How Magna Used project44 to Create a Just-in-Sequence Delivery
Customer Company Size
Large Corporate
Region
- Europe
Product
- project44 Advanced Visibility Platform™
Tech Stack
- Telematics
- Real-time Visibility
- Data Normalization
- Automated Data Flows
Implementation Scale
- Enterprise-wide Deployment
Impact Metrics
- Cost Savings
- Customer Satisfaction
- Productivity Improvements
Technology Category
- Analytics & Modeling - Real Time Analytics
- Functional Applications - Fleet Management Systems (FMS)
Applicable Industries
- Automotive
Applicable Functions
- Logistics & Transportation
Use Cases
- Fleet Management
- Real-Time Location System (RTLS)
- Supply Chain Visibility
Services
- Software Design & Engineering Services
- System Integration
About The Customer
Magna is the leading brand-independent engineering and manufacturing partner for OEMs and has over 100 years of vehicle production experience. They are focused on delivering superior value to customers through innovative processes and world-class manufacturing.
The Challenge
Magna’s Smart Factory required just-in-sequence deliveries from a range of locations. To ensure deliveries arrived in sequence regardless of origin, Magna Steyr needed a smarter way to access over-the-road visibility in the European market.
The Solution
Supported by project44, Magna introduced the first Industry 4.0 driven Long Distance Just-in-Sequence (LD-JIS) logistics program for its Smart Factory concept. Magna chose project44’s Advanced Visibility Platform™ to collect, normalize, and enrich telematics data, then feed it to their systems. Magna’s dispatchers and controllers now have real-time visibility of all JIS supplies and can monitor planned routes and deviations of JIS trucks and trailers. Data flows are now automated, eliminating costly errors from human intervention. Magna is now ensured that loads in the supply chain will arrive on the right vehicle, in sequence, and on time.
Operational Impact
Quantitative Benefit
Case Study missing?
Start adding your own!
Register with your work email and create a new case study profile for your business.
Related Case Studies.
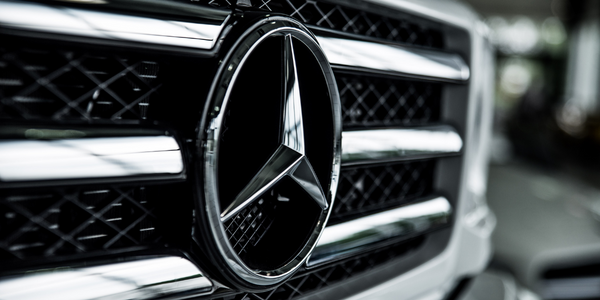
Case Study
Integral Plant Maintenance
Mercedes-Benz and his partner GAZ chose Siemens to be its maintenance partner at a new engine plant in Yaroslavl, Russia. The new plant offers a capacity to manufacture diesel engines for the Russian market, for locally produced Sprinter Classic. In addition to engines for the local market, the Yaroslavl plant will also produce spare parts. Mercedes-Benz Russia and his partner needed a service partner in order to ensure the operation of these lines in a maintenance partnership arrangement. The challenges included coordinating the entire maintenance management operation, in particular inspections, corrective and predictive maintenance activities, and the optimizing spare parts management. Siemens developed a customized maintenance solution that includes all electronic and mechanical maintenance activities (Integral Plant Maintenance).
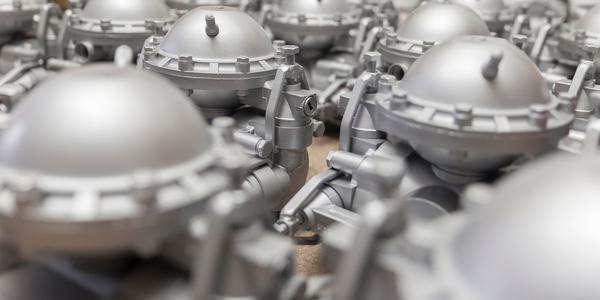
Case Study
Monitoring of Pressure Pumps in Automotive Industry
A large German/American producer of auto parts uses high-pressure pumps to deburr machined parts as a part of its production and quality check process. They decided to monitor these pumps to make sure they work properly and that they can see any indications leading to a potential failure before it affects their process.