Happigo Advances Supply Chain with Manhattan Associates
Customer Company Size
Large Corporate
Region
- Asia
Country
- China
Product
- Manhattan Warehouse Management System (WMS)
Tech Stack
- Radio-Frequency Enabled WMS
Implementation Scale
- Enterprise-wide Deployment
Impact Metrics
- Productivity Improvements
- Customer Satisfaction
- Cost Savings
Technology Category
- Functional Applications - Warehouse Management Systems (WMS)
Applicable Industries
- Retail
- E-Commerce
Applicable Functions
- Warehouse & Inventory Management
- Logistics & Transportation
Use Cases
- Inventory Management
- Warehouse Automation
- Supply Chain Visibility
Services
- System Integration
- Training
About The Customer
Founded by Hunan Broadcasting System in 2005, Happigo Home Shopping Co., Ltd., is a modern direct selling retailer using a variety of media channels including television, Internet, catalogues, telephone, and mobile devices to create an integrated selling platform. It is a market leader in China’s B2C market and a pioneer in the new generation of e-commerce in China. Happigo is the first live TV home shopping company in Mainland China, having gone out with its inaugural broadcast in March 2006. Based in Changsha, the capital city of Hunan Province, Happigo has built two warehouses in the city with a total storage area of 376,737 square feet. With a constantly growing demand for its products, Happigo aims to improve business performance across all channels in the coming years with a vision to become the top player in China’s e-commerce industry and to become a publicly listed company.
The Challenge
Happigo needed a scalable supply chain technology platform to support its growth ambitions and enhance its overall service offering. The existing ERP system and paper-based processes were insufficient to meet the future needs of the business, leading to inefficiencies and inaccuracies. To achieve its goals and support its fast-expanding business, Happigo realized it needed a more specialized system to meet its projected future growth. The company required a comprehensive, flexible, and scalable system to support its continued business expansion.
The Solution
After a competitive selection process, Happigo selected Manhattan’s Warehouse Management System (WMS) for its two warehouses in Changsha. Manhattan’s WMS provides best-in-class logistics technology that delivers measurable ROI and productivity gains in inventory, labor, physical space, time, and costs. The system efficiently manages multi-channel distribution operations and helps user companies to quickly respond to shifting demand patterns. It enhances inventory management by increasing accuracy levels and stock flow-through speeds, improves service levels by optimizing the order fulfillment process, and saves money by enabling productivity improvements throughout a company’s distribution operation. Following a period of discussion, system design, onsite testing, and staff training, the project went live. Upon completion of the deployment, Happigo had enhanced its order processing capability, increased picking efficiency, improved inventory visibility, and streamlined communication with its suppliers.
Operational Impact
Quantitative Benefit
Case Study missing?
Start adding your own!
Register with your work email and create a new case study profile for your business.
Related Case Studies.
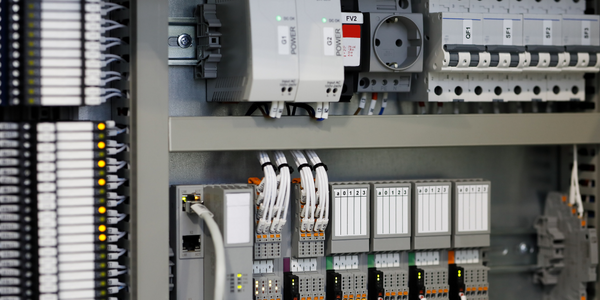
Case Study
Improving Production Line Efficiency with Ethernet Micro RTU Controller
Moxa was asked to provide a connectivity solution for one of the world's leading cosmetics companies. This multinational corporation, with retail presence in 130 countries, 23 global braches, and over 66,000 employees, sought to improve the efficiency of their production process by migrating from manual monitoring to an automatic productivity monitoring system. The production line was being monitored by ABB Real-TPI, a factory information system that offers data collection and analysis to improve plant efficiency. Due to software limitations, the customer needed an OPC server and a corresponding I/O solution to collect data from additional sensor devices for the Real-TPI system. The goal is to enable the factory information system to more thoroughly collect data from every corner of the production line. This will improve its ability to measure Overall Equipment Effectiveness (OEE) and translate into increased production efficiencies. System Requirements • Instant status updates while still consuming minimal bandwidth to relieve strain on limited factory networks • Interoperable with ABB Real-TPI • Small form factor appropriate for deployment where space is scarce • Remote software management and configuration to simplify operations
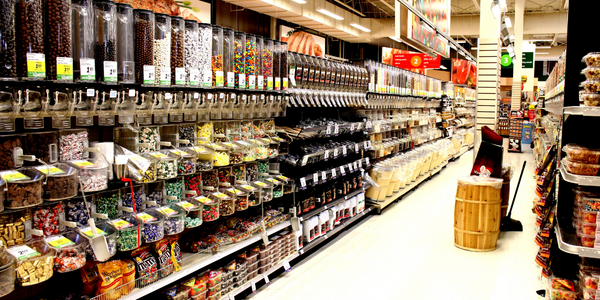
Case Study
How Sirqul’s IoT Platform is Crafting Carrefour’s New In-Store Experiences
Carrefour Taiwan’s goal is to be completely digital by end of 2018. Out-dated manual methods for analysis and assumptions limited Carrefour’s ability to change the customer experience and were void of real-time decision-making capabilities. Rather than relying solely on sales data, assumptions, and disparate systems, Carrefour Taiwan’s CEO led an initiative to find a connected IoT solution that could give the team the ability to make real-time changes and more informed decisions. Prior to implementing, Carrefour struggled to address their conversion rates and did not have the proper insights into the customer decision-making process nor how to make an immediate impact without losing customer confidence.
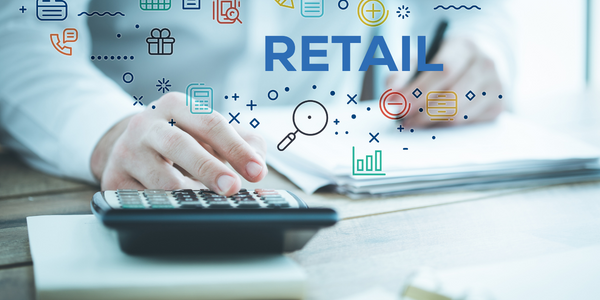
Case Study
Digital Retail Security Solutions
Sennco wanted to help its retail customers increase sales and profits by developing an innovative alarm system as opposed to conventional connected alarms that are permanently tethered to display products. These traditional security systems were cumbersome and intrusive to the customer shopping experience. Additionally, they provided no useful data or analytics.
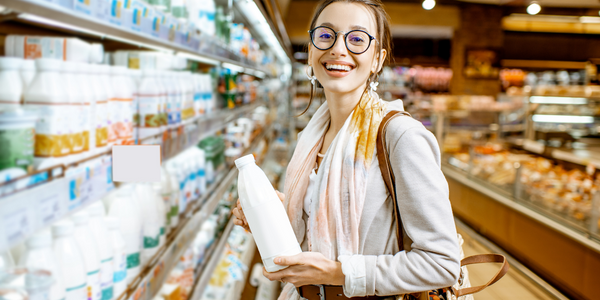
Case Study
Ensures Cold Milk in Your Supermarket
As of 2014, AK-Centralen has over 1,500 Danish supermarkets equipped, and utilizes 16 operators, and is open 24 hours a day, 365 days a year. AK-Centralen needed the ability to monitor the cooling alarms from around the country, 24 hours a day, 365 days a year. Each and every time the door to a milk cooler or a freezer does not close properly, an alarm goes off on a computer screen in a control building in southwestern Odense. This type of alarm will go off approximately 140,000 times per year, equating to roughly 400 alarms in a 24-hour period. Should an alarm go off, then there is only a limited amount of time to act before dairy products or frozen pizza must be disposed of, and this type of waste can quickly start to cost a supermarket a great deal of money.
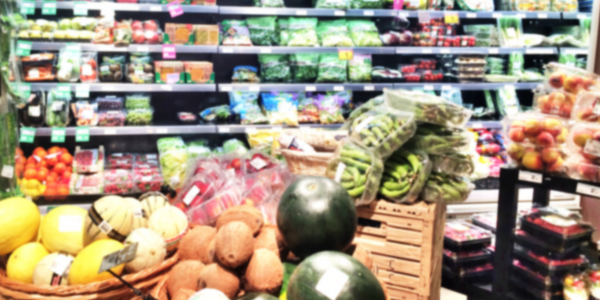
Case Study
Supermarket Energy Savings
The client had previously deployed a one-meter-per-store monitoring program. Given the manner in which energy consumption changes with external temperature, hour of the day, day of week and month of year, a single meter solution lacked the ability to detect the difference between a true problem and a changing store environment. Most importantly, a single meter solution could never identify root cause of energy consumption changes. This approach never reduced the number of truck-rolls or man-hours required to find and resolve issues.