Customer Company Size
Large Corporate
Region
- Europe
- America
- Asia
Country
- Italy
- Brazil
- Indonesia
- Mexico
Product
- Versalis
Tech Stack
- Industry 4.0
Implementation Scale
- Enterprise-wide Deployment
Impact Metrics
- Productivity Improvements
- Cost Savings
- Customer Satisfaction
Technology Category
- Functional Applications - Manufacturing Execution Systems (MES)
- Functional Applications - Product Lifecycle Management Systems (PLM)
- Functional Applications - Remote Monitoring & Control Systems
Applicable Industries
- Automotive
Applicable Functions
- Discrete Manufacturing
- Product Research & Development
- Quality Assurance
Use Cases
- Manufacturing System Automation
- Predictive Maintenance
- Process Control & Optimization
Services
- System Integration
- Software Design & Engineering Services
- Training
About The Customer
Headquartered in Arzignano, Italy—Europe’s largest leather tanning district—family-owned and -operated Gruppo Mastrotto produces more than 21 million m2 of high-quality bovine leathers annually for the garment, footwear, leather goods, furniture, marine seating, and aviation industries. With consolidated turnover of €460 million and a worldwide workforce of 2,400, the company runs operations at 20 manufacturing and logistics plants in Italy, Brazil, Indonesia, Mexico, and Tunisia. Gruppo Mastrotto’s automotive business unit, run as a standalone entity since 2009, continues to undergo rapid expansion to become more responsive to vehicle manufacturers.
The Challenge
Gruppo Mastrotto’s automotive business unit needed to enhance its manufacturing flexibility to meet evolving customer requirements brought about by rapidly changing consumer expectations. The tannery sought to optimize workflow and processes at its high-intensity automotive manufacturing plants, located on three different continents. The company faced the challenge of handling a high number of engineering changes associated with program changeovers, which required quick and seamless pattern development directly from digital files to eliminate costly retooling that could take several months.
The Solution
To modernize Gruppo Mastrotto’s cutting rooms, a decision was made to adopt the Versalis digital leather-cutting solution in 2014. Following a series of benchmark tests, Lectra was chosen as the partner to help raise the skill level in the automotive cutting room. Implementation of the advanced leather-cutting solution Versalis has enabled flexible automated cutting as well as optimized material usage, even for the most complex designs. The new, digitalized model of leather-cutting efficiency is currently being applied to sites in Mexico and Tunisia. Lectra’s best-in-class technology, unique business expertise, and worldwide capabilities enable the company to support Gruppo Mastrotto on all of the international markets where it operates, helping the tannery to achieve its continuous improvement goals and fulfill its ambitious expansion strategy.
Operational Impact
Quantitative Benefit
Case Study missing?
Start adding your own!
Register with your work email and create a new case study profile for your business.
Related Case Studies.
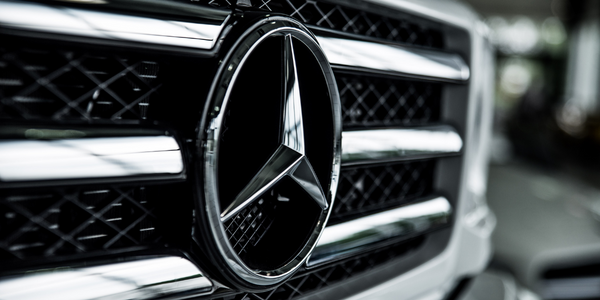
Case Study
Integral Plant Maintenance
Mercedes-Benz and his partner GAZ chose Siemens to be its maintenance partner at a new engine plant in Yaroslavl, Russia. The new plant offers a capacity to manufacture diesel engines for the Russian market, for locally produced Sprinter Classic. In addition to engines for the local market, the Yaroslavl plant will also produce spare parts. Mercedes-Benz Russia and his partner needed a service partner in order to ensure the operation of these lines in a maintenance partnership arrangement. The challenges included coordinating the entire maintenance management operation, in particular inspections, corrective and predictive maintenance activities, and the optimizing spare parts management. Siemens developed a customized maintenance solution that includes all electronic and mechanical maintenance activities (Integral Plant Maintenance).
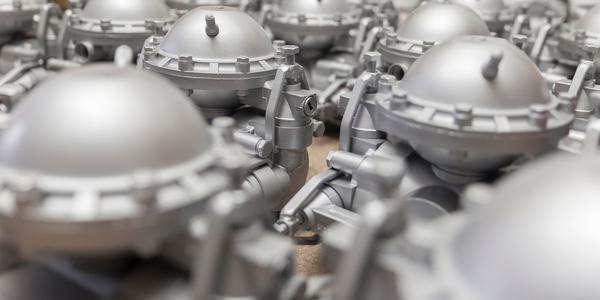
Case Study
Monitoring of Pressure Pumps in Automotive Industry
A large German/American producer of auto parts uses high-pressure pumps to deburr machined parts as a part of its production and quality check process. They decided to monitor these pumps to make sure they work properly and that they can see any indications leading to a potential failure before it affects their process.