Customer Company Size
Large Corporate
Region
- America
Country
- United States
Product
- FORCAM FORCE
Tech Stack
- Advanced Shop Floor Management Technology
- ERP SAP
Implementation Scale
- Enterprise-wide Deployment
Impact Metrics
- Cost Savings
- Productivity Improvements
- Customer Satisfaction
- Energy Saving
- Waste Reduction
Technology Category
- Functional Applications - Manufacturing Execution Systems (MES)
- Analytics & Modeling - Predictive Analytics
- Application Infrastructure & Middleware - Data Visualization
Applicable Industries
- Aerospace
Applicable Functions
- Process Manufacturing
- Maintenance
- Quality Assurance
Use Cases
- Machine Condition Monitoring
- Predictive Maintenance
- Energy Management System
- Process Control & Optimization
- Real-Time Location System (RTLS)
Services
- System Integration
- Data Science Services
- Training
About The Customer
GKN Aerospace is one of the world's largest independent first-tier aerospace suppliers, providing complex, high-performance, high-value integrated metallic and composite assemblies for aero structures and engine products. Based in Newington, Connecticut, USA, the company has a reputation for investing in technological innovation to bring real and practical benefits to their customers, aircraft operators, and passengers. GKN Aerospace's Engine Systems division, which accounted for 50% of sales in 2013, operates in a low-volume, high-mix environment and has close strategic partnerships with major OEMs and tier-one suppliers such as General Electric, Pratt & Whitney, Rolls-Royce, Snecma, and MTU.
The Challenge
GKN Aerospace, a leading aerospace supplier, faced the challenge of improving manufacturing productivity in a low-volume, high-mix environment. The company needed a solution to enhance machine utilization, reduce operation time, and improve overall efficiency. With strategic partnerships with major OEMs and tier-one suppliers, GKN Aerospace required a robust system to manage and analyze machine data in real-time, allowing for timely interventions and quality improvements. The company also aimed to integrate this system with their existing ERP SAP to further streamline operations and achieve continuous improvement.
The Solution
GKN Aerospace implemented FORCAM’s Advanced Shop Floor Management Technology, FORCAM FORCE, to improve manufacturing productivity. This technology allows the company to see production data in real-time, analyze machine states, and make timely interventions for quality improvements. The system provides a visual display on the plant floor, showing status information and enabling operators to signal line status based on color codes. This real-time visibility helps in increasing throughput efficiency and overall equipment effectiveness (OEE). The technology also supports continuous improvement activities by providing instant feedback on performance changes. In Phase 2, GKN Aerospace plans to integrate FORCAM FORCE with their ERP SAP to further enhance operational efficiency.
Operational Impact
Quantitative Benefit
Case Study missing?
Start adding your own!
Register with your work email and create a new case study profile for your business.
Related Case Studies.
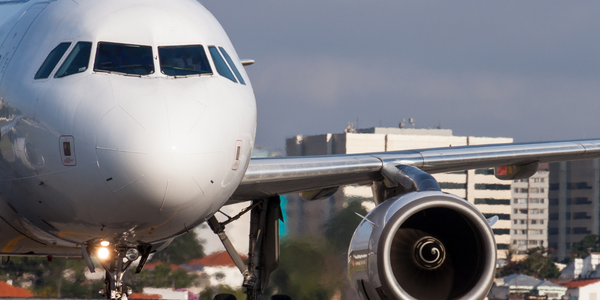
Case Study
Airbus Soars with Wearable Technology
Building an Airbus aircraft involves complex manufacturing processes consisting of thousands of moving parts. Speed and accuracy are critical to business and competitive advantage. Improvements in both would have high impact on Airbus’ bottom line. Airbus wanted to help operators reduce the complexity of assembling cabin seats and decrease the time required to complete this task.
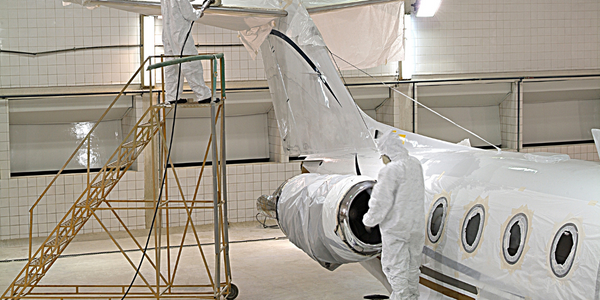
Case Study
Aircraft Predictive Maintenance and Workflow Optimization
First, aircraft manufacturer have trouble monitoring the health of aircraft systems with health prognostics and deliver predictive maintenance insights. Second, aircraft manufacturer wants a solution that can provide an in-context advisory and align job assignments to match technician experience and expertise.
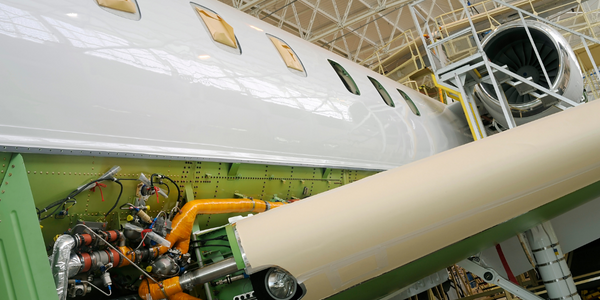
Case Study
Aerospace & Defense Case Study Airbus
For the development of its new wide-body aircraft, Airbus needed to ensure quality and consistency across all internal and external stakeholders. Airbus had many challenges including a very aggressive development schedule and the need to ramp up production quickly to satisfy their delivery commitments. The lack of communication extended design time and introduced errors that drove up costs.
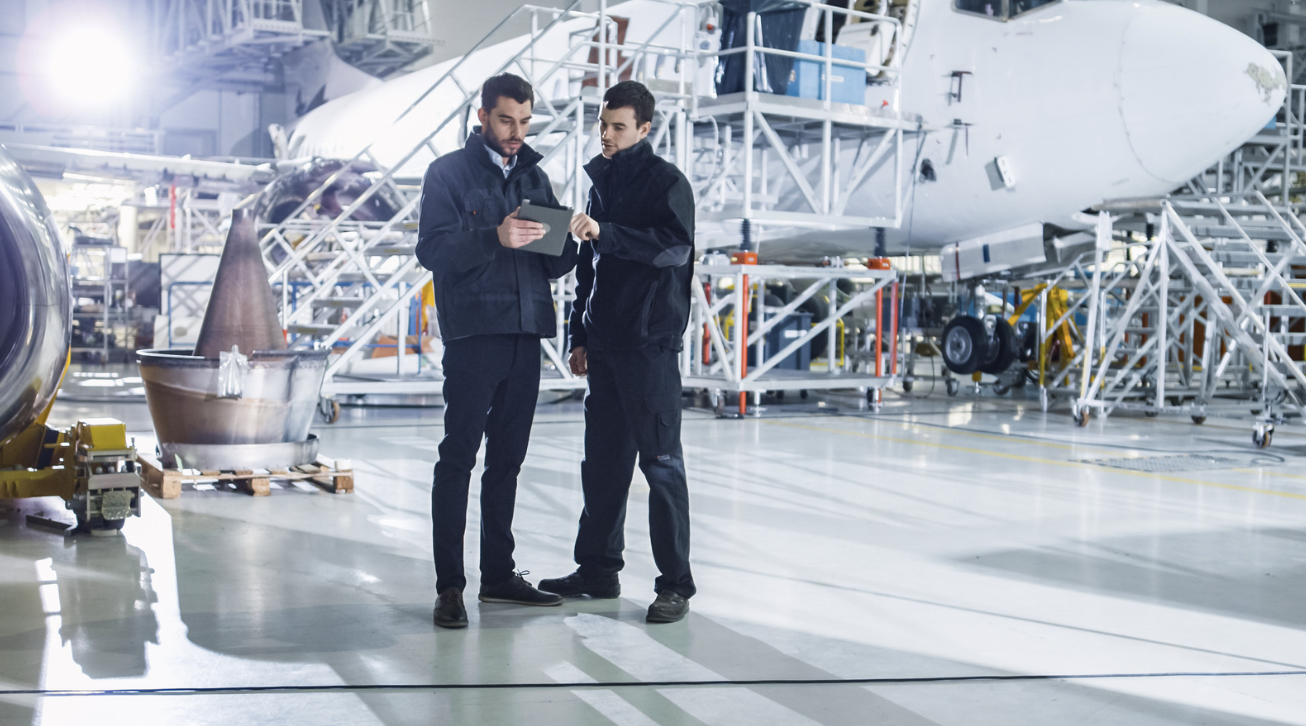
Case Study
Developing Smart Tools for the Airbus Factory
Manufacturing and assembly of aircraft, which involves tens of thousands of steps that must be followed by the operators, and a single mistake in the process could cost hundreds of thousands of dollars to fix, makes the room for error very small.
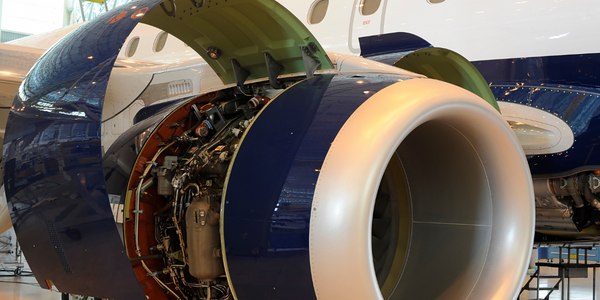
Case Study
Accelerate Production for Spirit AeroSystems
The manufacture and assembly of massive fuselage assemblies and other large structures generates a river of data. In fact, the bill of materials for a single fuselage alone can be millions of rows of data. In-house production processes and testing, as well as other manufacturers and customers created data flows that overwhelmed previous processes and information systems. Spirit’s customer base had grown substantially since their 2005 divestiture from Boeing, resulting in a $41 billion backlog of orders to fill. To address this backlog, meet increased customer demands and minimize additional capital investment, the company needed a way to improve throughput in the existing operational footprint. Spirit had a requirement from customers to increase fuselage production by 30%. To accomplish this goal, Spirit needed real-time information on its value chain and workflow. However, the two terabytes of data being pulled from their SAP ECC was unmanageable and overloaded their business warehouse. It had become time-consuming and difficult to pull aggregate data, disaggregate it for the needed information and then reassemble to create a report. During the 6-8 hours it took to build a report, another work shift (they run three per day) would have already taken place, thus the report content was out-of-date before it was ever delivered. As a result, supervisors often had to rely on manual efforts to provide charts, reports and analysis.