Engineering the Perfect Fit
Customer Company Size
Large Corporate
Region
- America
Country
- United States
Product
- Raymond® lift trucks
- Raymond Swing-Reach® trucks
- Raymond orderpickers
- Raymond intelliguide™ wire guidance system
Tech Stack
- Wire-guided systems
- Magnet-based end of aisle slowdown
Implementation Scale
- Enterprise-wide Deployment
Impact Metrics
- Productivity Improvements
- Cost Savings
- Customer Satisfaction
Technology Category
- Functional Applications - Warehouse Management Systems (WMS)
- Automation & Control - Automation & Process Control Systems
Applicable Industries
- Consumer Goods
- Retail
Applicable Functions
- Warehouse & Inventory Management
- Logistics & Transportation
Use Cases
- Warehouse Automation
- Inventory Management
- Fleet Management
Services
- System Integration
- Training
- Hardware Design & Engineering Services
About The Customer
New Balance Athletic Shoe, Inc., based in Boston, MA, is a renowned company that designs and develops innovative, highly functional, and reliable shoes for both weekend warriors and serious athletes. The company operates three North American warehouses located in Ontario, CA; Compton, CA; and Lawrence, MA, which collectively process 26 million pairs of shoes per year. New Balance's commitment to quality and performance extends to its warehouse operations, where it seeks to maximize productivity and efficiency. The company values ergonomic design, comfort, and operator productivity, which aligns with its philosophy of creating footwear that fits a wide range of activities and sizes.
The Challenge
Needing to maximize productivity in order to move the millions of athletic shoes sold annually, New Balance faced the challenge of selecting the right equipment for its various warehouse applications. The company required lift trucks that could handle the extensive traffic and narrow aisles in its warehouses, particularly in the Lawrence facility. Additionally, the Ontario facility had concerns with its extensive traffic and aisles that are open at both ends, necessitating a solution to aid operators in stopping or slowing prior to exiting the aisle. Another challenge was to reduce truck downtime for battery changes to maintain high productivity levels.
The Solution
To address its challenges, New Balance partnered with Abel Integrated Handling Systems, the Raymond Dealership in Lawrence, and its Director of Sales, Mike Petinge. Together, they selected eight counterbalanced trucks for receiving, six wire-guided Swing-Reach® trucks, and 11 pallet trucks for pick and put away in narrow aisles. Additionally, 26 wire-guided orderpickers were chosen for case picking. To further enhance efficiency, Petinge recommended Raymond’s exclusive intelliguide™ wire guidance system, which frees operators from steering responsibilities in very narrow aisles. This system quickly and reliably engages guide signals, providing excellent tracking and stability, which was particularly beneficial for the Lawrence warehouse. For the Ontario facility, Petinge addressed the issue of extensive traffic and open-ended aisles by equipping the trucks with magnets for end-of-aisle slowdown, aiding operators in stopping or slowing prior to exiting the aisle. This comprehensive approach ensured that New Balance's warehouses were equipped with the right tools to maximize productivity and efficiency.
Operational Impact
Quantitative Benefit
Case Study missing?
Start adding your own!
Register with your work email and create a new case study profile for your business.
Related Case Studies.
.png)
Case Study
Improving Vending Machine Profitability with the Internet of Things (IoT)
The vending industry is undergoing a sea change, taking advantage of new technologies to go beyond just delivering snacks to creating a new retail location. Intelligent vending machines can be found in many public locations as well as company facilities, selling different types of goods and services, including even computer accessories, gold bars, tickets, and office supplies. With increasing sophistication, they may also provide time- and location-based data pertaining to sales, inventory, and customer preferences. But at the end of the day, vending machine operators know greater profitability is driven by higher sales and lower operating costs.
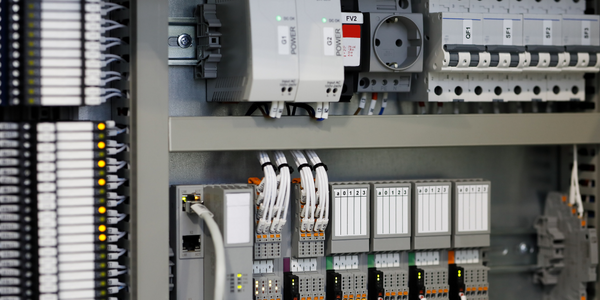
Case Study
Improving Production Line Efficiency with Ethernet Micro RTU Controller
Moxa was asked to provide a connectivity solution for one of the world's leading cosmetics companies. This multinational corporation, with retail presence in 130 countries, 23 global braches, and over 66,000 employees, sought to improve the efficiency of their production process by migrating from manual monitoring to an automatic productivity monitoring system. The production line was being monitored by ABB Real-TPI, a factory information system that offers data collection and analysis to improve plant efficiency. Due to software limitations, the customer needed an OPC server and a corresponding I/O solution to collect data from additional sensor devices for the Real-TPI system. The goal is to enable the factory information system to more thoroughly collect data from every corner of the production line. This will improve its ability to measure Overall Equipment Effectiveness (OEE) and translate into increased production efficiencies. System Requirements • Instant status updates while still consuming minimal bandwidth to relieve strain on limited factory networks • Interoperable with ABB Real-TPI • Small form factor appropriate for deployment where space is scarce • Remote software management and configuration to simplify operations
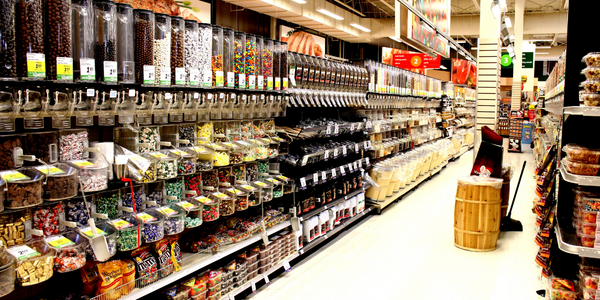
Case Study
How Sirqul’s IoT Platform is Crafting Carrefour’s New In-Store Experiences
Carrefour Taiwan’s goal is to be completely digital by end of 2018. Out-dated manual methods for analysis and assumptions limited Carrefour’s ability to change the customer experience and were void of real-time decision-making capabilities. Rather than relying solely on sales data, assumptions, and disparate systems, Carrefour Taiwan’s CEO led an initiative to find a connected IoT solution that could give the team the ability to make real-time changes and more informed decisions. Prior to implementing, Carrefour struggled to address their conversion rates and did not have the proper insights into the customer decision-making process nor how to make an immediate impact without losing customer confidence.
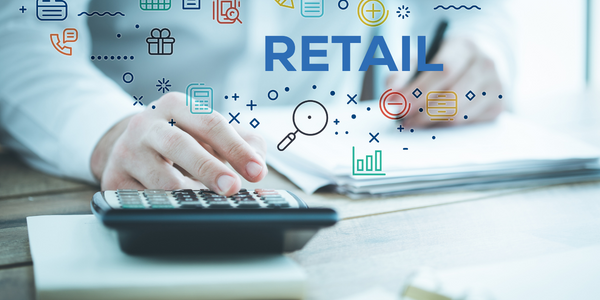
Case Study
Digital Retail Security Solutions
Sennco wanted to help its retail customers increase sales and profits by developing an innovative alarm system as opposed to conventional connected alarms that are permanently tethered to display products. These traditional security systems were cumbersome and intrusive to the customer shopping experience. Additionally, they provided no useful data or analytics.