Technology Category
- Infrastructure as a Service (IaaS) - Public Cloud
- Platform as a Service (PaaS) - Application Development Platforms
Applicable Industries
- Mining
- Paper & Pulp
Applicable Functions
- Human Resources
Use Cases
- Inventory Management
- Security Claims Evaluation
Services
- System Integration
- Training
About The Customer
The National Geology and Mining Service (SERNAGEOMIN) is a public and technical body responsible for advising the Chilean Government’s Ministry of Mining on matters related to mining and geology. Its competencies include technical processes for mining safety inspections, accident investigation, sanctioning procedures, project review, advising the courts of justice on the constitution of mining properties, closure plan review, and training experts in mining safety. The geology area deals with issues related to chemical analysis, geoheritage, exploration projects, basic and applied geology mapping, and monitoring of the country’s volcanic activity. The institution was founded in 1980 and has over 500 employees.
The Challenge
The National Geology and Mining Service (SERNAGEOMIN), a public entity under the Ministry of Mining of the Government of Chile, was facing challenges in its administrative processes due to lack of digitalization. The exchange of information between different administrative offices and civil servants involved manual and paper-based processes, which were inefficient and time-consuming. Documents were sent by mail all over Chile for review, approval, and signing. The management of procedures was carried out traditionally, with filing cabinets and folders containing documents related to each of the investigations into accidents that occurred during mining operations. When an accident occurred, the paper documents related to the investigation and possible sanctions had to be transported by airmail to be reviewed by the competent authorities. The mining subdirectorate needed a traceability system that would allow complete and real-time tracking of all the tasks that are part of each of the processes, and that would support agile reporting and communication.
The Solution
SERNAGEOMIN selected AuraQuantic as the platform to digitalize its administrative processes. The seven departments that form SERNAGEOMIN’s Mining Subdirectorate started using AuraQuantic to varying extents. The subdirectorate has 16 active processes on AuraQuantic and plans to expand its use over the next few years. The applications are designed by a member of the institution who has been trained and certified by completing the AuraQuantic Training School’s e-learning courses, with support from the software’s consultancy team. The platform has allowed the institution to evolve very quickly. Some of the processes that the subdirectorate manages on AuraQuantic include Project Evaluation, Closure Plans, Mining Property, and Accident Investigation and Sanction Management. All accident investigations are now 100% digital on AuraQuantic, which has eliminated the use of paper. The entire workflow, from traceability to serving the mining companies, is now carried out digitally.
Operational Impact
Quantitative Benefit
Case Study missing?
Start adding your own!
Register with your work email and create a new case study profile for your business.
Related Case Studies.

Case Study
Wireless Improves Efficiency in Compressed Air Systems
Hollingsworth and Vose wanted to improve the efficiency of their compressed air system, lower the electricity expense component of manufacturing cost in their commodity industry, and conserve energy leading to lowered greenhouse gas emissions. Compressed air systems degrade over time and become leaky and inefficient. Hollingsworth and Vose wanted to increase the frequency of system inspections without paying the high cost of manual labor.
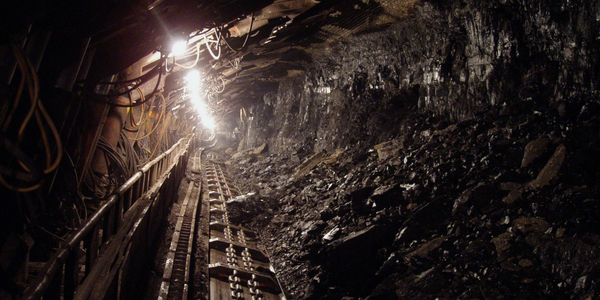
Case Study
Underground Mining Safety
The goal was to produce a safety system to monitor and support underground mining operations; existing systems were either too simple (i.e. phone line) or overly complex and expensive, inhibiting deployment, and providing little-to-no support in event of an accident. Given the dangerous nature of the mining work environment and the strict regulations placed on the industry, the solution would have to comply with Mine Safety and Health Administration (MSHA) regulations. Yet the product needed to allow for simple deployment to truly be a groundbreaking solution - increasing miner safety and changing daily operations for the better.
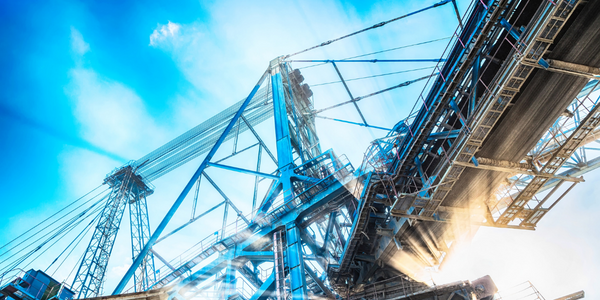
Case Study
Mining Firm Quadruples Production, with Internet of Everything
Dundee Precious Metal’s flagship mine, in Chelopech, Bulgaria, produces a gold, copper, and silver concentrate set a goal to increase production by 30%. Dundee wanted to increase production quality and output without increasing headcount and resources, improve miner safety, and minimize cost.
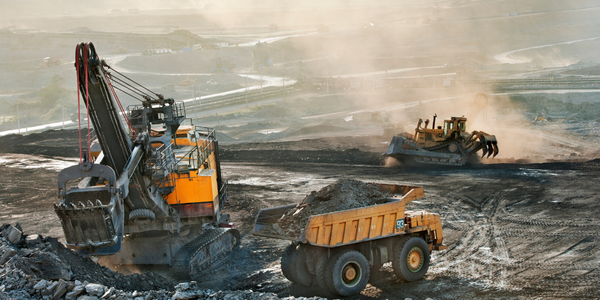
Case Study
Fastenal Builds the Future of Manufacturing with MachineMetrics
Fastenal's objective was to better understand their machine downtime, utilization, quality issues, and to embrace cutting-edge manufacturing technology/process improvement capabilities to bring their team to the next level. However, there was a lack of real-time data, visualization, and actionable insights made this transition impossible.
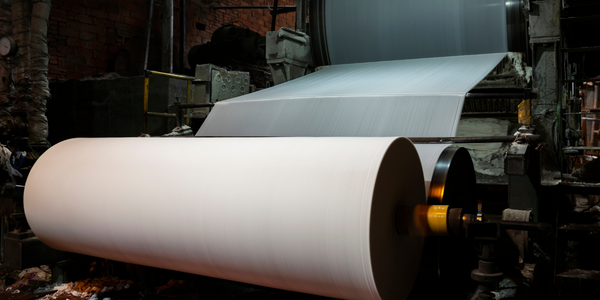
Case Study
Process Predictive Analysis in Pulp and Paper Mill
Common paper breaks consequently lead up to 60 minutes of downtime, delaying a potential $10K per hour of production value process. Thus, defective products cause financial and damage company's reputation. Improving quality and reducing defect rates can generate millions of dollars of revenue per year for your company.