Technology Category
- Analytics & Modeling - Real Time Analytics
- Platform as a Service (PaaS) - Application Development Platforms
Applicable Industries
- Automotive
- Retail
Applicable Functions
- Procurement
- Sales & Marketing
Use Cases
- Public Transportation Management
- Retail Store Automation
Services
- Cloud Planning, Design & Implementation Services
- System Integration
About The Customer
Arriva UK Bus (AUKB) is one of the UK’s largest and best-known transportation brands. It operates 5,900 buses across London, South East and North of England, and the Midlands and Wales. A subsidiary of Arriva, it provides tickets and travel information for using the bus network across the UK. As part of a broader company transformation, Arriva wanted to overhaul its digital experience for customers purchasing bus tickets and searching for travel information. With 90% of bus travel outside London still being purchased by cash, a seamless, enticing, easy-to-use digital experience was essential to drive behavior change and digital channel shift by travelers.
The Challenge
Arriva UK Bus (AUKB), one of the UK’s largest transportation brands, was facing a significant challenge with its digital experience for customers purchasing bus tickets and searching for travel information. The company's fragmented suite of journey planning and purchase tools were difficult for travelers to use. The company had two separate bus mobile apps: one for planning and one for retailing. Each regional operating company had its own discrete web experience. There were three separate web platforms for retail, planning, and marketing content. There was little to no correlation between the content on the different sites. Any content management actions on the site required significant custom development and manual input. The digital business was further impacted by the legacy technology running the content and retail platforms, with two different versions of EpiServer in use. The retail platform version had not been upgraded since the original sites were created, and the site also experienced Payment Card Industry (PCI) compliance issues. Finally, none of the digital platforms were scalable, with multi-day outages and problems caused by traffic spikes.
The Solution
AUKB partnered with ORM Digital to overhaul its digital strategy and roadmap. ORM helped AUKB develop a commercial business case for change, define and scope the digital ecosystem to support it, and then acted as system integrator to create the integrated digital marketing and retail solution powered by Acquia Cloud Platform and AWS. ORM engaged with a wide range of stakeholders from across AUKB business, from commercial, customer experience (CX) and call center leads to regional managers and central and regional marketing. They defined a content model and API architecture focused on giving users a connected experience, enriching the journey planning experience, and providing retail and journey options to users while they browsed marketing content. ORM configured Drupal CMS to serve content through a number of headless APIs, allowing a unique customer experience to be authored within the web application, where digital retail content (tickets, offers, journeys) could be positioned alongside relevant marketing information. The headless API was also used to provide content for the native apps, allowing content editors to manage content for multiple client types. This unique approach removed the need for the business to run two separate marketing and retail platforms and created a more seamless customer experience that converted at a higher rate. Arriva now has a single app and website using a core suite of components that have their content managed from one platform (Drupal CMS), where they can be reused and repurposed across each regional business. A more visual interface using maps with real-time journey data allows easy tracking of buses within their route and quick purchase through a streamlined booking flow.
Operational Impact
Quantitative Benefit
Case Study missing?
Start adding your own!
Register with your work email and create a new case study profile for your business.
Related Case Studies.
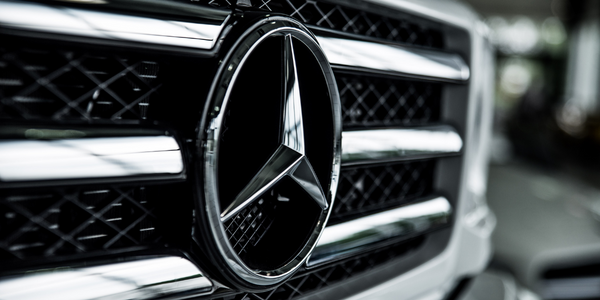
Case Study
Integral Plant Maintenance
Mercedes-Benz and his partner GAZ chose Siemens to be its maintenance partner at a new engine plant in Yaroslavl, Russia. The new plant offers a capacity to manufacture diesel engines for the Russian market, for locally produced Sprinter Classic. In addition to engines for the local market, the Yaroslavl plant will also produce spare parts. Mercedes-Benz Russia and his partner needed a service partner in order to ensure the operation of these lines in a maintenance partnership arrangement. The challenges included coordinating the entire maintenance management operation, in particular inspections, corrective and predictive maintenance activities, and the optimizing spare parts management. Siemens developed a customized maintenance solution that includes all electronic and mechanical maintenance activities (Integral Plant Maintenance).
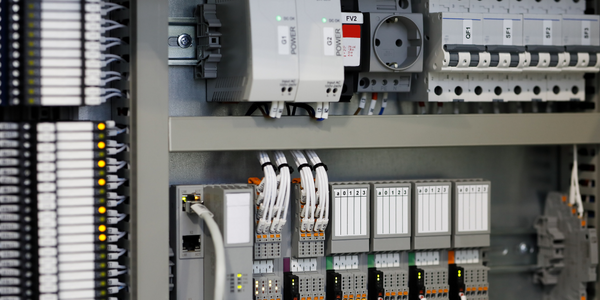
Case Study
Improving Production Line Efficiency with Ethernet Micro RTU Controller
Moxa was asked to provide a connectivity solution for one of the world's leading cosmetics companies. This multinational corporation, with retail presence in 130 countries, 23 global braches, and over 66,000 employees, sought to improve the efficiency of their production process by migrating from manual monitoring to an automatic productivity monitoring system. The production line was being monitored by ABB Real-TPI, a factory information system that offers data collection and analysis to improve plant efficiency. Due to software limitations, the customer needed an OPC server and a corresponding I/O solution to collect data from additional sensor devices for the Real-TPI system. The goal is to enable the factory information system to more thoroughly collect data from every corner of the production line. This will improve its ability to measure Overall Equipment Effectiveness (OEE) and translate into increased production efficiencies. System Requirements • Instant status updates while still consuming minimal bandwidth to relieve strain on limited factory networks • Interoperable with ABB Real-TPI • Small form factor appropriate for deployment where space is scarce • Remote software management and configuration to simplify operations