DeKalb Metal Finishing Enhances Efficiency and Quality with SoftExpert BPM
Customer Company Size
Mid-size Company
Region
- America
Country
- United States
Product
- SoftExpert BPM
Tech Stack
- Business Process Management (BPM)
Implementation Scale
- Enterprise-wide Deployment
Impact Metrics
- Cost Savings
- Productivity Improvements
- Customer Satisfaction
Technology Category
- Platform as a Service (PaaS) - Application Development Platforms
Applicable Industries
- Automotive
Applicable Functions
- Process Manufacturing
- Quality Assurance
Use Cases
- Process Control & Optimization
- Predictive Quality Analytics
Services
- System Integration
- Training
About The Customer
DeKalb Metal Finishing has been a key player in the electroplating and metal finishing industry for over 70 years, primarily serving the automotive sector along with other industries. The company is dedicated to maintaining high standards of quality, sustainability, and ethical practices, as evidenced by their certifications such as IATF 16949, CQI-11 Assessment, Conflict Minerals, and ROHS Compliance Letter. DeKalb's long-standing reputation is built on their commitment to delivering superior metal finishing services while adhering to stringent industry standards.
The Challenge
DeKalb Metal Finishing identified inefficiencies in their business operations that were affecting process quality and increasing costs. The company needed a robust solution to streamline processes, enhance quality, and reduce operational costs to maintain their commitment to quality, sustainability, and ethics.
The Solution
DeKalb Metal Finishing implemented SoftExpert BPM to address the inefficiencies in their processes. This solution was crucial in achieving the process approach mandated by the IATF 16949 certification. By leveraging SoftExpert BPM, DeKalb was able to identify and rectify areas of inefficiency, leading to significant improvements in their operational processes. The continuous improvement facilitated by the BPM solution not only enhanced the quality of their services but also resulted in cost reductions for both DeKalb and their customers.
Operational Impact
Case Study missing?
Start adding your own!
Register with your work email and create a new case study profile for your business.
Related Case Studies.
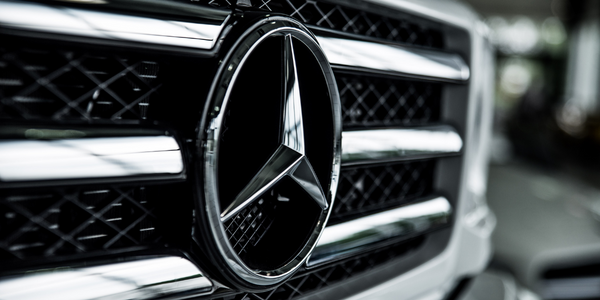
Case Study
Integral Plant Maintenance
Mercedes-Benz and his partner GAZ chose Siemens to be its maintenance partner at a new engine plant in Yaroslavl, Russia. The new plant offers a capacity to manufacture diesel engines for the Russian market, for locally produced Sprinter Classic. In addition to engines for the local market, the Yaroslavl plant will also produce spare parts. Mercedes-Benz Russia and his partner needed a service partner in order to ensure the operation of these lines in a maintenance partnership arrangement. The challenges included coordinating the entire maintenance management operation, in particular inspections, corrective and predictive maintenance activities, and the optimizing spare parts management. Siemens developed a customized maintenance solution that includes all electronic and mechanical maintenance activities (Integral Plant Maintenance).
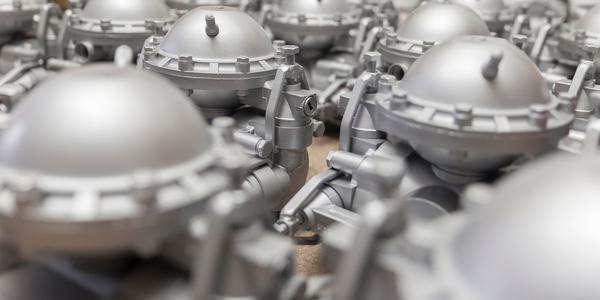
Case Study
Monitoring of Pressure Pumps in Automotive Industry
A large German/American producer of auto parts uses high-pressure pumps to deburr machined parts as a part of its production and quality check process. They decided to monitor these pumps to make sure they work properly and that they can see any indications leading to a potential failure before it affects their process.