Technology Category
- Platform as a Service (PaaS) - Application Development Platforms
- Sensors - Electrical Conductivity Sensors
Applicable Industries
- Electrical Grids
- Electronics
Applicable Functions
- Maintenance
- Product Research & Development
Use Cases
- Inventory Management
- Personnel Tracking & Monitoring
Services
- Software Design & Engineering Services
- System Integration
About The Customer
Dah Chong Hong (DCH) is a leading trading and distribution company based in Hong Kong with over 70 years of experience. The company has a workforce of 16,000 employees and operates in 13 Asian markets. DCH provides goods and services through five primary business units, including motor, food, healthcare, electrical appliances, and logistics. The company's IT team, led by Chief Information Officer, Alan Chung, comprises around 230 specialists serving the different business units.
The Challenge
Dah Chong Hong (DCH), a Hong Kong-based conglomerate with a presence in 13 Asian markets, faced the challenge of integrating IT systems across its five business units. The company's IT landscape was highly fragmented, with each unit developing its own applications tailored to its unique challenges. This resulted in distributed and inconsistent data that was slow and costly to consolidate. The company also relied heavily on paper-based processes. The management needed a centralized view of processes across the organization to make informed decisions and respond to market changes on time. One of the processes that needed improvement was the electrical appliance repair service, which was highly manual and inefficient, involving phone appointments, onsite cash payments, and a complex billing procedure that took about a month to complete.
The Solution
To address these challenges, DCH adopted OutSystems in 2021, a flexible and agile application development platform. The company developed the 'DCH Smart Toolbox App - DigiFix', an end-to-end electrical appliances customer and field service support platform. This platform transformed the customer and management experiences by automating the communication between customers, technicians, and DCH staff. Customers could now place bookings, get quotes, and request after-sales service online. The platform also provided real-time access to all the information needed for the staff to work efficiently. In addition to the DigiFix platform, DCH used OutSystems to replace legacy workflow systems while standardizing and improving processes. These included a new digital workspace, a new HR & finance portal, and internal workflow systems that replaced legacy Notes Domino applications.
Operational Impact
Quantitative Benefit
Case Study missing?
Start adding your own!
Register with your work email and create a new case study profile for your business.
Related Case Studies.

Case Study
Remote Temperature Monitoring of Perishable Goods Saves Money
RMONI was facing temperature monitoring challenges in a cold chain business. A cold chain must be established and maintained to ensure goods have been properly refrigerated during every step of the process, making temperature monitoring a critical business function. Manual registration practice can be very costly, labor intensive and prone to mistakes.
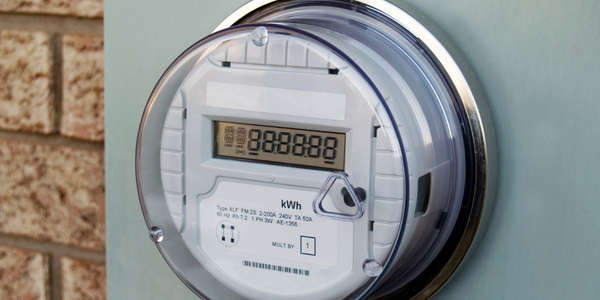
Case Study
Hydro One Leads the Way In Smart Meter Development
In 2010, Ontario’s energy board mandated that time-of-use (TOU) pricing for consumers be available for all consumers on a regulated price plan. To meet this requirement, Hydro One needed to quickly deploy a smart meter and intelligent communications network solution to meet the provincial government’s requirement at a low cost. The network needed to cover Hydro One’s expansive service territory, which has a land mass twice the size of Texas, and its customers live in a mix of urban, rural, and remote areas, some places only accessible by air, rail, boat or snowmobile. Most importantly, the network needed to enable future enterprise-wide business efficiencies, modernization of distribution infrastructure and enhanced customer service. To meet these needs, Hydro One conceptualized an end-to-end solution leveraging open standards and Internet Protocols (IP) at all communication levels. The utility drew upon industry leaders like Trilliant to realize this vision.
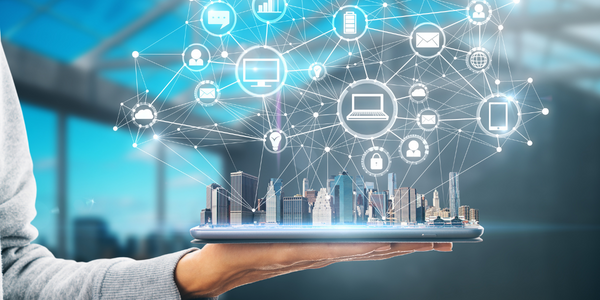
Case Study
Selling more with Whirlpool
Whirlpool wanted to add connectivity to appliances and transform the company's relationship with customers. Traditionally, Whirlpool interaction with customers was limited to purchases made once every ten years. Connected washer and dryers provide exciting new features like remote management of start times and inter-machine communication.
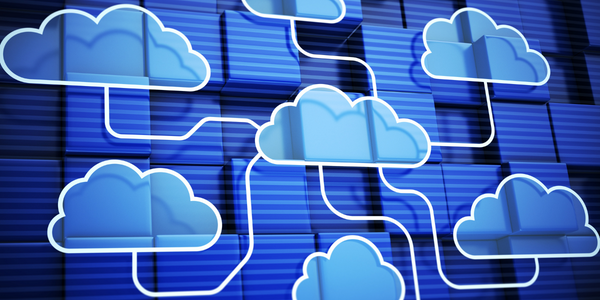
Case Study
Cloud Solution for Energy Management Platform-Schneider Electric
Schneider Electric required a cloud solution for its energy management platform to manage high computational operations, which were essential for catering to client requirements. As the business involves storage and analysis of huge amounts of data, the company also needed a convenient and scalable storage solution to facilitate operations efficiently.