Customer Company Size
Large Corporate
Country
- Germany
Product
- IBM Decision Optimization Center
Tech Stack
- Data Warehousing
- ERP
- Production Planning
- Materials Management
- Quality Management
Implementation Scale
- Enterprise-wide Deployment
Impact Metrics
- Productivity Improvements
- Cost Savings
Technology Category
- Analytics & Modeling - Predictive Analytics
- Application Infrastructure & Middleware - Data Exchange & Integration
Applicable Industries
- Automotive
Applicable Functions
- Discrete Manufacturing
- Product Research & Development
Use Cases
- Predictive Maintenance
- Manufacturing System Automation
Services
- Cloud Planning, Design & Implementation Services
- Data Science Services
About The Customer
Continental Tires is a major global tire manufacturer, generating annual revenues of around EUR9.8 billion and employing around 47,500 people. Continental Tires is a division of Continental AG, a German firm that ranks among the top five automotive suppliers worldwide. The company produces more than 10,000 different types of tires to fit a huge range of vehicles, each of which has different requirements, purposes, and target markets. Since tire manufacturing is a machine- and capital-intensive process, smart utilization of that huge investment is critical.
The Challenge
Continental Tires, a major global tire manufacturer, was facing inefficiencies in its production landscape, which manufactures 10,000 different products. The company was using manual, spreadsheet-based allocation of products to production plants, which was extremely complex and time-consuming. The process was entirely dependent on the know-how and experience of the people driving it and used no form of computer-aided optimization. Since data could not be transferred between documents automatically, it was also easy to make mistakes. The company planned production budgets annually and at a fairly high level to lighten the burden this process placed on its planners. But since the company launches 1,000 new products every year, even this method was becoming unviable.
The Solution
Continental Tires decided to support and improve planning with an optimization solution called Future Allocation and Capacity Tracking (FACT), which is based on IBM® Decision Optimization Center software. The company joined forces with IBM Global Business Services® and IBM Software Group Lab Services to complete a smooth implementation of the new solution. FACT captures information related to manufacturing – including product specifications, machine capacities at individual plants, and staff planning through shift allocations – from back-end systems. The back-end systems include Forecasting, Data Warehouses, and ERP modules such as Production Planning, Materials Management, Quality Management, and other systems. Since data is pulled directly from source systems, the risk of errors from manual transfer has been significantly reduced. The solution then performs highly complex mathematical optimization calculations to help planners decide which plants should make which products to obtain the greatest possible demand fulfillment and cost-efficiency.
Operational Impact
Quantitative Benefit
Case Study missing?
Start adding your own!
Register with your work email and create a new case study profile for your business.
Related Case Studies.
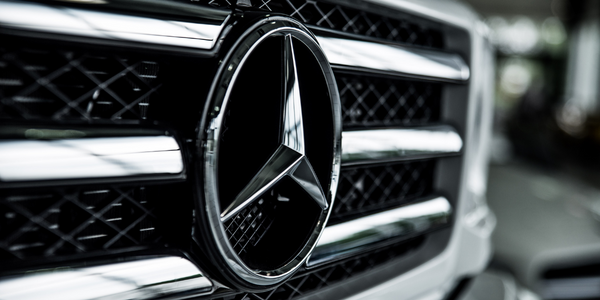
Case Study
Integral Plant Maintenance
Mercedes-Benz and his partner GAZ chose Siemens to be its maintenance partner at a new engine plant in Yaroslavl, Russia. The new plant offers a capacity to manufacture diesel engines for the Russian market, for locally produced Sprinter Classic. In addition to engines for the local market, the Yaroslavl plant will also produce spare parts. Mercedes-Benz Russia and his partner needed a service partner in order to ensure the operation of these lines in a maintenance partnership arrangement. The challenges included coordinating the entire maintenance management operation, in particular inspections, corrective and predictive maintenance activities, and the optimizing spare parts management. Siemens developed a customized maintenance solution that includes all electronic and mechanical maintenance activities (Integral Plant Maintenance).
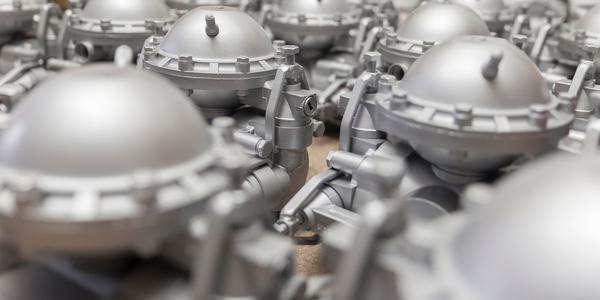
Case Study
Monitoring of Pressure Pumps in Automotive Industry
A large German/American producer of auto parts uses high-pressure pumps to deburr machined parts as a part of its production and quality check process. They decided to monitor these pumps to make sure they work properly and that they can see any indications leading to a potential failure before it affects their process.