Comau increases operational efficiency and reduces risk of failure by 60% with SoftExpert
Customer Company Size
Large Corporate
Region
- Europe
- America
Country
- Italy
- Brazil
Product
- SoftExpert Excellence Suite
Tech Stack
- Web-based Application
Implementation Scale
- Enterprise-wide Deployment
Impact Metrics
- Productivity Improvements
- Cost Savings
- Customer Satisfaction
Technology Category
- Functional Applications - Enterprise Resource Planning Systems (ERP)
- Functional Applications - Enterprise Asset Management Systems (EAM)
Applicable Industries
- Automotive
Applicable Functions
- Business Operation
- Quality Assurance
Use Cases
- Process Control & Optimization
- Predictive Maintenance
- Regulatory Compliance Monitoring
Services
- System Integration
- Training
About The Customer
Comau is an Italian multinational that is part of the FCA group, one of the world's largest players in the automotive sector, which includes brands such as Fiat, Jeep, Alfa Romeo, Chrysler, Dodge, Maserati and others. A world leader in the supply of advanced industrial automation products and solutions, it has a portfolio of industrial and collaborative robots, autonomous logistics, wearable technology, automated systems for production lines, digital and interconnected solutions, machining centers, specialized industrial maintenance services and facilities. The company has been in the market for 45 years, operating in 14 countries, with 32 branches, 5 innovation centers, 14 operating plants and over 9 thousand collaborators.
The Challenge
Comau sought to monitor processes and contracts at all stages through a structured and automated method. Business unit management, processes and performance information were performed in spreadsheets and communication was done over e-mail. The compilation of information, analysis and results on the performance of services took, on average, 7 days to be generated. The more than 50 contracts implemented in 12 Brazilian states, generated information using 25 tools/sheets per location, in a total of 500 documents per month.
The Solution
Softexpert Excellence Suite was made available to 220 users from various areas, with different levels of security and management. Through the tool, it is possible to access dynamic portals, where there is relevant information for each level, and can even be connected through smartphones. The project included the implementation of these components: Audit, Process, Incident, Form, Problem, Performance, Document, Risk, Survey and Action Plan.
Operational Impact
Quantitative Benefit
Case Study missing?
Start adding your own!
Register with your work email and create a new case study profile for your business.
Related Case Studies.
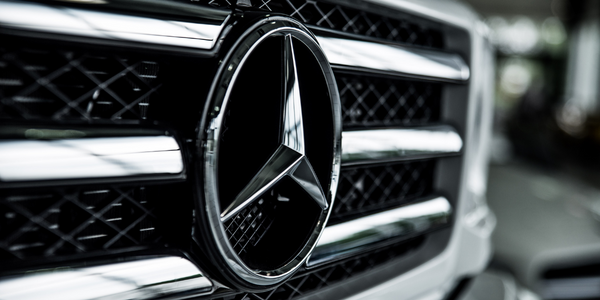
Case Study
Integral Plant Maintenance
Mercedes-Benz and his partner GAZ chose Siemens to be its maintenance partner at a new engine plant in Yaroslavl, Russia. The new plant offers a capacity to manufacture diesel engines for the Russian market, for locally produced Sprinter Classic. In addition to engines for the local market, the Yaroslavl plant will also produce spare parts. Mercedes-Benz Russia and his partner needed a service partner in order to ensure the operation of these lines in a maintenance partnership arrangement. The challenges included coordinating the entire maintenance management operation, in particular inspections, corrective and predictive maintenance activities, and the optimizing spare parts management. Siemens developed a customized maintenance solution that includes all electronic and mechanical maintenance activities (Integral Plant Maintenance).
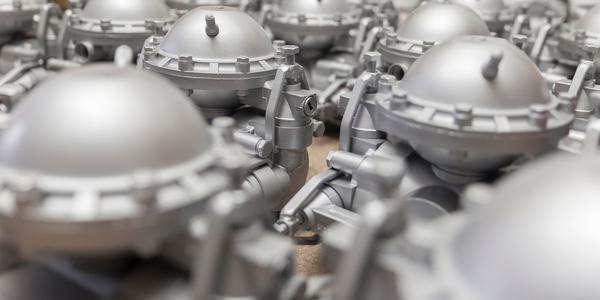
Case Study
Monitoring of Pressure Pumps in Automotive Industry
A large German/American producer of auto parts uses high-pressure pumps to deburr machined parts as a part of its production and quality check process. They decided to monitor these pumps to make sure they work properly and that they can see any indications leading to a potential failure before it affects their process.