Better Together
Customer Company Size
Large Corporate
Region
- Africa
- America
- Asia
- Europe
Country
- Brazil
- Canada
- China
- Hungary
- Korea
- Mexico
- United Kingdom
- United States
Product
- Workday Core HCM
- Workday Absence
- Workday Benefits
- Workday Compensation
- Workday Payroll
Tech Stack
- SaaS
Implementation Scale
- Enterprise-wide Deployment
Impact Metrics
- Cost Savings
- Digital Expertise
- Productivity Improvements
Technology Category
- Platform as a Service (PaaS) - Application Development Platforms
Applicable Industries
- Automotive
Applicable Functions
- Business Operation
- Human Resources
Services
- System Integration
- Training
About The Customer
Remy International traces its roots to 1896, when brothers Frank and Perry Remy developed the Remy Magneto to power the first vehicles. Today, Remy is the leading global manufacturer and remanufacturer of automotive parts such as starters, alternators, and hybrid motors. They are based in Indiana and have global operations across four continents and 11 countries. 'We Start the World & Keep It Running™' is not just a tagline but a company goal – long-standing partnerships allow Remy to stay ahead of customer needs and develop more innovative products and services within the automotive industry.
The Challenge
Remy International needed a solution to unify internal HR processes and create a common repository for global employee data. The country-specific HR solutions yielded fragmented and incomplete information. Initially, PeopleSoft was chosen as the solution to meet these needs. Budget constraints and the need for too many customizations made a global implementation of PeopleSoft virtually impossible. After several attempts to implement PeopleSoft successfully, Remy looked elsewhere for a more innovative solution to unify the worker population.
The Solution
In Workday’s SaaS model, Remy found the configuration methods to be better suited to its dynamic global needs. We worked with Remy’s team to deploy various Workday functionalities in multiple phases including Workday Core HCM, Absence, Benefits, Compensation, Payroll, Performance, and Integration Development. The initial implementation phase included the US, Mexico, Canada, Brazil, and Hungary. Subsequent phased implementations included Tunisia, UK, Korea, and China.
Operational Impact
Quantitative Benefit
Case Study missing?
Start adding your own!
Register with your work email and create a new case study profile for your business.
Related Case Studies.
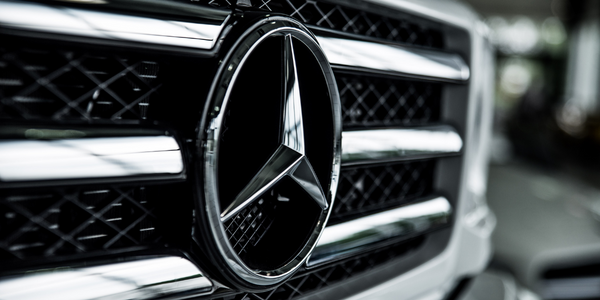
Case Study
Integral Plant Maintenance
Mercedes-Benz and his partner GAZ chose Siemens to be its maintenance partner at a new engine plant in Yaroslavl, Russia. The new plant offers a capacity to manufacture diesel engines for the Russian market, for locally produced Sprinter Classic. In addition to engines for the local market, the Yaroslavl plant will also produce spare parts. Mercedes-Benz Russia and his partner needed a service partner in order to ensure the operation of these lines in a maintenance partnership arrangement. The challenges included coordinating the entire maintenance management operation, in particular inspections, corrective and predictive maintenance activities, and the optimizing spare parts management. Siemens developed a customized maintenance solution that includes all electronic and mechanical maintenance activities (Integral Plant Maintenance).
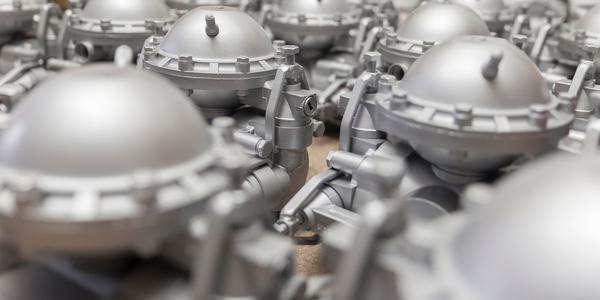
Case Study
Monitoring of Pressure Pumps in Automotive Industry
A large German/American producer of auto parts uses high-pressure pumps to deburr machined parts as a part of its production and quality check process. They decided to monitor these pumps to make sure they work properly and that they can see any indications leading to a potential failure before it affects their process.