Technology Category
- Application Infrastructure & Middleware - Event-Driven Application
Applicable Industries
- Cement
- Transportation
Applicable Functions
- Logistics & Transportation
- Procurement
Use Cases
- Last Mile Delivery
Services
- System Integration
About The Customer
Céu Delivery's primary customers are business owners in Brazil who require delivery services. These businesses may range from small startups to larger companies, all of whom are looking for a cost-effective and efficient way to manage their delivery services. The businesses may be in various sectors, including food, retail, and more. They are likely to be businesses that are growing and finding the manual management of delivery services increasingly labor-intensive and stressful. They are also likely to be businesses that are financially strained by the high fees charged by marketplaces for delivery services.
The Challenge
Céu Delivery, a Brazilian company, was founded by Juliano Rodrigues to address the challenges faced by businesses requiring delivery services in the country. The existing options were either to offer telephone service or to participate in a marketplace that charged high fees, significantly reducing business profits. While the telephone service option seemed viable, it became increasingly labor-intensive and stressful as the business grew. The marketplace option, on the other hand, was financially draining due to the exorbitant fees charged. Rodrigues recognized the need for an automated solution that could bridge the gap between delivery service owners and customers, thereby reducing operating costs and increasing business sales and profits.
The Solution
Rodrigues developed Céu Delivery, an automated delivery service management tool, using Bubble's no-code programming tools. The app allows businesses to have their professional delivery app without paying fees to marketplaces. Companies can subscribe to the service, register their company data, operating hours, products, delivery personnel, and discount coupons. The app link can then be shared with customers or through social media networks. The app enables users to control the entire workflow, from receiving the order to the delivery of the order. Rodrigues, who is not a programmer, was able to create this solution thanks to the no-code tools provided by Bubble, which he learned about through Renato Asse's YouTube channel.
Operational Impact
Quantitative Benefit
Case Study missing?
Start adding your own!
Register with your work email and create a new case study profile for your business.
Related Case Studies.

Case Study
System 800xA at Indian Cement Plants
Chettinad Cement recognized that further efficiencies could be achieved in its cement manufacturing process. It looked to investing in comprehensive operational and control technologies to manage and derive productivity and energy efficiency gains from the assets on Line 2, their second plant in India.
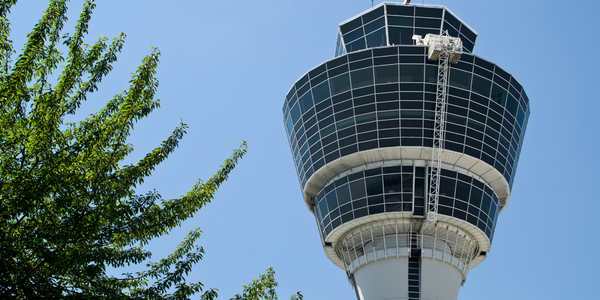
Case Study
Airport SCADA Systems Improve Service Levels
Modern airports are one of the busiest environments on Earth and rely on process automation equipment to ensure service operators achieve their KPIs. Increasingly airport SCADA systems are being used to control all aspects of the operation and associated facilities. This is because unplanned system downtime can cost dearly, both in terms of reduced revenues and the associated loss of customer satisfaction due to inevitable travel inconvenience and disruption.
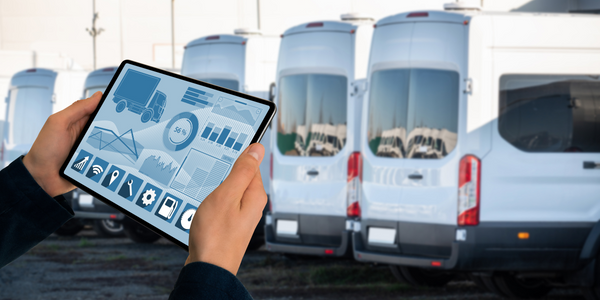
Case Study
IoT-based Fleet Intelligence Innovation
Speed to market is precious for DRVR, a rapidly growing start-up company. With a business model dependent on reliable mobile data, managers were spending their lives trying to negotiate data roaming deals with mobile network operators in different countries. And, even then, service quality was a constant concern.
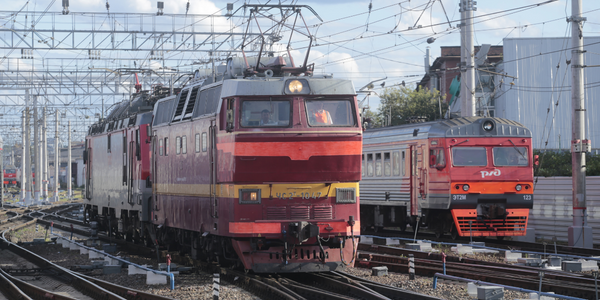
Case Study
Digitize Railway with Deutsche Bahn
To reduce maintenance costs and delay-causing failures for Deutsche Bahn. They need manual measurements by a position measurement system based on custom-made MEMS sensor clusters, which allow autonomous and continuous monitoring with wireless data transmission and long battery. They were looking for data pre-processing solution in the sensor and machine learning algorithms in the cloud so as to detect critical wear.
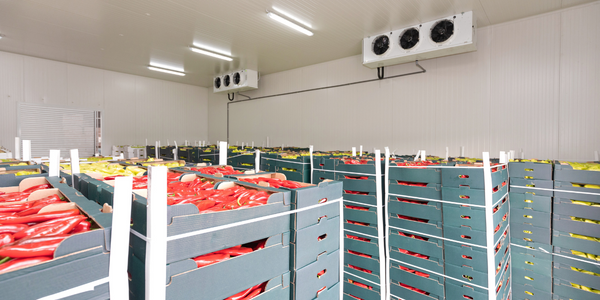
Case Study
Cold Chain Transportation and Refrigerated Fleet Management System
1) Create a digital connected transportation solution to retrofit cold chain trailers with real-time tracking and controls. 2) Prevent multi-million dollar losses due to theft or spoilage. 3) Deliver a digital chain-of-custody solution for door to door load monitoring and security. 4) Provide a trusted multi-fleet solution in a single application with granular data and access controls.
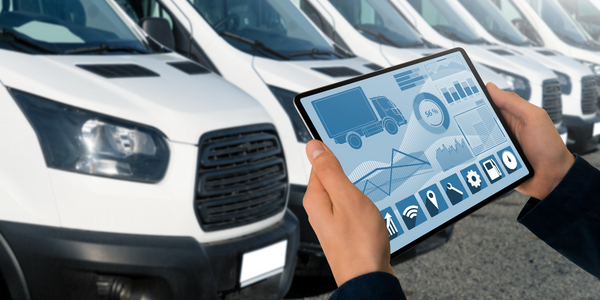
Case Study
Vehicle Fleet Analytics
Organizations frequently implement a maintenance strategy for their fleets of vehicles using a combination of time and usage based maintenance schedules. While effective as a whole, time and usage based schedules do not take into account driving patterns, environmental factors, and sensors currently deployed within the vehicle measuring crank voltage, ignition voltage, and acceleration, all of which have a significant influence on the overall health of the vehicle.In a typical fleet, a large percentage of road calls are related to electrical failure, with battery failure being a common cause. Battery failures result in unmet service agreement levels and costly re-adjustment of scheduled to provide replacement vehicles. To reduce the impact of unplanned maintenance, the transportation logistics company was interested in a trial of C3 Vehicle Fleet Analytics.