Technology Category
- Analytics & Modeling - Real Time Analytics
- Functional Applications - Inventory Management Systems
Applicable Industries
- Automotive
- Transportation
Applicable Functions
- Logistics & Transportation
- Warehouse & Inventory Management
Use Cases
- Inventory Management
- Picking, Sorting & Positioning
Services
- System Integration
- Testing & Certification
About The Customer
Fujitsu is an integrated supplier to the automotive industry in North America and one of the world’s leading developers and producers of innovative audio, digital, and other electronic products for consumer, business, and industrial use. The company is headquartered in the United States with five additional primary worldwide locations. The company has some 600 users regularly using glovia.com. Fujitsu began their upgrade in January of 2005 and went live the following November. Throughout the migration process, CrescentOne worked with the company to help keep them on track and make the migration a success.
The Challenge
Fujitsu, an integrated supplier to the automotive industry, was operating on an outdated version of glovia.com. The company had numerous decentralized applications which were difficult to monitor and coordinate. The system had over 3,000 customizations, making it cumbersome to navigate and lacked the ability to provide important information in real-time. The company was also struggling with a large number of decentralized systems, which complicated company-wide processes. The need to manually input customizations into multiple systems was a time-consuming process necessary for the decentralized systems to communicate with each other. The company also lacked full network monitoring and real-time operational measurements.
The Solution
Fujitsu selected glovia.com as their single enterprise solution and migrated to the current version in 2005, replacing legacy systems at locations not utilizing glovia.com. The current version automated many of their critical business processes, improved navigation of the system, and provided important operational information in real-time. The company standardized onto a single enterprise solution to simplify company-wide processes and replace legacy systems. This provided a top-down view of their global operations, helped streamline operations, automate manual processes, and reduce the total cost of ownership. The migration also eliminated the vast majority of customizations, reducing them to less than 100. The new system also improved business application monitoring, automated many processes, and enabled real-time operational measurements. Web access was provided across all locations for order-entry, service, quotes, and queries, increasing the speed and effectiveness of operations.
Operational Impact
Quantitative Benefit
Case Study missing?
Start adding your own!
Register with your work email and create a new case study profile for your business.
Related Case Studies.
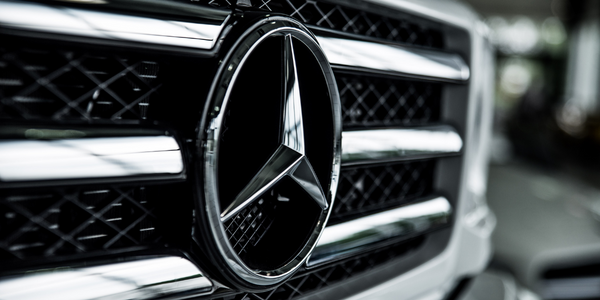
Case Study
Integral Plant Maintenance
Mercedes-Benz and his partner GAZ chose Siemens to be its maintenance partner at a new engine plant in Yaroslavl, Russia. The new plant offers a capacity to manufacture diesel engines for the Russian market, for locally produced Sprinter Classic. In addition to engines for the local market, the Yaroslavl plant will also produce spare parts. Mercedes-Benz Russia and his partner needed a service partner in order to ensure the operation of these lines in a maintenance partnership arrangement. The challenges included coordinating the entire maintenance management operation, in particular inspections, corrective and predictive maintenance activities, and the optimizing spare parts management. Siemens developed a customized maintenance solution that includes all electronic and mechanical maintenance activities (Integral Plant Maintenance).
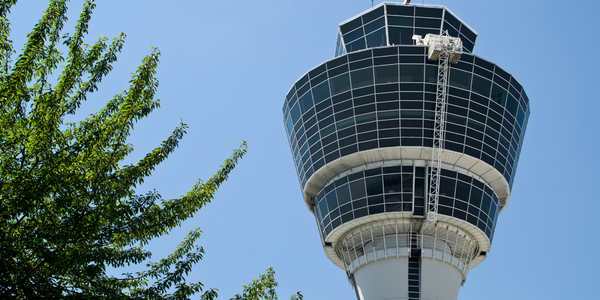
Case Study
Airport SCADA Systems Improve Service Levels
Modern airports are one of the busiest environments on Earth and rely on process automation equipment to ensure service operators achieve their KPIs. Increasingly airport SCADA systems are being used to control all aspects of the operation and associated facilities. This is because unplanned system downtime can cost dearly, both in terms of reduced revenues and the associated loss of customer satisfaction due to inevitable travel inconvenience and disruption.
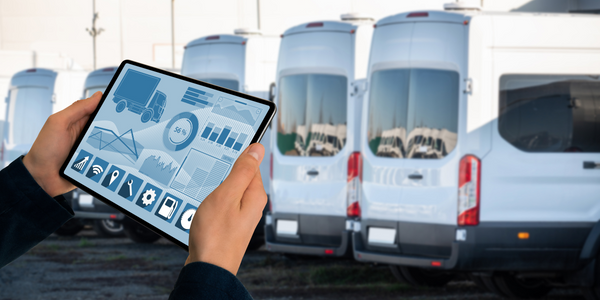
Case Study
IoT-based Fleet Intelligence Innovation
Speed to market is precious for DRVR, a rapidly growing start-up company. With a business model dependent on reliable mobile data, managers were spending their lives trying to negotiate data roaming deals with mobile network operators in different countries. And, even then, service quality was a constant concern.
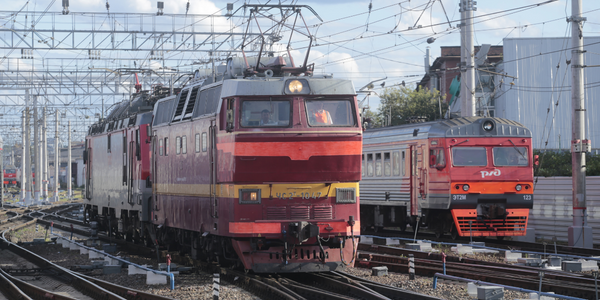
Case Study
Digitize Railway with Deutsche Bahn
To reduce maintenance costs and delay-causing failures for Deutsche Bahn. They need manual measurements by a position measurement system based on custom-made MEMS sensor clusters, which allow autonomous and continuous monitoring with wireless data transmission and long battery. They were looking for data pre-processing solution in the sensor and machine learning algorithms in the cloud so as to detect critical wear.