Technology Category
- Sensors - Liquid Detection Sensors
- Sensors - Temperature Sensors
Applicable Industries
- Aerospace
- Life Sciences
Applicable Functions
- Product Research & Development
Use Cases
- Behavior & Emotion Tracking
- Experimentation Automation
About The Customer
Astec, Inc. is a member of the Astec Industries family of companies, located in Chattanooga, Tennessee. The company is a manufacturer of continuous and batch-process hot-mix asphalt plants and related equipment and services. Astec is committed to improving its products and services by leveraging technology and innovation. The company has integrated EDEM into its design process, recognizing it as a valuable tool for its engineers. Astec's commitment to energy efficiency and process optimization led to the challenge of redesigning their drum dryer for better performance and reduced energy consumption.
The Challenge
Astec, Inc., a manufacturer of continuous and batch-process hot-mix asphalt plants, was faced with the challenge of developing a more energy-efficient drum dryer that could process a wide range of aggregate types at various tonnage rates. The drying process in asphalt production is energy-intensive, requiring hundreds of tons per hour of wet aggregate rock to be dried in a rotating drum dryer before being coated with liquid asphalt. This process ensures that the asphalt will bind to the rock. Inside the drum, the aggregate is kept in motion by shaped scoops called flights attached to the inner surface, which produce a 'veil' of falling material. Better veiling action improves heat transfer and speeds drying, reducing fuel consumption. However, direct observation of the drum in operation is very difficult, making it challenging to experiment with new flight designs.
The Solution
Astec deployed EDEM, a Discrete Element Method (DEM) software, to provide a virtual environment for observing and analyzing the effect of flight design and operating parameters on material flow. Astec imported CAD files of the drum dryer into EDEM and generated an aggregate rock DEM Material Model. After model calibration, EDEM accurately simulated the dynamics of the rocks being lifted and released by the flighting. Using EDEM’s binning function to calculate the number of rocks in a given volume, Astec could quantify the density of the veiled aggregate in a given drum section. By virtually comparing the performance of different flight designs, Astec was able to arrive at a new flight design, called the 'V Flight,' which optimized the distribution of rock during veiling, improving the aggregate drying process.
Operational Impact
Quantitative Benefit
Case Study missing?
Start adding your own!
Register with your work email and create a new case study profile for your business.
Related Case Studies.
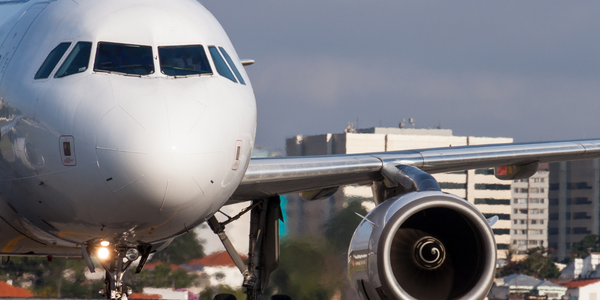
Case Study
Airbus Soars with Wearable Technology
Building an Airbus aircraft involves complex manufacturing processes consisting of thousands of moving parts. Speed and accuracy are critical to business and competitive advantage. Improvements in both would have high impact on Airbus’ bottom line. Airbus wanted to help operators reduce the complexity of assembling cabin seats and decrease the time required to complete this task.
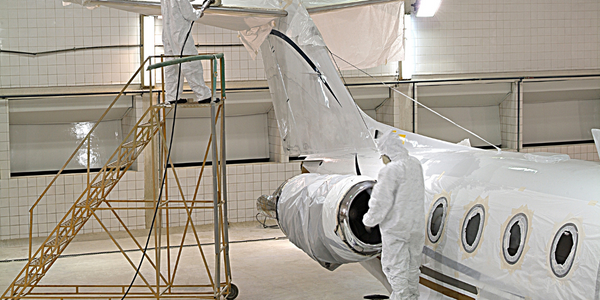
Case Study
Aircraft Predictive Maintenance and Workflow Optimization
First, aircraft manufacturer have trouble monitoring the health of aircraft systems with health prognostics and deliver predictive maintenance insights. Second, aircraft manufacturer wants a solution that can provide an in-context advisory and align job assignments to match technician experience and expertise.
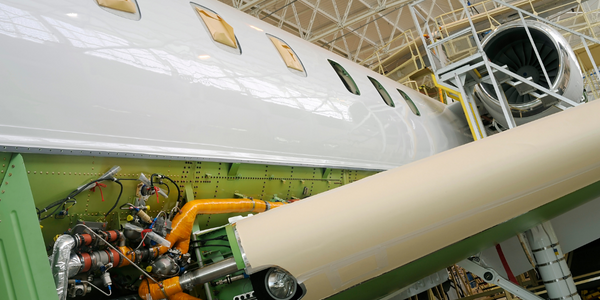
Case Study
Aerospace & Defense Case Study Airbus
For the development of its new wide-body aircraft, Airbus needed to ensure quality and consistency across all internal and external stakeholders. Airbus had many challenges including a very aggressive development schedule and the need to ramp up production quickly to satisfy their delivery commitments. The lack of communication extended design time and introduced errors that drove up costs.
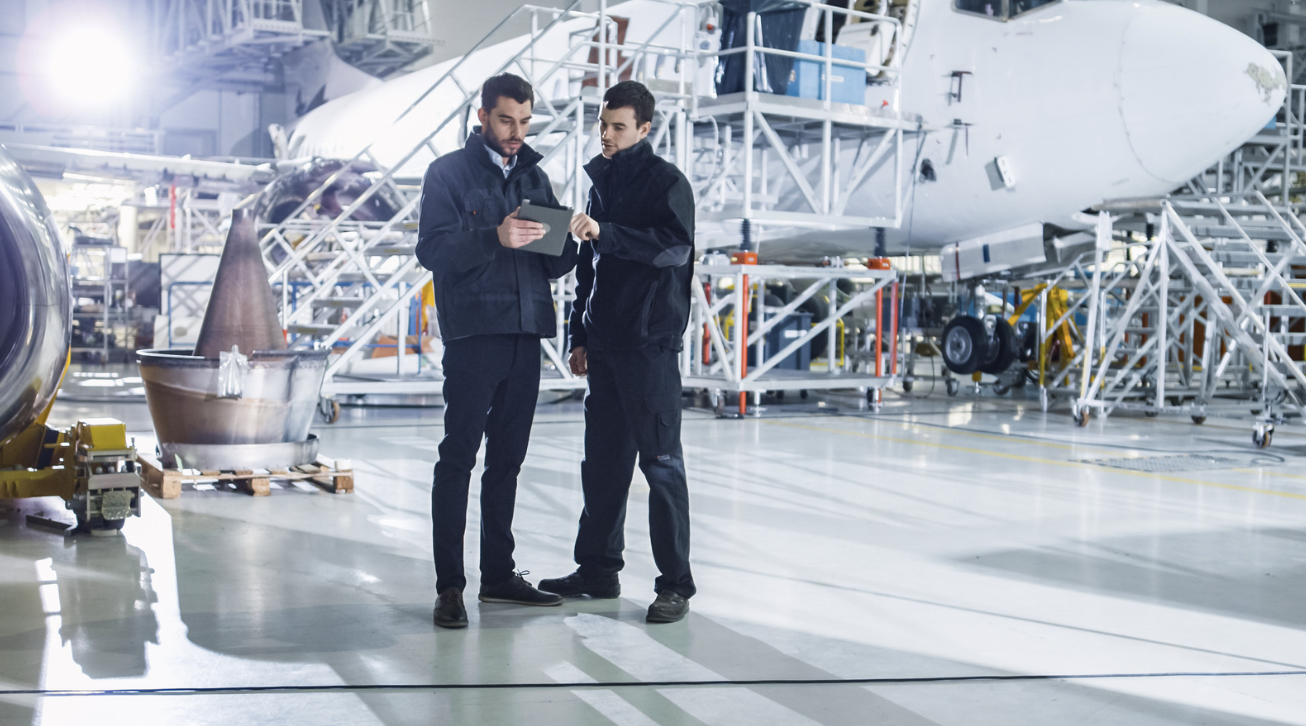
Case Study
Developing Smart Tools for the Airbus Factory
Manufacturing and assembly of aircraft, which involves tens of thousands of steps that must be followed by the operators, and a single mistake in the process could cost hundreds of thousands of dollars to fix, makes the room for error very small.
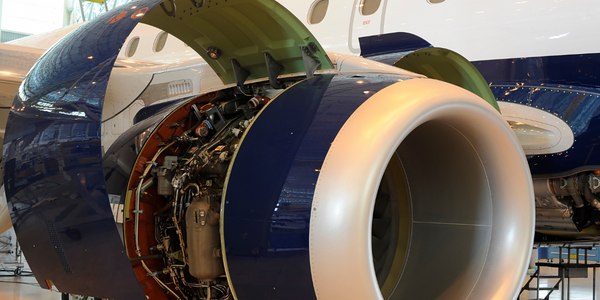
Case Study
Accelerate Production for Spirit AeroSystems
The manufacture and assembly of massive fuselage assemblies and other large structures generates a river of data. In fact, the bill of materials for a single fuselage alone can be millions of rows of data. In-house production processes and testing, as well as other manufacturers and customers created data flows that overwhelmed previous processes and information systems. Spirit’s customer base had grown substantially since their 2005 divestiture from Boeing, resulting in a $41 billion backlog of orders to fill. To address this backlog, meet increased customer demands and minimize additional capital investment, the company needed a way to improve throughput in the existing operational footprint. Spirit had a requirement from customers to increase fuselage production by 30%. To accomplish this goal, Spirit needed real-time information on its value chain and workflow. However, the two terabytes of data being pulled from their SAP ECC was unmanageable and overloaded their business warehouse. It had become time-consuming and difficult to pull aggregate data, disaggregate it for the needed information and then reassemble to create a report. During the 6-8 hours it took to build a report, another work shift (they run three per day) would have already taken place, thus the report content was out-of-date before it was ever delivered. As a result, supervisors often had to rely on manual efforts to provide charts, reports and analysis.