Alstom Uses aPriori to Model Supplier Costs for 100,000+ Parts While Implementing Zero-RFQ
Company Size
1,000+
Region
- Africa
- America
- Asia
- Europe
Country
- France
- India
- South Africa
- United States
Product
- aPriori
Tech Stack
- Digital Manufacturing Simulation
- 3D CAD
- PLM System
Implementation Scale
- Enterprise-wide Deployment
Impact Metrics
- Cost Savings
- Customer Satisfaction
- Productivity Improvements
Technology Category
- Analytics & Modeling - Digital Twin / Simulation
- Application Infrastructure & Middleware - Data Exchange & Integration
- Functional Applications - Product Lifecycle Management Systems (PLM)
Applicable Industries
- Railway & Metro
- Transportation
Applicable Functions
- Procurement
- Product Research & Development
Use Cases
- Digital Twin
- Manufacturing System Automation
- Predictive Maintenance
- Supply Chain Visibility
Services
- Software Design & Engineering Services
- System Integration
About The Customer
Alstom is a global leader in the transportation sector, particularly in the manufacturing of rolling stock, which includes trains and rail systems. The company operates in over 60 countries and employs more than 75,000 people. Alstom’s Rolling Stock Division is the largest within the company, responsible for designing and manufacturing a wide range of train cars and components. The Design to Cost department within this division is tasked with evaluating new projects and developing cost models to facilitate more effective supplier negotiations. The team works with different branches of the company spread across the entire globe, making it essential to have a robust and efficient system for managing supplier costs and sourcing components.
The Challenge
Within the Rolling Stock Division, Alstom’s Design to Cost department is tasked with evaluating new projects and developing cost models to facilitate more effective supplier negotiation. The team needed a tool to generate manufacturing cost models for a diverse variety of train car components. Each car requires thousands of distinct parts, and Alstom’s global operations offer many different car designs. The right tool needed to offer detailed manufacturing cost models for the shell of the rail car and everything inside. Often, Alstom needed to source simple components at the last minute, leading to a scramble to find savings and source the part without delaying product development. Every new RFQ introduced a risk for delay, as suppliers could take up to three weeks to return a quote. Rushed RFQ processes limited Alstom’s ability to wait for multiple quotes for maximized savings. The Design to Cost team faced the challenge of supporting an urgent timeline while ensuring the most cost-effective option possible.
The Solution
Alstom selected aPriori as a tool capable of modeling manufacturing costs for the huge variety of components that go into rolling stock products. aPriori quickly matured as a solution used across virtually all the products managed by the Rolling Stock Design to Cost team. Digital manufacturing simulation is an essential capability for a team charged with generating a high volume of manufacturing cost models across a number of sub-systems. The department uses aPriori for both simple parts and extremely complex assemblies like complete car body shells. Once a 3D CAD model for a part is uploaded into the PLM system, aPriori generates a digital twin of the design. Its production can then be modeled with aPriori’s digital factories, which have been configured to reflect the capabilities and cost structures of different suppliers. With the ability to generate supplier-specific manufacturing cost models directly from 3D CAD files, Alstom’s purchasing team is now able to award purchase orders to suppliers based on the aPriori output, avoiding the need for lengthy quoting and negotiating timelines.
Operational Impact
Quantitative Benefit
Case Study missing?
Start adding your own!
Register with your work email and create a new case study profile for your business.
Related Case Studies.
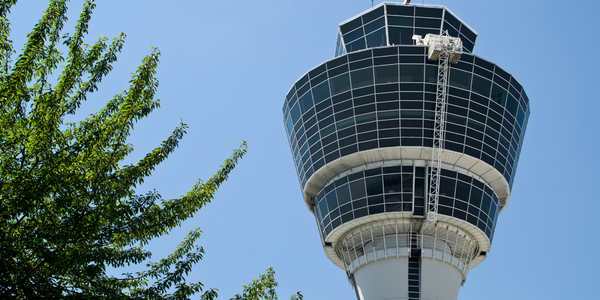
Case Study
Airport SCADA Systems Improve Service Levels
Modern airports are one of the busiest environments on Earth and rely on process automation equipment to ensure service operators achieve their KPIs. Increasingly airport SCADA systems are being used to control all aspects of the operation and associated facilities. This is because unplanned system downtime can cost dearly, both in terms of reduced revenues and the associated loss of customer satisfaction due to inevitable travel inconvenience and disruption.
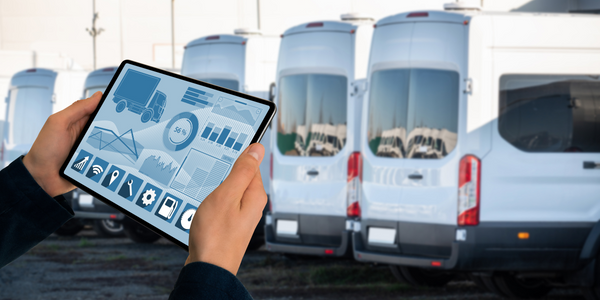
Case Study
IoT-based Fleet Intelligence Innovation
Speed to market is precious for DRVR, a rapidly growing start-up company. With a business model dependent on reliable mobile data, managers were spending their lives trying to negotiate data roaming deals with mobile network operators in different countries. And, even then, service quality was a constant concern.
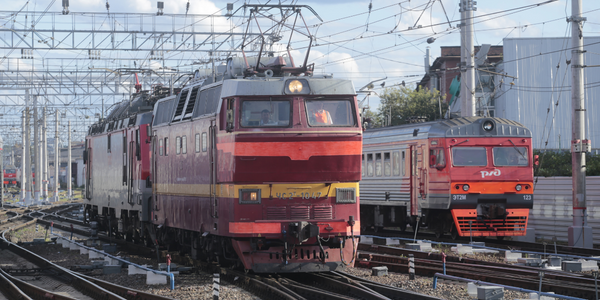
Case Study
Digitize Railway with Deutsche Bahn
To reduce maintenance costs and delay-causing failures for Deutsche Bahn. They need manual measurements by a position measurement system based on custom-made MEMS sensor clusters, which allow autonomous and continuous monitoring with wireless data transmission and long battery. They were looking for data pre-processing solution in the sensor and machine learning algorithms in the cloud so as to detect critical wear.
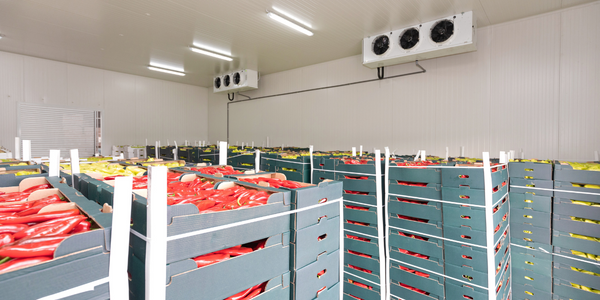
Case Study
Cold Chain Transportation and Refrigerated Fleet Management System
1) Create a digital connected transportation solution to retrofit cold chain trailers with real-time tracking and controls. 2) Prevent multi-million dollar losses due to theft or spoilage. 3) Deliver a digital chain-of-custody solution for door to door load monitoring and security. 4) Provide a trusted multi-fleet solution in a single application with granular data and access controls.
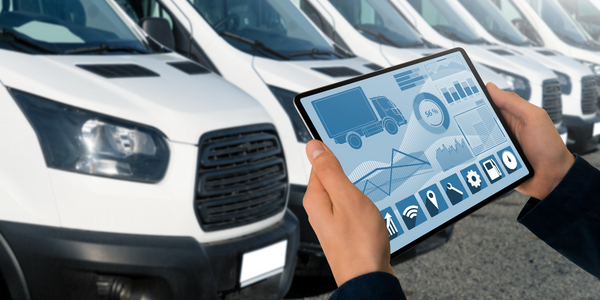
Case Study
Vehicle Fleet Analytics
Organizations frequently implement a maintenance strategy for their fleets of vehicles using a combination of time and usage based maintenance schedules. While effective as a whole, time and usage based schedules do not take into account driving patterns, environmental factors, and sensors currently deployed within the vehicle measuring crank voltage, ignition voltage, and acceleration, all of which have a significant influence on the overall health of the vehicle.In a typical fleet, a large percentage of road calls are related to electrical failure, with battery failure being a common cause. Battery failures result in unmet service agreement levels and costly re-adjustment of scheduled to provide replacement vehicles. To reduce the impact of unplanned maintenance, the transportation logistics company was interested in a trial of C3 Vehicle Fleet Analytics.
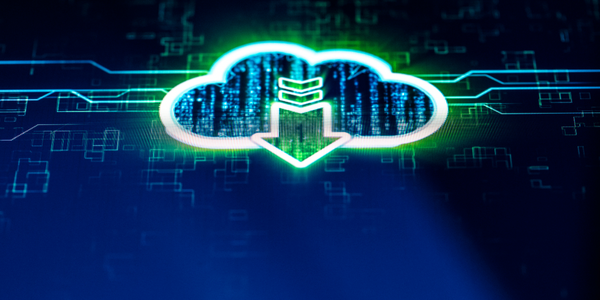
Case Study
3M Gains Real-Time Insight with Cloud Solution
The company has a long track record of innovative technology solutions. For example, 3M helps its customers optimize parking operations by automating fee collection and other processes. To improve support for this rapidly expanding segment, 3M needed to automate its own data collection and reporting. The company had recently purchased the assets of parking, tolling, and automatic license plate reader businesses, and required better insight into these acquisitions. Chad Reed, Global Business Manager for 3M Parking Systems, says, “With thousands of installations across the world, we couldn’t keep track of our software and hardware deployments, which made it difficult to understand our market penetration.” 3M wanted a tracking application that sales staff could use to get real-time information about the type and location of 3M products in parking lots and garages. So that it could be used on-site with potential customers, the solution would have to provide access to data anytime, anywhere, and from an array of mobile devices. Jason Fox, Mobile Application Architect at 3M, upped the ante by volunteering to deliver the new app in one weekend. For Fox and his team, these requirements meant turning to the cloud instead of an on-premises datacenter. “My first thought was to go directly to the cloud because we needed to provide access not only to our salespeople, but to resellers who didn’t have access to our internal network,” says Fox. “The cloud just seemed like a logical choice.”