Adapting jet engine technology for alternative energy uses with SolidWorks
Customer Company Size
SME
Region
- America
- Pacific
Country
- Canada
- United States
Product
- SolidWorks Premium
- SolidWorks Simulation Professional
- SolidWorks Flow Simulation
- SolidWorks Composer
- SolidWorks Workgroup PDM
Tech Stack
- 3D CAD
- CFD Analysis
- Product Data Management
- Simulation Software
Implementation Scale
- Enterprise-wide Deployment
Impact Metrics
- Productivity Improvements
- Innovation Output
- Customer Satisfaction
Technology Category
- Functional Applications - Product Lifecycle Management Systems (PLM)
- Analytics & Modeling - Predictive Analytics
- Application Infrastructure & Middleware - Data Visualization
Applicable Industries
- Renewable Energy
- Automotive
- Transportation
Applicable Functions
- Product Research & Development
- Quality Assurance
Use Cases
- Predictive Maintenance
- Energy Management System
- Fleet Management
- Remote Asset Management
Services
- Software Design & Engineering Services
- System Integration
- Training
About The Customer
Brayton Energy is a leading developer of innovative energy applications that combine abundant renewable fuels with gas turbine technology, which is traditionally used to power jet aircraft engines. The company has adapted this technology to create new hybrid engines, portable generators, and complete power plants. Brayton Energy's work spans the conversion of biomass and solar energy into electricity and the application of natural-gas-powered hybrid fuel cell/turbine engines for driving large vehicles. Established in 2004, Brayton Energy Canada is a subsidiary of Brayton Energy, LLC, and focuses on developing environmentally responsible energy technologies.
The Challenge
When Brayton Energy began developing environmentally responsible energy technologies in 2004, they needed a design platform that allowed engineers to design, analyze, and show innovative gas turbine applications within compressed development cycles. The company required a CAD system that could take them from concept to production in a streamlined, highly visual way. Given that they were breaking new ground for gas turbine technology, they needed to test and simulate the performance of their systems in software before investing in actual production. The CAD system had to be an extension of their operations, enabling quick movement without wasting time on retraining with various software applications from different vendors.
The Solution
Brayton Energy selected the SolidWorks Premium integrated 3D design system due to its ease of use, robust tools for designing large assemblies, automated sheet-metal design capabilities, and integrated simulation and documentation applications. They implemented 12 seats of SolidWorks software across their US and Canadian operations, including SolidWorks Simulation Professional, SolidWorks Flow Simulation, and SolidWorks Composer. This integrated platform allowed Brayton Energy to quickly develop and visualize innovative gas turbine systems, such as a unique hybrid solid oxide fuel cell (SOFC) system combined with a high-efficiency intercooled recuperated (ICR) gas turbine system for vehicular applications. The SolidWorks platform enabled the company to conduct structural, thermal, and fluid flow analysis, manage design files, and document the entire process efficiently.
Operational Impact
Quantitative Benefit
Case Study missing?
Start adding your own!
Register with your work email and create a new case study profile for your business.
Related Case Studies.

Case Study
Remote Monitoring & Predictive Maintenance App for a Solar Energy System
The maintenance & tracking of various modules was an overhead for the customer due to the huge labor costs involved. Being an advanced solar solutions provider, they wanted to ensure early detection of issues and provide the best-in-class customer experience. Hence they wanted to automate the whole process.
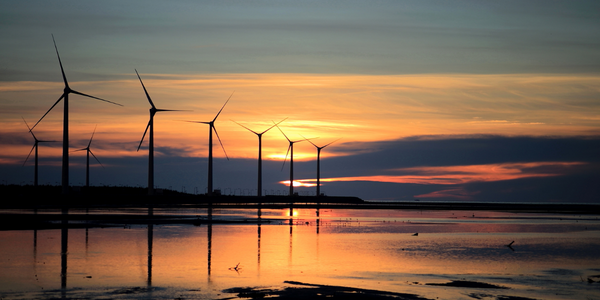
Case Study
Vestas: Turning Climate into Capital with Big Data
Making wind a reliable source of energy depends greatly on the placement of the wind turbines used to produce electricity. Turbulence is a significant factor as it strains turbine components, making them more likely to fail. Vestas wanted to pinpoint the optimal location for wind turbines to maximize power generation and reduce energy costs.
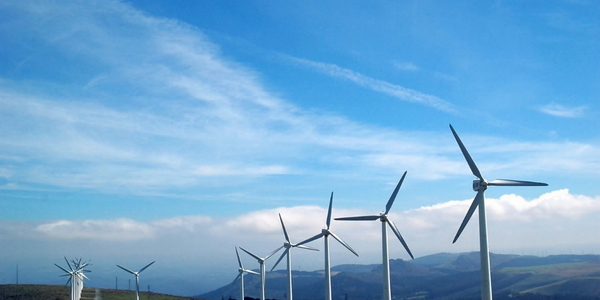
Case Study
Siemens Wind Power
Wind provides clean, renewable energy. The core concept is simple: wind turbines spin blades to generate power. However, today's systems are anything but simple. Modern wind turbines have blades that sweep a 120 meter circle, cost more than 1 million dollars and generate multiple megawatts of power. Each turbine may include up to 1,000 sensors and actuators – integrating strain gages, bearing monitors and power conditioning technology. The turbine can control blade speed and power generation by altering the blade pitch and power extraction. Controlling the turbine is a sophisticated job requiring many cooperating processors closing high-speed loops and implementing intelligent monitoring and optimization algorithms. But the real challenge is integrating these turbines so that they work together. A wind farm may include hundreds of turbines. They are often installed in difficult-to-access locations at sea. The farm must implement a fundamentally and truly distributed control system. Like all power systems, the goal of the farm is to match generation to load. A farm with hundreds of turbines must optimize that load by balancing the loading and generation across a wide geography. Wind, of course, is dynamic. Almost every picture of a wind farm shows a calm sea and a setting sun. But things get challenging when a storm goes through the wind farm. In a storm, the control system must decide how to take energy out of gusts to generate constant power. It must intelligently balance load across many turbines. And a critical consideration is the loading and potential damage to a half-billion-dollar installed asset. This is no environment for a slow or undependable control system. Reliability and performance are crucial.
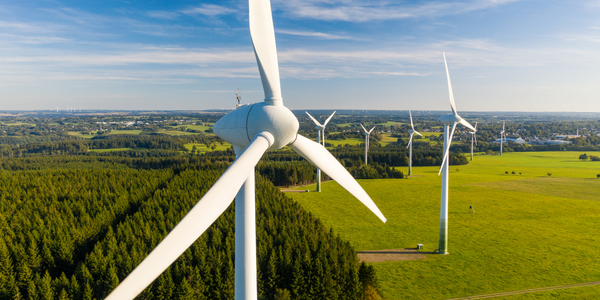
Case Study
Remote Monitoring and Control for a Windmill Generator
As concerns over global warming continue to grow, green technologies are becoming increasingly popular. Wind turbine companies provide an excellent alternative to burning fossil fuels by harnessing kinetic energy from the wind and converting it into electricity. A typical wind farm may include over 80 wind turbines so efficient and reliable networks to manage and control these installations are imperative. Each wind turbine includes a generator and a variety of serial components such as a water cooler, high voltage transformer, ultrasonic wind sensors, yaw gear, blade bearing, pitch cylinder, and hub controller. All of these components are controlled by a PLC and communicate with the ground host. Due to the total integration of these devices into an Ethernet network, one of our customers in the wind turbine industry needed a serial-to-Ethernet solution that can operate reliably for years without interruption.
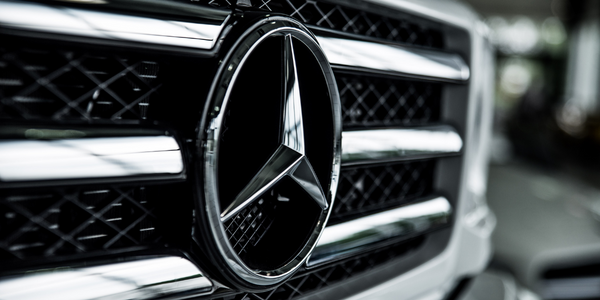
Case Study
Integral Plant Maintenance
Mercedes-Benz and his partner GAZ chose Siemens to be its maintenance partner at a new engine plant in Yaroslavl, Russia. The new plant offers a capacity to manufacture diesel engines for the Russian market, for locally produced Sprinter Classic. In addition to engines for the local market, the Yaroslavl plant will also produce spare parts. Mercedes-Benz Russia and his partner needed a service partner in order to ensure the operation of these lines in a maintenance partnership arrangement. The challenges included coordinating the entire maintenance management operation, in particular inspections, corrective and predictive maintenance activities, and the optimizing spare parts management. Siemens developed a customized maintenance solution that includes all electronic and mechanical maintenance activities (Integral Plant Maintenance).
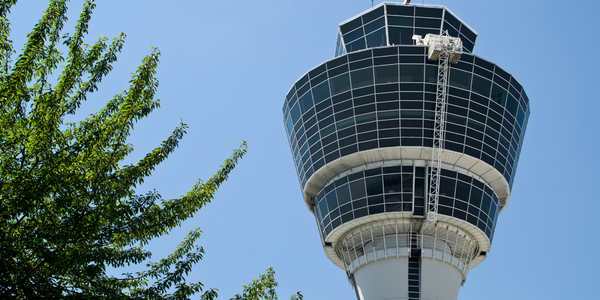
Case Study
Airport SCADA Systems Improve Service Levels
Modern airports are one of the busiest environments on Earth and rely on process automation equipment to ensure service operators achieve their KPIs. Increasingly airport SCADA systems are being used to control all aspects of the operation and associated facilities. This is because unplanned system downtime can cost dearly, both in terms of reduced revenues and the associated loss of customer satisfaction due to inevitable travel inconvenience and disruption.