过程控制与优化

概述
过程控制和优化 (PCO) 是在不违反过程约束的情况下调整过程以维持或优化一组指定参数的学科。 PCO 市场受到对节能生产流程、安全和安保问题的需求不断增长以及能够可靠预测流程偏差的物联网系统开发的推动。从根本上说,可以调整三个参数以影响最佳性能。 - 设备优化:第一步是通过检查运行数据以识别设备瓶颈来验证现有设备是否被充分利用。 - 操作程序:操作程序可能因人而异或因班次而异。工厂的自动化可以提供很大帮助。但是,如果操作员控制并手动运行工厂,自动化将无济于事。 - 控制优化:在典型的加工厂,例如化工厂或炼油厂,有数百甚至数千个控制回路。每个控制回路负责控制过程的一部分,例如保持温度、液位或流量。如果控制回路没有正确设计和调整,则过程会低于其最佳值。该过程的操作成本将更高,并且设备会过早磨损。为了使每个控制回路以最佳方式运行,识别传感器、阀门和调整问题很重要。已充分证明超过 35% 的控制回路通常存在问题。持续监控和优化整个工厂的过程有时称为绩效监督。
适用行业
- 运输
- 设备与机械
- 化学品
适用功能
- 离散制造
- 质量保证
市场规模
案例研究.
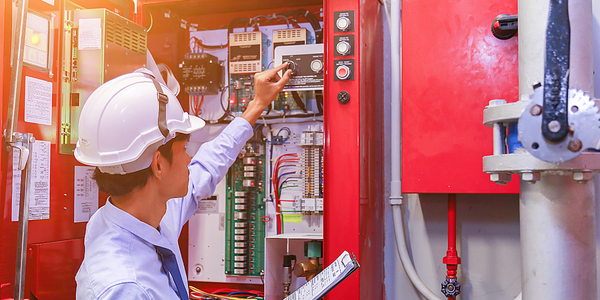
Case Study
versiondog on the Trial of Big Bang
Backing up and monitoring of Industrial control system programs for the Large Hadron Collider (LHC) at CERN near Geneva, the world´s largest particle accelerator, has been entrusted to the data management system versiondog. The European Organization for Nuclear Research uses the system to manage the data of around 500 components, making versiondog one of CERN's standard technologies.
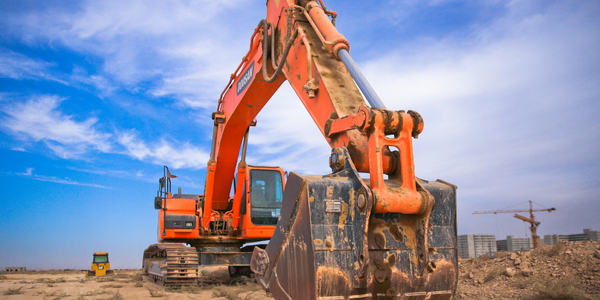
Case Study
Boost in Online Orders and Aftermarket Revenues for Atlas Copco
Printed parts manuals become less and less relevant and useful with time. The static information offered by printed documentation was no longer good enough for a major global player like ACC. ACC needed a solution that would deliver updated versions of documents to their network immediately. The company wanted a dynamic system, which would not only display current inventory levels, but also provide customers with information regarding how products should be used. Atlas Copco Construction’s Needs • Offer customers real-time part and information updates • Provide customers a comprehensive parts lookup and search platform • Administer an eCommerce platform with shopping cart and ERP integration • Produce a multilingual site for parts ordering
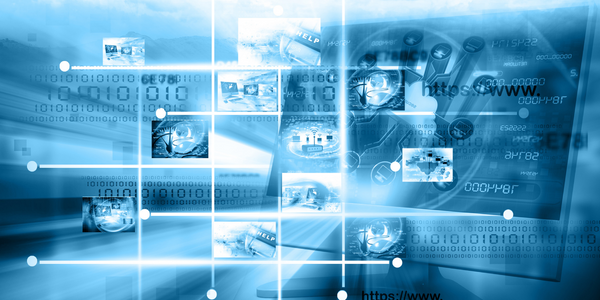
Case Study
Sensor Synergy Case Study
Whether sensors are stand-alone, connected to PLCs, interfaced to PCs or tied directly to networks, these devices can be found in a multitude of electronics that affect daily life – from washing machines to windshield wiper blades. Although there are a number of ways to add sensor data to a system, designers and users want to keep the sensor-to-system interface process as easy as possible, and, in many cases, users want this information to be accessible via the Internet.In recent years, the IEEE’s (Institute of Electrical and Electronics Engineering) approval of multiple standards, coupled with the increase of factory automation suppliers differentiating themselves by developing different communications protocols, has resulted in over 50 different hardware and software interface protocols. What initially was an opportunity for factory automation suppliers to provide enhanced new features to their customers has become a challenge for sensor manufacturers. It is increasingly difficult to develop sensor solutions that will interface with all applicable protocols. To help alleviate this problem, smart sensor technology pioneer, Sensor Synergy, developed a near-universal sensor-to-Internet solution utilizing Lantronix Device Networking technologies.