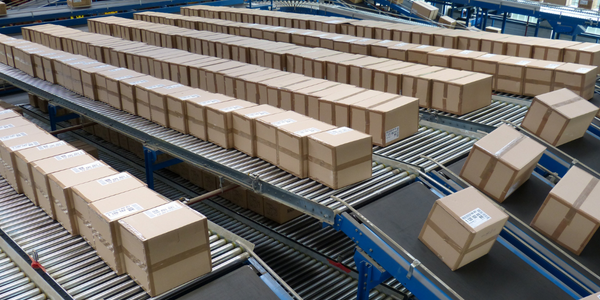
技术
- 自动化与控制 - 监督控制和数据采集 (SCADA)
适用行业
- 包装
适用功能
- 离散制造
用例
- 过程控制与优化
客户
KHS有限公司
关于客户
KHS GmbH 是一家位于德国多特蒙德的灌装和包装系统供应商,拥有 4,600 多名员工。该公司为饮料、食品和非食品行业提供玻璃和 PET 瓶、桶和罐的灌装线,是一家完全
挑战
KHS 开发和生产用于饮料行业灌装和包装的机器和设备。由于饮料制造、灌装和包装由许多高度复杂的过程组成,用户友好和直观的设备操作变得越来越重要。为了尽可能简单地为用户设计这些流程,KHS 决定为公司引入统一、透明和标准化的解决方案。 HMI 界面应满足不同资质人员的要求,使他们能够在标准平台上工作。
解决方案
KHS 决定使用 COPA-DATA 的 Zenon 来实施新的 ClearLine HMI。 Zenon HMI/SCADA 平台精确地提供了我们机器和生产线所需的东西。 zenon 软件具有完善的图形显示可能性和许多已作为标准配置的 HMI 元素。软件组件 - Zenon:COPA-DATA 的 HMI/SCADA 软件 - Everywhere App
收集的数据
Device Status, Machine Performance, Production Efficiency, Quantity Of Parts Produced
运营影响
Case Study missing?
Start adding your own!
Register with your work email and create a new case study profile for your business.
相关案例.
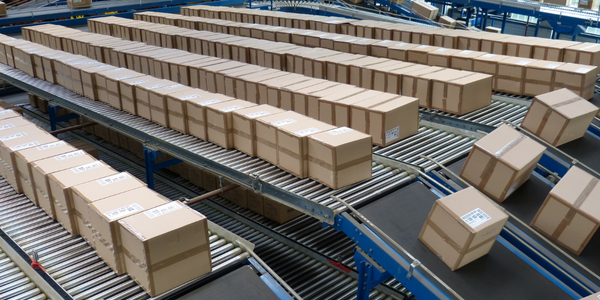
Case Study
IoT Data Analytics Case Study - Packaging Films Manufacturer
The company manufactures packaging films on made to order or configure to order basis. Every order has a different set of requirements from the product characteristics perspective and hence requires machine’s settings to be adjusted accordingly. If the film quality does not meet the required standards, the degraded quality impacts customer delivery causes customer dissatisfaction and results in lower margins. The biggest challenge was to identify the real root cause and devise a remedy for that.
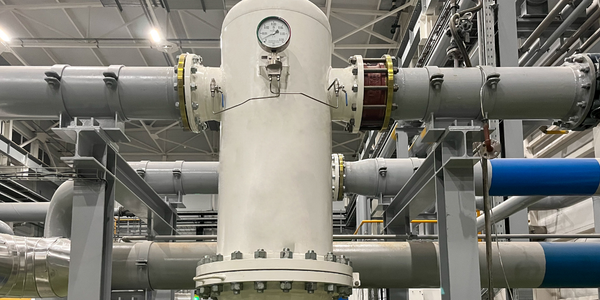
Case Study
Sparks Dynamics Assists Atlas Container Secure a $15,000 BGE Energy Rebate
The ReMASTER Compressed Air Monitoring system was installed in 2015. This system is capable of monitoring compressed air system parameters on a continuous basis and transferring that information to a cloud server which can be accessed by Atlas Container personnel, Industrial Diagnostics and Sparks Dynamics. This information was collected into a database which can be exported to an Excel spreadsheet or displayed graphically using Sparks Dynamics ViewMaster Software. The average annual compressed air electricity expense was estimated to be approximately $116,000. This is based on an incremental $/KWh electric rate of $.091 per KWh and an estimated compressed air energy consumption of 1,279,200 KWH. The implementation phase of Energy Conservation Measures (ECMs) for the Compressed Air System included: • Identification and repair of compressed air leaks • Understanding of compressed air usage per manufacturing machine and installation of shut off valves when the machines are no longer in production mode • Identification of misapplications of compressed air to include blow offs, venturis, and cooling scenarios • Understand system pressure requirements and potential installation of point of use pressure regulation.
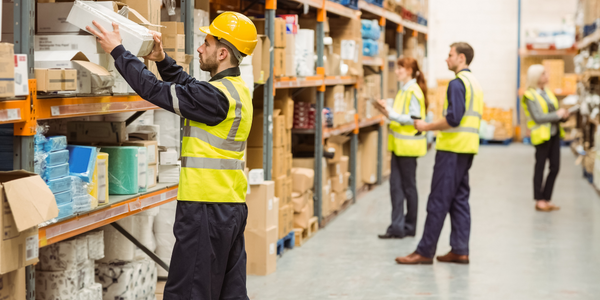
Case Study
Automated Pallet Labeling Solution for SPR Packaging
SPR Packaging, an American supplier of packaging solutions, was in search of an automated pallet labeling solution that could meet their immediate and future needs. They aimed to equip their lines with automatic printer applicators, but also required a solution that could interface with their accounting software. The challenge was to find a system that could read a 2D code on pallets at the stretch wrapper, track the pallet, and flag any pallets with unread barcodes for inspection. The pallets could be single or double stacked, and the system needed to be able to differentiate between the two. SPR Packaging sought a system integrator with extensive experience in advanced printing and tracking solutions to provide a complete traceability system.
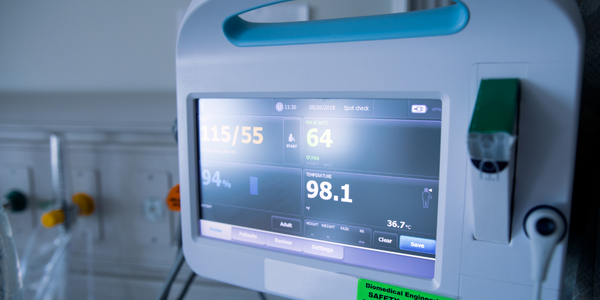
Case Study
Mondi Implements Statistics-Based Health Monitoring and Predictive Maintenance
The extrusion and other machines at Mondi’s plant are large and complex, measuring up to 50 meters long and 15 meters high. Each machine is controlled by up to five programmable logic controllers (PLCs), which log temperature, pressure, velocity, and other performance parameters from the machine’s sensors. Each machine records 300–400 parameter values every minute, generating 7 gigabytes of data daily.Mondi faced several challenges in using this data for predictive maintenance. First, the plant personnel had limited experience with statistical analysis and machine learning. They needed to evaluate a variety of machine learning approaches to identify which produced the most accurate results for their data. They also needed to develop an application that presented the results clearly and immediately to machine operators. Lastly, they needed to package this application for continuous use in a production environment.

Case Study
Industry 4.0 at ALPLA: Enhancing Factory Efficiency with IoT
ALPLA, a global leader in packaging solutions, faced several challenges as the complexity of their production machinery increased. The need for highly trained specialists in each factory led to higher personnel costs, difficulties in recruiting experienced talent at each location, and costly personnel turnover. Furthermore, less experienced operators running the machines sub-optimally impacted resource consumption and overall equipment effectiveness (OEE). ALPLA also faced the challenge of monitoring visual inspection systems in every line of their plants, which was almost impossible to do manually. In 2016, ALPLA decided to use data from the 900 different types of embedded sensors in each factory to address these issues. However, their initial choice of SQL Server as the data store for the sensor data proved inadequate, as it was unable to cope with their data requirements.

Case Study
Closer To Becoming world's Most Digitized Bottling Operation
While digitization is increasing efficiency and significantly growing customer engagement, it also comes with several challenges, not least being the growing risk of cyberattacks.This led the company’s Australian, Pacific and Indonesian operations (CCEP API) to create a three-year roadmap for developing and implementing enhanced security measures. A key element of the plan has been to improve existing privileged access management processes and gain heightened oversight and control over the use of elevated credentials.