World’s Leading Automotive Oem & Supplier Shrinks Freight Procurement Costs by 10% and Saves 75% in Personhours Spent
公司规模
Large Corporate
产品
- Shipsy International Logistics Management Platform
- Shipsy ERP Integrated Solution
- Shipsy Automated Documentation Management
技术栈
- ERP Integration
- Advanced Analytics
- Automated Tracking
实施规模
- Enterprise-wide Deployment
影响指标
- Cost Savings
- Productivity Improvements
- Customer Satisfaction
技术
- 功能应用 - 企业资源规划系统 (ERP)
- 分析与建模 - 预测分析
适用行业
- 汽车
- 运输
适用功能
- 物流运输
- 采购
用例
- 车队管理
- 预测性维护
- 供应链可见性(SCV)
- 仓库自动化
服务
- 系统集成
- 软件设计与工程服务
- 数据科学服务
关于客户
Our customer is one of the world’s largest manufacturers of components for the automotive and transport industries. With a global presence of 270 facilities in 41 countries, they focus on being a single-window, technology empowering 4PL solution provider for all their group companies with zero service failure assurance.
挑战
The customer was struggling with manual processes throughout the shipments’ lifecycle. They were challenged by poor freight negotiations with carriers and freight forwarders on lack of data-driven insights, and a centralized system to effectively manage multimodal shipments across all the group companies. The top 10 challenges specifically cited by our customer were: Multiple rounds of negotiations leading to error-prone freight procurement, Poor system interoperability and data inconsistencies, Siloed communications between key logistics stakeholders, Poor container visibility for order consolidation, Lack of transparency over market rates and cost deviations, Lack of analytics and monitoring for data-driven decisions, Disparate sources for multimodal shipment tracking, Lack of timely alerts and insights leading to cost leakages, Manual processes leading to higher turnaround times, Inefficient document and invoice management processes.
解决方案
The customer needed an intelligent solution that integrates with their current systems to drive unified visibility and automate shipment processes across companies. Shipsy’s automation-led and ERP integrated, end-to-end international logistics solution met their requirements out of the box. Key Solution Highlights: Enterprise-wide unified portals to create, float, compare, and confirm spots and freight rates, Single platform to collaborate and communicate with internal and external stakeholders for effective shipment execution, Standardized and automated documentation and invoice reconciliation, Automated, multimodal tracking of shipments, Insightful dashboards with advanced analytics and reporting. Shipsy’s International Logistics Management platform was a one-stop-shop solution for the customer to automate and optimize processes — from spot inquiries to advanced reporting — addressing all their shipment management needs. Our smart logistics management platform empowered the customer with: Up to 10% cost reduction in freight procurement, 75% person-hours saved in the overall procurement process, Instant access of rates leading to up to 2 days faster business closure process, A standardized process flow for shipment execution and documentation, bringing down the error rate by 70%, Up to 50% reduction in incidental costs, Up to 2 days faster BL release resulting in an improved working capital cycle, Faster, automation-led invoice reconciliation processes resulting in up to 80% person-hour savings.
运营影响
数量效益
Case Study missing?
Start adding your own!
Register with your work email and create a new case study profile for your business.
相关案例.
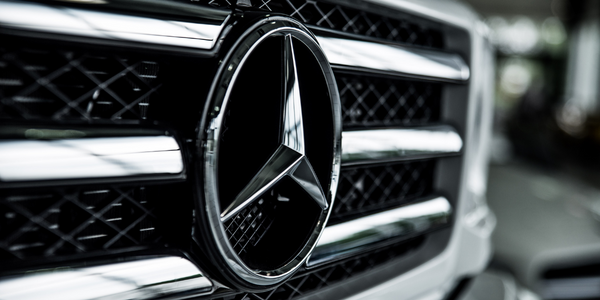
Case Study
Integral Plant Maintenance
Mercedes-Benz and his partner GAZ chose Siemens to be its maintenance partner at a new engine plant in Yaroslavl, Russia. The new plant offers a capacity to manufacture diesel engines for the Russian market, for locally produced Sprinter Classic. In addition to engines for the local market, the Yaroslavl plant will also produce spare parts. Mercedes-Benz Russia and his partner needed a service partner in order to ensure the operation of these lines in a maintenance partnership arrangement. The challenges included coordinating the entire maintenance management operation, in particular inspections, corrective and predictive maintenance activities, and the optimizing spare parts management. Siemens developed a customized maintenance solution that includes all electronic and mechanical maintenance activities (Integral Plant Maintenance).
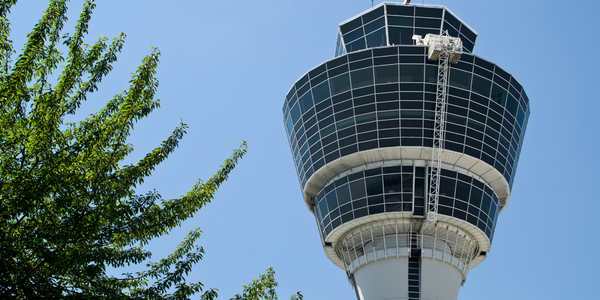
Case Study
Airport SCADA Systems Improve Service Levels
Modern airports are one of the busiest environments on Earth and rely on process automation equipment to ensure service operators achieve their KPIs. Increasingly airport SCADA systems are being used to control all aspects of the operation and associated facilities. This is because unplanned system downtime can cost dearly, both in terms of reduced revenues and the associated loss of customer satisfaction due to inevitable travel inconvenience and disruption.
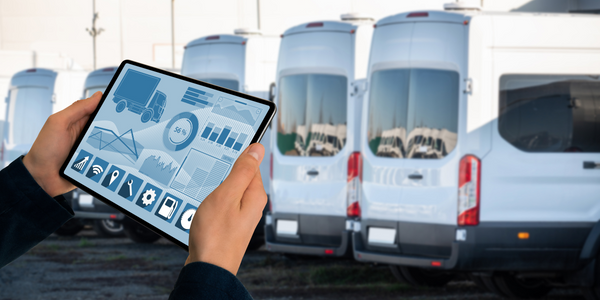
Case Study
IoT-based Fleet Intelligence Innovation
Speed to market is precious for DRVR, a rapidly growing start-up company. With a business model dependent on reliable mobile data, managers were spending their lives trying to negotiate data roaming deals with mobile network operators in different countries. And, even then, service quality was a constant concern.
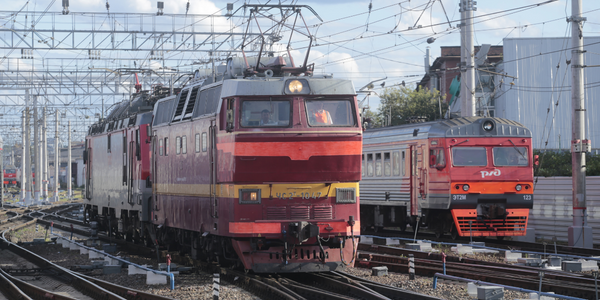
Case Study
Digitize Railway with Deutsche Bahn
To reduce maintenance costs and delay-causing failures for Deutsche Bahn. They need manual measurements by a position measurement system based on custom-made MEMS sensor clusters, which allow autonomous and continuous monitoring with wireless data transmission and long battery. They were looking for data pre-processing solution in the sensor and machine learning algorithms in the cloud so as to detect critical wear.