Walking on the World’s Most Advanced 3D Printed Prosthetics in the Jungles of Guatemala
公司规模
SME
地区
- America
国家
- Guatemala
产品
- nTopology
- MJF 3D Printing
技术栈
- 3D Scanning
- MJF 3D Printing
- nTopology Software
实施规模
- Enterprise-wide Deployment
影响指标
- Cost Savings
- Productivity Improvements
- Customer Satisfaction
技术
- 分析与建模 - Generative AI
- 功能应用 - 产品生命周期管理系统 (PLM)
- 功能应用 - 远程监控系统
适用行业
- 医疗保健和医院
适用功能
- 产品研发
- 质量保证
用例
- 添加剂制造
- 远程病人监护
- 预测性维护
服务
- 软件设计与工程服务
- 系统集成
- 培训
关于客户
LifeNabled is a non-profit organization dedicated to providing prosthetic solutions for the developing world. For the past 15 years, they have been changing the lives of amputees in northern Guatemala. Leveraging the 3D printing expertise of its founder, Brent Wright, LifeNabled has focused on creating a fully digital workflow to produce custom 3D printed prosthetic sockets with flexible inner liners. The organization aims to make the digital process scalable and cost-effective, with the potential to replicate it in other parts of the world to significantly improve the quality of life for amputees in developing countries.
挑战
LifeNabled, a non-profit organization, has been providing prosthetic solutions to amputees in northern Guatemala for the past 15 years. The traditional manufacturing process for prosthetics is expertise-intensive and laborious, making it difficult to scale and cost-effective. The organization aimed to digitize the entire workflow to bypass these challenges and make the process scalable and cost-effective. The goal was to improve the quality of life for amputees in developing countries by providing advanced prosthetic and orthotic devices.
解决方案
LifeNabled implemented a fully digital workflow for producing prosthetic devices. The process begins with 3D scanning of the patients, allowing for quick and accurate evaluations. The engineering team then designs each custom prosthetic device and manufactures the sockets using MJF 3D printing. The entire process, from 3D scan to manufacturing-ready STL files, is streamlined and semi-automated using nTopology's software. This approach not only saves valuable engineering time but also ensures higher-quality and error-free results. Additionally, the team opted for washable and low-cost cloth socks and flexible 3D printed foam liners to ensure comfort and hygiene for the patients.
运营影响
数量效益
Case Study missing?
Start adding your own!
Register with your work email and create a new case study profile for your business.
相关案例.
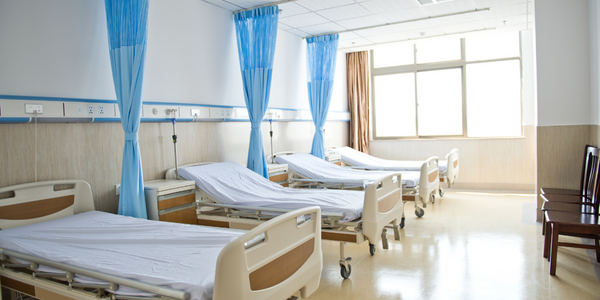
Case Study
Hospital Inventory Management
The hospital supply chain team is responsible for ensuring that the right medical supplies are readily available to clinicians when and where needed, and to do so in the most efficient manner possible. However, many of the systems and processes in use at the cancer center for supply chain management were not best suited to support these goals. Barcoding technology, a commonly used method for inventory management of medical supplies, is labor intensive, time consuming, does not provide real-time visibility into inventory levels and can be prone to error. Consequently, the lack of accurate and real-time visibility into inventory levels across multiple supply rooms in multiple hospital facilities creates additional inefficiency in the system causing over-ordering, hoarding, and wasted supplies. Other sources of waste and cost were also identified as candidates for improvement. Existing systems and processes did not provide adequate security for high-cost inventory within the hospital, which was another driver of cost. A lack of visibility into expiration dates for supplies resulted in supplies being wasted due to past expiry dates. Storage of supplies was also a key consideration given the location of the cancer center’s facilities in a dense urban setting, where space is always at a premium. In order to address the challenges outlined above, the hospital sought a solution that would provide real-time inventory information with high levels of accuracy, reduce the level of manual effort required and enable data driven decision making to ensure that the right supplies were readily available to clinicians in the right location at the right time.
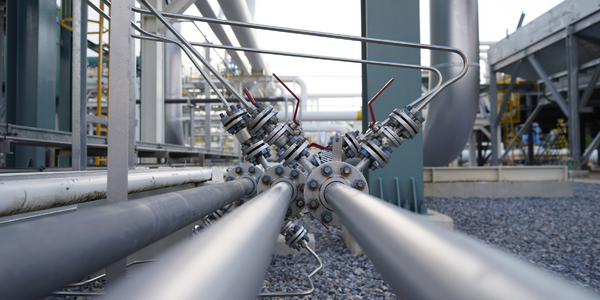
Case Study
Gas Pipeline Monitoring System for Hospitals
This system integrator focuses on providing centralized gas pipeline monitoring systems for hospitals. The service they provide makes it possible for hospitals to reduce both maintenance and labor costs. Since hospitals may not have an existing network suitable for this type of system, GPRS communication provides an easy and ready-to-use solution for remote, distributed monitoring systems System Requirements - GPRS communication - Seamless connection with SCADA software - Simple, front-end control capability - Expandable I/O channels - Combine AI, DI, and DO channels
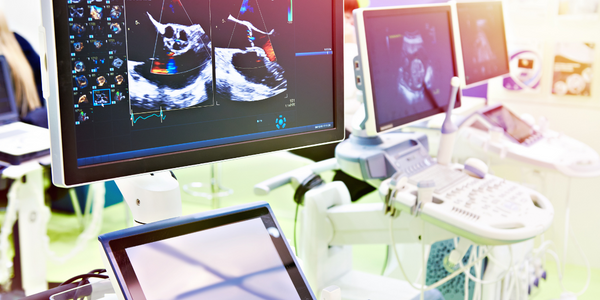
Case Study
Driving Digital Transformations for Vitro Diagnostic Medical Devices
Diagnostic devices play a vital role in helping to improve healthcare delivery. In fact, an estimated 60 percent of the world’s medical decisions are made with support from in vitrodiagnostics (IVD) solutions, such as those provided by Roche Diagnostics, an industry leader. As the demand for medical diagnostic services grows rapidly in hospitals and clinics across China, so does the market for IVD solutions. In addition, the typically high cost of these diagnostic devices means that comprehensive post-sales services are needed. Wanteed to improve three portions of thr IVD:1. Remotely monitor and manage IVD devices as fixed assets.2. Optimizing device availability with predictive maintenance.3. Recommending the best IVD solution for a customer’s needs.
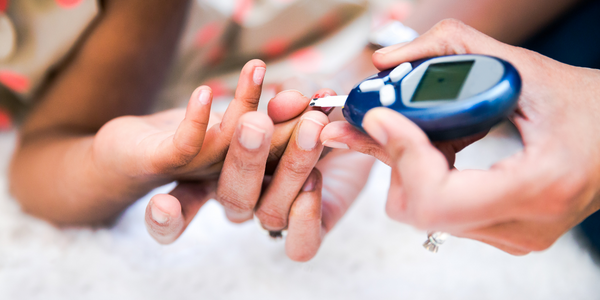
Case Study
HaemoCloud Global Blood Management System
1) Deliver a connected digital product system to protect and increase the differentiated value of Haemonetics blood and plasma solutions. 2) Improve patient outcomes by increasing the efficiency of blood supply flows. 3) Navigate and satisfy a complex web of global regulatory compliance requirements. 4) Reduce costly and labor-intensive maintenance procedures.
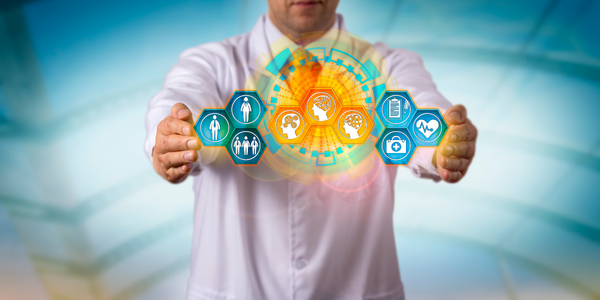
Case Study
Harnessing real-time data to give a holistic picture of patient health
Every day, vast quantities of data are collected about patients as they pass through health service organizations—from operational data such as treatment history and medications to physiological data captured by medical devices. The insights hidden within this treasure trove of data can be used to support more personalized treatments, more accurate diagnosis and more advanced preparative care. But since the information is generated faster than most organizations can consume it, unlocking the power of this big data can be a struggle. This type of predictive approach not only improves patient care—it also helps to reduce costs, because in the healthcare industry, prevention is almost always more cost-effective than treatment. However, collecting, analyzing and presenting these data-streams in a way that clinicians can easily understand can pose a significant technical challenge.