SYSPRO case study Loftness Manufacturing
公司规模
200-1,000
地区
- America
国家
- Canada
- United States
产品
- SYSPRO Manufacturing
- SYSPRO Financials
- SYSPRO Report Writer
- SQL Manager
- Product Configurator
技术栈
- SQL Database
- Windows GUI
实施规模
- Enterprise-wide Deployment
影响指标
- Customer Satisfaction
- Digital Expertise
- Productivity Improvements
技术
- 功能应用 - 企业资源规划系统 (ERP)
- 功能应用 - 制造执行系统 (MES)
- 功能应用 - 产品数据管理系统
适用行业
- 农业
适用功能
- 离散制造
- 仓库和库存管理
用例
- 库存管理
- 自动化制造系统
- 预测性维护
服务
- 系统集成
- 培训
关于客户
Loftness Manufacturing, established in 1956 in Hector, Minnesota, started by making V-type snow blowers in response to local demand. Today, the company produces a wide range of high-quality, durable equipment for agriculture, forestry, landscape, and right-of-way maintenance. Their product lines include brands like GrainLogix, CropLogix, VM-Logix, and SnowLogix, all known for their quality and durability. Loftness operates from a single sprawling building in Hector, which houses two warehouses and a storage yard. The company processes approximately 4,000 orders a month from a customer base of 2,600, including dealers and consumers in the USA and Canada.
挑战
A number of years ago, Loftness identified a need to upgrade to a SQL database, create custom reports, better manage data and expand functionality. The company also aimed to optimize SYSPRO’s functionality to enhance various operational aspects such as jobs processing, inventory transactions, sales order processing, and MRP. The goal was to institute training and process disciplines that would fully utilize SYSPRO’s capabilities, thereby ensuring inventory accuracy, smooth product flow, and efficient operations.
解决方案
SYSPRO software was chosen to meet Loftness Manufacturing’s requirements. The software operates on an HP Proliant with 24 concurrent users. SYSPRO’s functionalities, such as jobs processing, inventory transactions, sales order processing, and MRP, were fully utilized. Training and process disciplines were instituted to integrate SYSPRO into the company’s procedures, ensuring inventory accuracy, smooth product flow, and efficient operations. The software also facilitated better production planning and customer service, enabling the company to have products ready to ship when customers wanted them. Additionally, SYSPRO helped reduce back-ordered parts and allowed sales personnel to provide reliable information on product availability.
运营影响
数量效益
Case Study missing?
Start adding your own!
Register with your work email and create a new case study profile for your business.
相关案例.
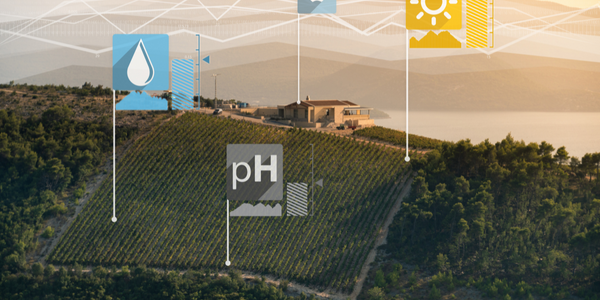
Case Study
Intelligent Farming with ThingWorx Analytics
Z Farms was facing three challenges: costly irrigation systems with water as a limited resource, narrow optimal ranges of soil moisture for growth with difficult maintenance and farm operators could not simply turn on irrigation systems like a faucet.
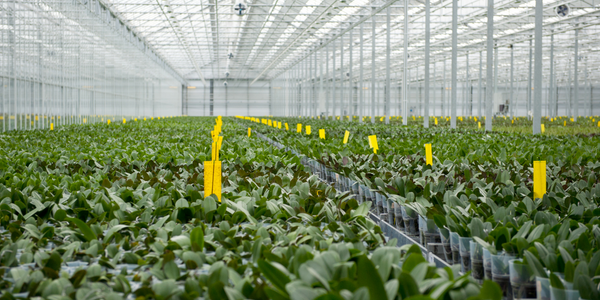
Case Study
Greenhouse Intelligent Monitoring and Control Solution
Farming Orchids is the most successful form of precision farming in Taiwan, and also the most exported flower. Orchids need a specific temperature and humidity conditions to grow and bloom, and its flowering time may not be in line with market demands, so the price collapses when there is overproduction. Therefore, some farmers began to import automated greenhouse control systems for breeding and forcing, which not only improves quality, but also effectively controls the production period and yield to ensure revenue. In 2012, an orchid farmer built a Forcing Greenhouse of about 200 pings (approximately 661 Square Meters) in Tainan, Taiwan. The system integrator adopted Advantech’s APAX-5000 series programmable automation controllers to build the control platform, coupled with Advantech WebAccess HMI/SCADA software, to achieve cloud monitoring. The staff of the orchid field can monitor important data anytime via smart phone, iPad, and other handheld devices, and control the growth and flowering conditions. System requirements: In the past, most environmental control systems of orchid greenhouses in Taiwan used PLCs (Programmable Logic Controller) with poorscalability and control, and could not be connected to the Internet formonitoring from the cloud. For advanced database analysis and networking capability, the PC platform must be adopted. Therefore, PAC Systems (Programmable Automation Controller) with both PLC programming capabilities andPC functions is a better choice.The environmental control of the Orchid greenhouse switches on and off devices like fan, shade net, cooling/heat pump, liquid flow control, water-cooling wall etc. It is controlled by a control panel of electric controllers, and is driven by a motor, to adjust the greenhouse temperature, humidity, and other environmental conditions to the set parameters.
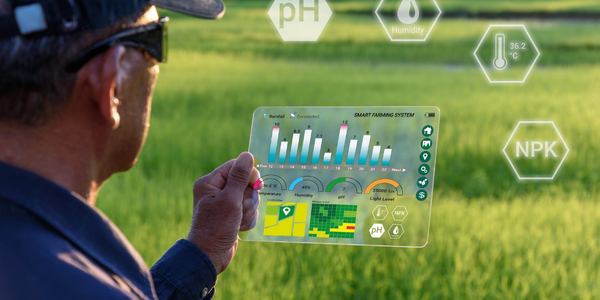
Case Study
Enabling Internet of Things Innovation in Agriculture
DigiBale, wanted to apply technology know-how and IP from implementations successfully to more agriculture sectors including cotton, forestry, sugarcane and cattle. However, farmers and growers still have worries about the connected technology.
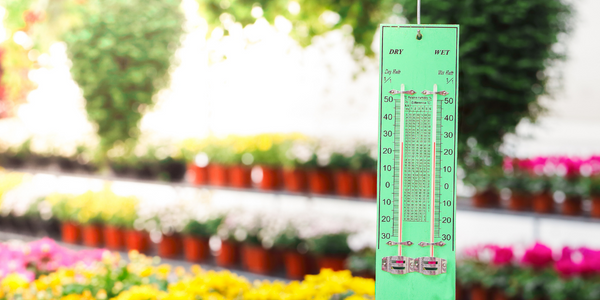
Case Study
Precision beekeeping with wireless temperature monitoring
Honeybees are insects of large economic value and provide a vital service to agriculture by pollinating a variety of crops. In addition, bees provide us with valuable products such as honey, beeswax, propolis, bee venom, etc. Monitoring of honeybee colony health, population, productivity, and environmental conditions affecting the colony health have always been exceedingly difficult tasks in apiculture. Research has shown that even small deviations (by more than 2°C) from the optimal temperatures have a significant influence on the development of the brood and the health of adult bees.