SYSPRO Case Study KWALU
公司规模
Mid-size Company
地区
- America
国家
- United States
产品
- SYSPRO Financials
- SYSPRO e.net Solutions
- SYSPRO CRM
- SQL Manager
- e.net Manager
技术栈
- Microsoft Platform
- SQL 2000
- Unix Platform
- Bar Coding
- Email Integration
实施规模
- Enterprise-wide Deployment
影响指标
- Cost Savings
- Customer Satisfaction
- Productivity Improvements
- Digital Expertise
技术
- 功能应用 - 企业资源规划系统 (ERP)
- 应用基础设施与中间件 - 数据交换与集成
适用功能
- 商业运营
- 质量保证
- 仓库和库存管理
用例
- 库存管理
- 预测性维护
- 过程控制与优化
- 供应链可见性(SCV)
服务
- 系统集成
- 软件设计与工程服务
- 培训
关于客户
Kwalu, based in Ridgeland, South Carolina, custom manufactures highly durable furniture for hospitals, schools, hotels, and numerous other business entities. Founded in 1984, the company’s modular product line enables customers to mix and match different styles of frames with various choices of upholstery to create uniquely customized designs that are as beautiful as they are durable. Kwalu also offers coordinating wainscot, handrails, corner and wall guards, and wall coverings to complete the look each client wants to achieve. Kwalu furniture and associated products use a processed material that captures the beauty of wood but is far more durable. The patented process, developed by Kwalu, involves the production of high-impact resistant polymers that mimic wood grain. The graining appears throughout the product, enabling the sanding of scuffs, scratches, and other damages without the need to re-stain or re-finish the surface. Kwalu prides itself on the fact that the modularity of its products makes the company a single source for designers and facilities. Kwalu also believes the durability of its products is unmatched in the furniture industry and commensurately offers a 10-year warranty covering both finish and construction. Kwalu’s roster of customers numbers well over 10,000. The company’s orders are generated both nationally and internationally from a network of dealers, independent representatives, and distributors.
挑战
When MIS Manager Erwin Bartsch joined Kwalu some seven years ago, he ‘inherited’ the currently implemented software, SYSPRO, running on a Unix platform. Rather than seek a new software solution, Bartsch decided to work with SYSPRO to determine whether there was a need to replace the system. Kwalu faced unique requirements, a high degree of customization, and exponential growth. The company needed a solution that could handle these challenges effectively.
解决方案
The more Bartsch worked with the solution, the more he felt it to be ideal for Kwalu. Today, 24 concurrent users work with SYSPRO running on a Microsoft platform on top of SQL 2000. The company’s manufacturing plant and two warehouses tie into the corporate office computer through a bonded T1 connection. Bartsch believes there is no reason to switch from SYSPRO. “SYSPRO continues to be an innovator in software development and continually develops its product to keep pace with technological advances,” he says. “SYSPRO keeps up with the demands of our business.” He also feels this assessment is validated by the number of awards SYSPRO continues to win. Bartsch says SYSPRO accommodates the company’s unique requirements. He likes the adaptability of the product, the add-on modules, bar coding, SQL, and email integration. He also appreciates the ability to customize the software through SYSPRO e.net Solutions and is anticipating using it to automate information sent to customers regarding the status of their orders, delivery dates, billings, and other similar data.
运营影响
数量效益
Case Study missing?
Start adding your own!
Register with your work email and create a new case study profile for your business.
相关案例.

Case Study
Remote Monitoring & Predictive Maintenance App for a Solar Energy System
The maintenance & tracking of various modules was an overhead for the customer due to the huge labor costs involved. Being an advanced solar solutions provider, they wanted to ensure early detection of issues and provide the best-in-class customer experience. Hence they wanted to automate the whole process.

Case Study
Remote Temperature Monitoring of Perishable Goods Saves Money
RMONI was facing temperature monitoring challenges in a cold chain business. A cold chain must be established and maintained to ensure goods have been properly refrigerated during every step of the process, making temperature monitoring a critical business function. Manual registration practice can be very costly, labor intensive and prone to mistakes.
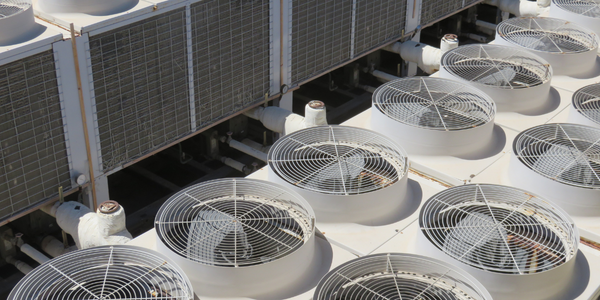
Case Study
Predictive Maintenance for Industrial Chillers
For global leaders in the industrial chiller manufacturing, reliability of the entire production process is of the utmost importance. Chillers are refrigeration systems that produce ice water to provide cooling for a process or industrial application. One of those leaders sought a way to respond to asset performance issues, even before they occur. The intelligence to guarantee maximum reliability of cooling devices is embedded (pre-alarming). A pre-alarming phase means that the cooling device still works, but symptoms may appear, telling manufacturers that a failure is likely to occur in the near future. Chillers who are not internet connected at that moment, provide little insight in this pre-alarming phase.

Case Study
System 800xA at Indian Cement Plants
Chettinad Cement recognized that further efficiencies could be achieved in its cement manufacturing process. It looked to investing in comprehensive operational and control technologies to manage and derive productivity and energy efficiency gains from the assets on Line 2, their second plant in India.
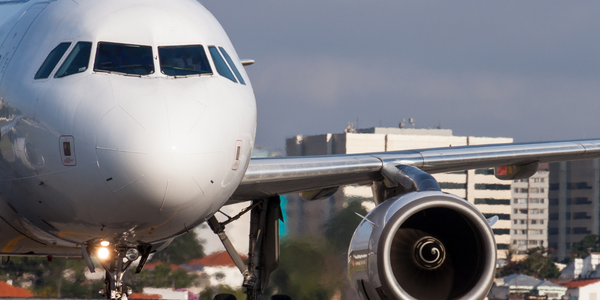
Case Study
Airbus Soars with Wearable Technology
Building an Airbus aircraft involves complex manufacturing processes consisting of thousands of moving parts. Speed and accuracy are critical to business and competitive advantage. Improvements in both would have high impact on Airbus’ bottom line. Airbus wanted to help operators reduce the complexity of assembling cabin seats and decrease the time required to complete this task.