公司规模
Large Corporate
地区
- America
国家
- Mexico
- Canada
- United States
产品
- Blue Yonder transportation management
- Luminate Control Tower
技术栈
- Artificial Intelligence
实施规模
- Enterprise-wide Deployment
影响指标
- Cost Savings
- Productivity Improvements
- Customer Satisfaction
技术
- 平台即服务 (PaaS) - 连接平台
适用功能
- 物流运输
用例
- 供应链可见性(SCV)
- 实时定位系统 (RTLS)
- 预测性维护
服务
- 系统集成
关于客户
Traxion 是墨西哥最大的物流供应商,拥有 8,000 辆车和 1,000 多家客户。自 2011 年成立以来,该公司规模增长了 28 倍,是其最接近的竞争对手的三倍。Traxion 所在的市场增长迅速,墨西哥第三方物流市场在疫情爆发前每年的增长率高达 25%。疫情进一步加速了增长,2020 年墨西哥的电子商务增长了一倍,将三年的物流需求压缩到了一年。Traxion 的客户群在增长,客户的要求也在增长。该公司需要最大限度地提高速度和响应能力,同时控制成本并确保盈利能力。
挑战
墨西哥最大的物流供应商 Traxion 自 2011 年成立以来,增长了 28 倍。Traxion 拥有 8,000 辆车和 1,000 多家客户,规模是其最接近的竞争对手的三倍。随着 Traxion 的客户群不断增长,客户需求也在不断增长。该公司需要最大限度地提高速度和响应能力,同时控制成本并确保盈利能力。2020 年之前,墨西哥第三方物流市场每年的增长率高达 25%。疫情大大加速了这一增长,2020 年墨西哥的电子商务增长了一倍,将三年的物流需求压缩到了一年。
解决方案
Traxion 与 Blue Yonder 合作实施其运输管理解决方案以及 Luminate Control Tower,以获得内部供应链和扩展合作伙伴网络的实时可见性。Blue Yonder 的运输管理解决方案使 Traxion 能够量化节省和机会,平衡服务水平和成本权衡,并确定执行的优先级。Traxion 可以评估整个网络的性能,以及排除中断故障,以提高可靠性和节省成本。在日常运营中,Traxion 受益于 Blue Yonder 先进的路线、模式、集装箱和服务水平优化,以及整个供应链的库存感知。在人工智能的支持下,运输管理解决方案可以根据条件的变化自动执行和重新规划。Luminate Control Tower 为 Traxion 提供了其合作伙伴网络中事件的统一视图。关键警报可帮助规划人员实时预测中断并预测对库存、生产能力和销售的影响。
运营影响
数量效益
Case Study missing?
Start adding your own!
Register with your work email and create a new case study profile for your business.
相关案例.

Case Study
Remote Monitoring & Predictive Maintenance App for a Solar Energy System
The maintenance & tracking of various modules was an overhead for the customer due to the huge labor costs involved. Being an advanced solar solutions provider, they wanted to ensure early detection of issues and provide the best-in-class customer experience. Hence they wanted to automate the whole process.

Case Study
Remote Temperature Monitoring of Perishable Goods Saves Money
RMONI was facing temperature monitoring challenges in a cold chain business. A cold chain must be established and maintained to ensure goods have been properly refrigerated during every step of the process, making temperature monitoring a critical business function. Manual registration practice can be very costly, labor intensive and prone to mistakes.
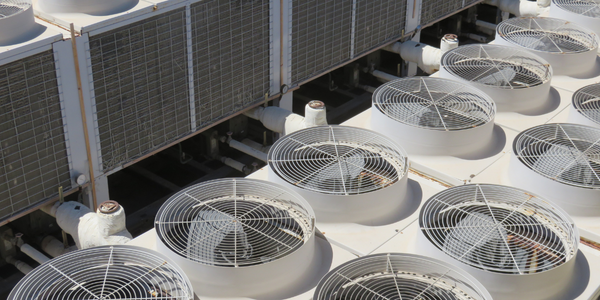
Case Study
Predictive Maintenance for Industrial Chillers
For global leaders in the industrial chiller manufacturing, reliability of the entire production process is of the utmost importance. Chillers are refrigeration systems that produce ice water to provide cooling for a process or industrial application. One of those leaders sought a way to respond to asset performance issues, even before they occur. The intelligence to guarantee maximum reliability of cooling devices is embedded (pre-alarming). A pre-alarming phase means that the cooling device still works, but symptoms may appear, telling manufacturers that a failure is likely to occur in the near future. Chillers who are not internet connected at that moment, provide little insight in this pre-alarming phase.
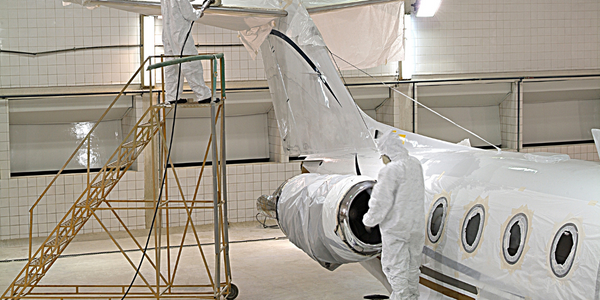
Case Study
Aircraft Predictive Maintenance and Workflow Optimization
First, aircraft manufacturer have trouble monitoring the health of aircraft systems with health prognostics and deliver predictive maintenance insights. Second, aircraft manufacturer wants a solution that can provide an in-context advisory and align job assignments to match technician experience and expertise.
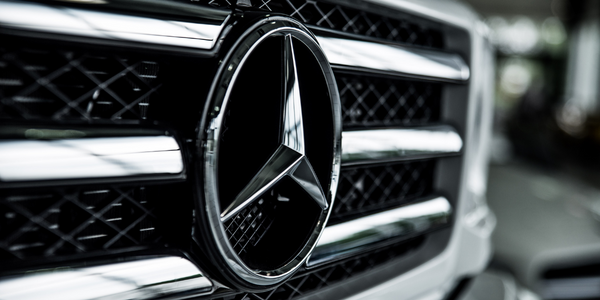
Case Study
Integral Plant Maintenance
Mercedes-Benz and his partner GAZ chose Siemens to be its maintenance partner at a new engine plant in Yaroslavl, Russia. The new plant offers a capacity to manufacture diesel engines for the Russian market, for locally produced Sprinter Classic. In addition to engines for the local market, the Yaroslavl plant will also produce spare parts. Mercedes-Benz Russia and his partner needed a service partner in order to ensure the operation of these lines in a maintenance partnership arrangement. The challenges included coordinating the entire maintenance management operation, in particular inspections, corrective and predictive maintenance activities, and the optimizing spare parts management. Siemens developed a customized maintenance solution that includes all electronic and mechanical maintenance activities (Integral Plant Maintenance).
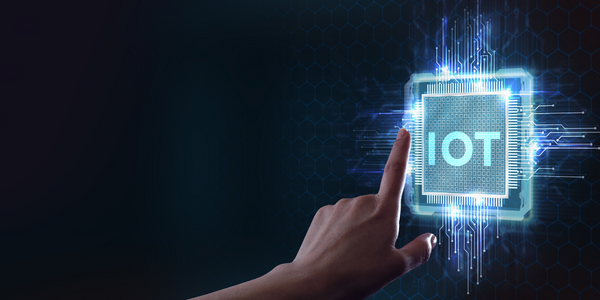
Case Study
Leading Tools Manufacturer Transforms Operations with IoT
Stanley Black & Decker required transparency of real-time overall equipment effectiveness and line productivity to reduce production line change over time.The goal was to to improve production to schedule, reduce actual labor costs and understanding the effects of shift changes and resource shifts from line to line.