Simplifying Complex Logistics for Santander Banks
公司规模
Large Corporate
地区
- America
- Europe
- Asia
国家
- United States
- Spain
产品
- Digibee Hybrid Integration Platform (HIP)
技术栈
- Hybrid Integration Platform
- End-to-End Encryption
- Real-Time Tracking
实施规模
- Enterprise-wide Deployment
影响指标
- Cost Savings
- Productivity Improvements
- Customer Satisfaction
技术
- 平台即服务 (PaaS) - 连接平台
- 应用基础设施与中间件 - 数据交换与集成
- 应用基础设施与中间件 - 中间件、SDK 和库
适用功能
- 物流运输
- 商业运营
用例
- 资产跟踪
- 车队管理
- 过程控制与优化
- 远程资产管理
服务
- 系统集成
- 云规划/设计/实施服务
- 网络安全服务
关于客户
Santander Bank, N.A. is one of the largest retail and commercial banks in the United States, providing a range of services including capital, treasury management, risk management, and international solutions. The bank is a wholly-owned subsidiary of Madrid-based Banco Santander, S.A., one of the most respected banking groups globally, with over 125 million customers across the U.S., Europe, and Latin America. Santander's Global Platform segment focuses on global payments services, fully digital banking, and digital assets. The bank's headquarters are in Boston, MA, and it employs over 196,400 people.
挑战
Santander Bank needed to integrate a broad and complex logistics network to distribute paper currency. The network included various entities such as bank branches, ATMs, stores, main depots, central banks, and security transportation companies. The existing process was highly manual, involving hundreds of people, thousands of emails, and various versioned spreadsheets, making operations slow and non-secure. The commercial bank aimed to make its operations more efficient and protected, as the manual process made near real-time tracking and monitoring almost impossible.
解决方案
Santander Bank implemented the Digibee Hybrid Integration Platform (HIP) to integrate its transport requests and track the status of its security transport operations nationwide in near real-time. The solution integrated Santander's operations with Cash-in-Transit Companies (CIT), despite the diversity of systems and different maturity levels of processes. The Digibee HIP streamlined the process, heightened security, and increased efficiency while reducing operational costs. The platform encrypted all messages end-to-end, provided visibility to track the process in near real-time, and simplified integration complexities between different systems and protocols.
运营影响
数量效益
Case Study missing?
Start adding your own!
Register with your work email and create a new case study profile for your business.
相关案例.
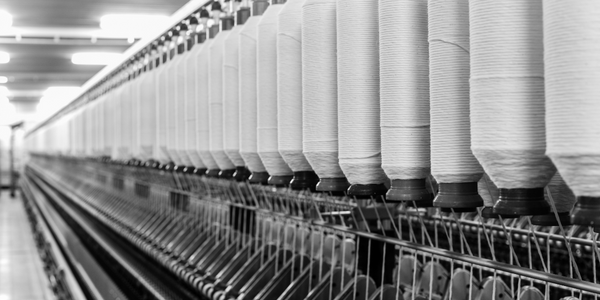
Case Study
IoT Applications and Upgrades in Textile Plant
At any given time, the textile company’s manufacturing facility has up to 2,000 textile carts in use. These carts are pushed from room to room, carrying materials or semi-finished products. Previously, a paper with a hand-written description was attached to each cart. This traditional method of processing made product tracking extremely difficult. Additionally, making sure that every cart of materials or semi-finished products went to its correct processing work station was also a problem. Therefore, the company desired an intelligent solution for tracking assets at their factories. They also wanted a solution that would help them collect process data so they could improve their manufacturing efficiency.
.png)
Case Study
Improving Vending Machine Profitability with the Internet of Things (IoT)
The vending industry is undergoing a sea change, taking advantage of new technologies to go beyond just delivering snacks to creating a new retail location. Intelligent vending machines can be found in many public locations as well as company facilities, selling different types of goods and services, including even computer accessories, gold bars, tickets, and office supplies. With increasing sophistication, they may also provide time- and location-based data pertaining to sales, inventory, and customer preferences. But at the end of the day, vending machine operators know greater profitability is driven by higher sales and lower operating costs.
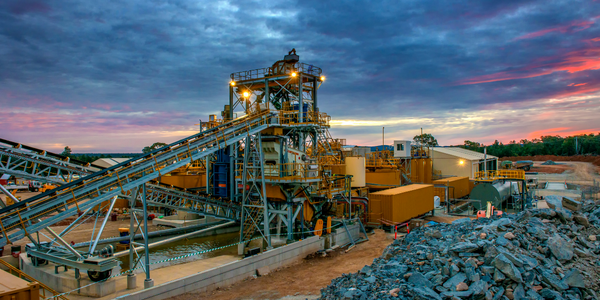
Case Study
Goldcorp: Internet of Things Enables the Mine of the Future
Goldcorp is committed to responsible mining practices and maintaining maximum safety for its workers. At the same time, the firm is constantly exploring ways to improve the efficiency of its operations, extend the life of its assets, and control costs. Goldcorp needed technology that can maximize production efficiency by tracking all mining operations, keep employees safe with remote operations and monitoring of hazardous work areas and control production costs through better asset and site management.

Case Study
Remote Wellhead Monitoring
Each wellhead was equipped with various sensors and meters that needed to be monitored and controlled from a central HMI, often miles away from the assets in the field. Redundant solar and wind generators were installed at each wellhead to support the electrical needs of the pumpstations, temperature meters, cameras, and cellular modules. In addition to asset management and remote control capabilities, data logging for remote surveillance and alarm notifications was a key demand from the customer. Terra Ferma’s solution needed to be power efficient, reliable, and capable of supporting high-bandwidth data-feeds. They needed a multi-link cellular connection to a central server that sustained reliable and redundant monitoring and control of flow meters, temperature sensors, power supply, and event-logging; including video and image files. This open-standard network needed to interface with the existing SCADA and proprietary network management software.