地区
- America
国家
- United States
产品
- Fleet Management Services
技术栈
- Not mentioned
实施规模
- Enterprise-wide Deployment
影响指标
- Cost Savings
- Productivity Improvements
技术
- 功能应用 - 车队管理系统 (FMS)
适用功能
- 物流运输
用例
- 车队管理
- 远程资产管理
服务
- 系统集成
关于客户
The customer is a business services company that operates a service fleet with trucks, vans, and material handling equipment. The fleet consists of over 70 forklifts spread over 11 facilities. The company was under intense pressure to reduce costs associated with its material handling equipment. Each facility handled its own maintenance needs using a variety of manufacturers/providers. There was no centralized oversight or visibility into costs and effectiveness.
挑战
The customer, a business services company, was under intense pressure to reduce costs associated with its material handling equipment used in its facilities. The customer operated approximately 70 units, mostly forklifts, in 11 sites around the United States. Each facility handled its own maintenance needs using a variety of manufacturers/providers. There was no centralized oversight or visibility into costs and effectiveness. The lack of centralized oversight led to a lack of visibility into the actual number of units and the costs associated with their maintenance.
解决方案
Element Fleet Management conducted thorough, on-site surveys of the customer’s material handling equipment inventory and uncovered more units than the customer thought it had. As a brand-neutral third party, Element was able to incorporate all the OEMs the customer had been using into an open network of providers. Now all maintenance transactions and billing came through Element to manage. A material handling equipment analyst, with 20 years of forklift experience, was dedicated to the customer’s account; he audited and analyzed all repair invoices, and negotiated invoice credits and adjustments where costs/repairs were above industry standards.
运营影响
数量效益
Case Study missing?
Start adding your own!
Register with your work email and create a new case study profile for your business.
相关案例.
.png)
Case Study
Improving Vending Machine Profitability with the Internet of Things (IoT)
The vending industry is undergoing a sea change, taking advantage of new technologies to go beyond just delivering snacks to creating a new retail location. Intelligent vending machines can be found in many public locations as well as company facilities, selling different types of goods and services, including even computer accessories, gold bars, tickets, and office supplies. With increasing sophistication, they may also provide time- and location-based data pertaining to sales, inventory, and customer preferences. But at the end of the day, vending machine operators know greater profitability is driven by higher sales and lower operating costs.

Case Study
Remote Wellhead Monitoring
Each wellhead was equipped with various sensors and meters that needed to be monitored and controlled from a central HMI, often miles away from the assets in the field. Redundant solar and wind generators were installed at each wellhead to support the electrical needs of the pumpstations, temperature meters, cameras, and cellular modules. In addition to asset management and remote control capabilities, data logging for remote surveillance and alarm notifications was a key demand from the customer. Terra Ferma’s solution needed to be power efficient, reliable, and capable of supporting high-bandwidth data-feeds. They needed a multi-link cellular connection to a central server that sustained reliable and redundant monitoring and control of flow meters, temperature sensors, power supply, and event-logging; including video and image files. This open-standard network needed to interface with the existing SCADA and proprietary network management software.
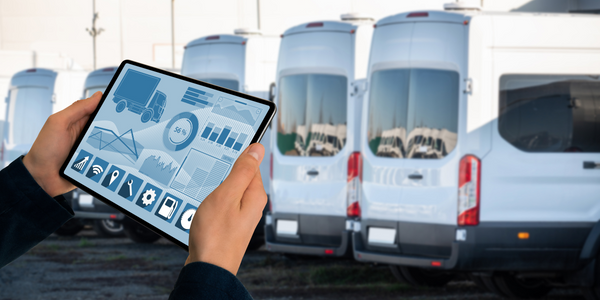
Case Study
IoT-based Fleet Intelligence Innovation
Speed to market is precious for DRVR, a rapidly growing start-up company. With a business model dependent on reliable mobile data, managers were spending their lives trying to negotiate data roaming deals with mobile network operators in different countries. And, even then, service quality was a constant concern.