公司规模
Large Corporate
地区
- Europe
国家
- Poland
- United Kingdom
产品
- IBM Global Technology Services
- IBM Global Process Services
- IBM WebSphere Business Modeler
- IBM Content Manager
技术栈
- IBM WebSphere
- SAP ERP
实施规模
- Enterprise-wide Deployment
影响指标
- Cost Savings
- Productivity Improvements
- Digital Expertise
技术
- 平台即服务 (PaaS) - 连接平台
适用行业
- 消费品
适用功能
- 离散制造
- 采购
用例
- 过程控制与优化
- 供应链可见性(SCV)
- 库存管理
服务
- 云规划/设计/实施服务
- 数据科学服务
关于客户
联合利华欧洲是全球最知名、最受尊敬的品牌之一,年收入超过 440 亿欧元。该公司在五大洲的约 100 个国家开展业务。它管理着 14 个不同类别的 500 多个独立品牌,拥有超过 167,000 名员工。联合利华欧洲占联合利华全球业务的 32%,拥有 32,000 名员工。该公司的使命一直是帮助人们保持美丽、感觉良好并为他们的生活增添活力。然而,面对疲软的营收和高昂的成本结构,联合利华欧洲需要进行重大的运营变革。
挑战
著名消费品巨头联合利华欧洲公司曾以国家和部门为单位以孤立方式扩张。这导致其在 24 个国家/地区形成了一个松散的业务集团和地区联盟,全部使用多个 ERP 系统。由于三个独立的领导团队负责处理许多不同的财务和会计流程,导致组织复杂、效率低下,阻碍了增长。2005 年,联合利华欧洲公司的领导团队做出一项战略决策,将公司的多个业务部门整合为一个统一的泛欧组织,但需要实施系统和框架来实现这一目标。欧洲各地文化、政策和语言的多样性进一步加剧了挑战,公司各个业务部门的技术水平参差不齐,既有先进的纸质系统,也有过时的纸质系统。
解决方案
2005 年,联合利华欧洲公司与 IBM 结成合作伙伴关系,创建了一个集中化的“一个联合利华”财务组织。该高度变革性的解决方案以流程创新和高级分析为基础,为联合利华欧洲公司提供了更高的质量、控制和信息访问能力,并创建了一个更灵活、适应性更强的运营模式。IBM 通过位于波兰克拉科夫、葡萄牙布拉加、印度班加罗尔和菲律宾马尼拉的设施,以三层交付模式提供托管业务流程服务。IBM 部署了工具来标准化和自动化现有流程,这些流程通过通用工作流技术连接起来,并在已建立的全球交付基础架构中无缝一致地交付。联合利华欧洲公司的财务流程现已协调一致,使工作能够轻松地在全球中心之间转移。
运营影响
数量效益
Case Study missing?
Start adding your own!
Register with your work email and create a new case study profile for your business.
相关案例.
.png)
Case Study
Improving Vending Machine Profitability with the Internet of Things (IoT)
The vending industry is undergoing a sea change, taking advantage of new technologies to go beyond just delivering snacks to creating a new retail location. Intelligent vending machines can be found in many public locations as well as company facilities, selling different types of goods and services, including even computer accessories, gold bars, tickets, and office supplies. With increasing sophistication, they may also provide time- and location-based data pertaining to sales, inventory, and customer preferences. But at the end of the day, vending machine operators know greater profitability is driven by higher sales and lower operating costs.
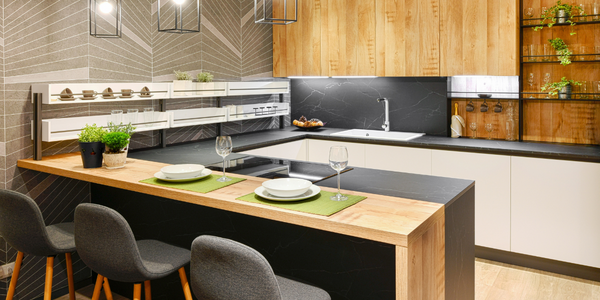
Case Study
Series Production with Lot-size-1 Flexibility
Nobilia manufactures customized fitted kitchens with a lot size of 1. They require maximum transparency of tracking design data and individual processing steps so that they can locate a particular piece of kitchen furniture in the sequence of processes.
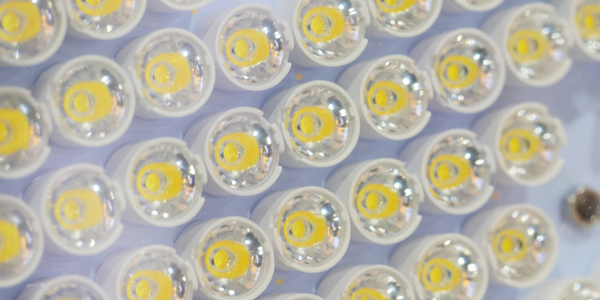
Case Study
American Eagle Achieves LEED with GE LED Lighting Fixtures
American Eagle Outfitters (AEO) was in the process of building a new distribution center. The AEO facility management team decided to look at alternate options for lighting layout that could provide energy and maintenance savings. AEO would need a full-time maintenance employee just to replace burned-out fluorescent tubes.
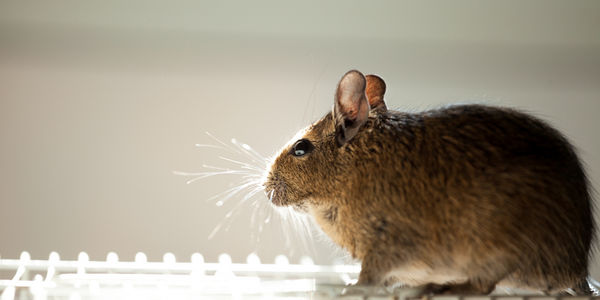
Case Study
Revolutionizing Rodent Control
From pet- and child-safe traps, to touch-free and live-catch rodent control solutions, Victor continues to stay committed to producing superior products that meet the varying needs of today’s pest control professionals. And, with a long standing history supporting customers in the food processing, service, and retail settings, Victor knew that strict regulations were costing organizations thousands of dollars in excess overhead trying to manage their rodent-control solutions. Trap inspections in these environments are often difficult and time consuming, requiring personnel to manually check a trap’s status multiple times per day, amounting to over six hours of manual labor. Victor is looking for an innovative way to increase operational efficiencies with the use of technology.