Praxair Employes NWA for Ultra-Pure Process Gas Customer Satisfication
公司规模
Large Corporate
地区
- America
- Europe
- Asia
国家
- United States
- Belgium
- Korea
- Taiwan
产品
- NWA Quality Analyst
- Oracle Database
技术栈
- SPC (Statistical Process Control)
- Oracle Database
- Electronic Data Interchange (EDI)
实施规模
- Enterprise-wide Deployment
影响指标
- Cost Savings
- Productivity Improvements
- Customer Satisfaction
- Waste Reduction
技术
- 分析与建模 - 预测分析
- 应用基础设施与中间件 - 数据库管理和存储
- 功能应用 - 企业资源规划系统 (ERP)
适用行业
- 半导体
- 电子产品
适用功能
- 质量保证
- 流程制造
用例
- 预测性维护
- 过程控制与优化
- 机器状态监测
- 远程资产管理
服务
- 系统集成
- 数据科学服务
- 培训
关于客户
Praxair Electronics produces process and precursor gases used by the majority of semiconductor chip and solar cell manufacturers. The Praxair product line includes ammonia, silane, dichlorosilane, arsine, phospine dopant mixtures, inert gases, halocarbon etchant gases, and support products and services. As one of the top players in semiconductor industry gases and related services, Praxair ships high purity gas cylinders around the world to its customers. The data-management system at the Kingman, AZ plant was used as the benchmark model to apply the same methods to ramping up the Quality Analyst systems at other Praxair gas plants in Oevel, Belgium; Giheung and Tangjung, Korea; and Toufen, Taiwan. This global effort has resulted in highly successful customer retention and expanded global business. Praxair is dealing with over 7,000 products and tracking from one to twelve quality parameters per product.
挑战
Gas contamination and variation affect chip yield rates and the required reduction in impurity levels for successful chip production. Continuous Process Improvement (CPI) drives performance to meet the requirements. To meet their CPI goals, Praxair uses NWA Quality Analyst to drive control limits tighter and decrease variation. Business requirements are driving the move to less variation and higher process capability. Many customers are demanding tighter process control and “ship-to-control” capability. Vendors such as Praxair who actively use SPC and CPI can successfully negotiate specifications with regard to their actual process capability and guarantee they will be a capable supplier. Their production is at least three sigma level, and with the ongoing CPI program they have projects in place to improve process capability to meet the evolving business demands.
解决方案
Praxair has implemented NWA Quality Analyst to drive control limits tighter and decrease variation. The data-management system at the Kingman, AZ plant was used as the benchmark model to apply the same methods to ramping up the Quality Analyst systems at other Praxair gas plants in Oevel, Belgium; Giheung and Tangjung, Korea; and Toufen, Taiwan. This global effort has resulted in highly successful customer retention and expanded global business. In the lab, they have interfaced 45 instruments to automatically generate results that are passed into an Oracle database where they are used to generate Certificates of Analysis (COAs) and Electronic Data Interchange (EDI). Most customer electronic systems are set up to automatically decline or accept the lots based on this information. The Quality Analyst automated execution and database linkage produces near-real-time results. All laboratory data enters the Oracle database, and the continuing project is integrating production equipment data into the database. Machine measurement integration is rapidly leading to real-time, on-line process control. Since most failures develop gradually, using SPC detects trends long before they become problems. The engineers can predict vacuum pump and purification trap failures months before an out-of-specification excursion occurs.
运营影响
数量效益
Case Study missing?
Start adding your own!
Register with your work email and create a new case study profile for your business.
相关案例.

Case Study
Remote Temperature Monitoring of Perishable Goods Saves Money
RMONI was facing temperature monitoring challenges in a cold chain business. A cold chain must be established and maintained to ensure goods have been properly refrigerated during every step of the process, making temperature monitoring a critical business function. Manual registration practice can be very costly, labor intensive and prone to mistakes.
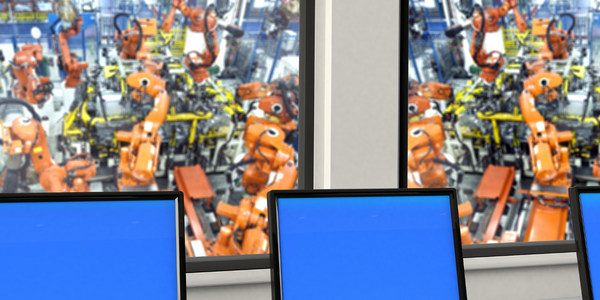
Case Study
KINESYS Semiconductor Factory Automation Software
KINESYS Software provides both Integrated Device Manufacturer (IDM) and Original Equipment Manufacturer (OEM) customers world-class software products and solutions for advanced wafer and device traceability and process management. KINESYS offers state of the art database technology with a core focus on SEMI standards. KINESYS’ challenge was to make back-end processing failure-free and easy to use for clients while supporting licensing models more adaptable to changing industry needs.
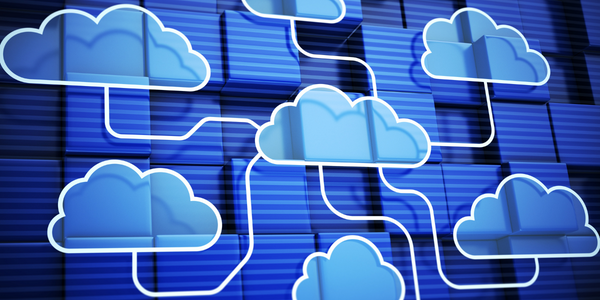
Case Study
Cloud Solution for Energy Management Platform-Schneider Electric
Schneider Electric required a cloud solution for its energy management platform to manage high computational operations, which were essential for catering to client requirements. As the business involves storage and analysis of huge amounts of data, the company also needed a convenient and scalable storage solution to facilitate operations efficiently.
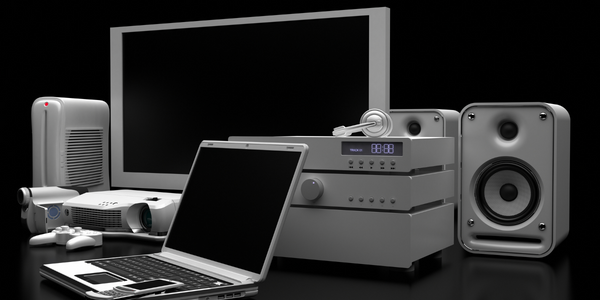
Case Study
Leveraging the IoT to Gain a Competitive Edge in International Competition
Many large manufacturers in and outside Japan are competing for larger market share in the same space, expecting a growing demand for projectors in the areas of entertainment, which requires glamor and strong visual performance as well as digital signage that can attract people’s attention. “It is becoming more and more difficult to differentiate ourselves with stand-alone hardware products,” says Kazuyuki Kitagawa, Director of Service & Support at Panasonic AVC Networks. “In order for Panasonic to grow market share and overall business, it is essential for us to develop solutions that deliver significant added value.” Panasonic believes projection failure and quality deterioration should never happen. This is what and has driven them to make their projectors IoT-enabled. More specifically, Panasonic has developed a system that collects data from projectors, visualizes detailed operational statuses, and predicts issues and address them before failure occurs. Their projectors are embedded with a variety of sensors that measure power supply, voltage, video input/ output signals, intake/exhaust air temperatures, cooling fan operations, and light bulb operating time. These sensors have been used to make the projector more intelligent, automatically suspending operation when the temperature rises excessively, and automatically switching light bulbs. Although this was a great first step, Panasonic projectors were still not equipped with any capability to send the data over a network.