Plastics Components Inc. Leads Global Competition at Home With EnterpriseIQ ERP Software
公司规模
200-1,000
地区
- America
国家
- United States
产品
- EnterpriseIQ ERP software system
- Customer Relationship Management (CRM)
- RealTime Production Monitoring
- Sales and Distribution
- Quality
技术栈
- Oracle database
- Windows-based PCs
实施规模
- Enterprise-wide Deployment
影响指标
- Cost Savings
- Customer Satisfaction
- Productivity Improvements
技术
- 功能应用 - 企业资源规划系统 (ERP)
适用行业
- 塑料
适用功能
- 离散制造
- 质量保证
用例
- 库存管理
- 自动化制造系统
- 预测性维护
服务
- 软件设计与工程服务
- 系统集成
关于客户
Founded in 1989, Plastic Components, Inc. (PCI) is a globally competitive, low-cost producer of critical injection molded thermoplastic parts for original equipment manufacturers. The company is based in Germantown, Wisconsin and has relied on complete process automation to provide the highest quality parts at the lowest possible cost. With 40 dedicated manufacturing cells (presses, robots, parts conveyors and automated material handling systems) producing parts on a fully automated basis 24 hours a day, five days a week, PCI has shipped over one billion molded parts to customers throughout North America since its inception. The company operates 40 molding presses simultaneously 24 hours a day, five days a week with no operators involved in the molding process.
挑战
Plastic Components, Inc. (PCI) is a leading, globally-competitive supplier of critical molded plastic parts for a diverse range of original equipment manufacturers (OEMs). However, the company was struggling with managing operations with several nonintegrated, manual databases, which was putting a heavy load on the company’s staffing resources. Data was scattered throughout the company, and there was no standard for reporting, so information was often unavailable or inaccurate. Without accurate data, PCI couldn’t easily provide value quotes to its customers, and because the system lacked inventory management controls, inventory could not be checked without calling a live person. The company was looking for a single database solution that offered centralized, accurate, and relevant data that was accessible to everyone in the company.
解决方案
PCI selected EnterpriseIQ for its breadth of functionality, easy-to-manage user-friendly format, and the centralized control it provided over core business data. With EnterpriseIQ in place, PCI is more effectively managing information internally and across its entire supply chain. The company relies on EnterpriseIQ to manage everything from manufacturing and plant operations to sales and distribution, finance, payroll, customer relationship management, preventative maintenance, and more. IQAlerts, IQMS’ business activity monitoring module, helps PCI fend off potential problems by notifying the appropriate personnel when a task needs to be accomplished and by warning when an error has been made. PCI also uses IQAlerts to automate electronic delivery of invoices to its customers.
运营影响
数量效益
Case Study missing?
Start adding your own!
Register with your work email and create a new case study profile for your business.
相关案例.

Case Study
Plastic Spoons Case study: Injection Moulding
In order to meet customer expectations by supplying a wide variety of packaging units, from 36 to 1000 spoons per package, a new production and packaging line needed to be built. DeSter wanted to achieve higher production capacity, lower cycle time and a high degree of operator friendliness with this new production line.
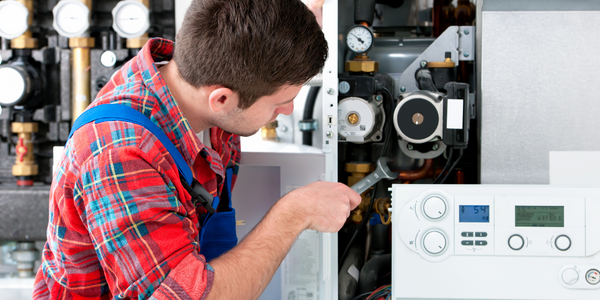
Case Study
Boiler Control System for Plastic Manufacturing Applications
Factory automation applications must be equipped to handle and monitor the myriads of information from attached devices. For plastic manufacturing applications, the boiler control system plays a critical role by gathering and regulating information to ensure production is accurate and smooth. In this particular case, the customer combines eight subsystems that include power meters, water meters, alarm output, displays, and I/O status to be controlled by several intelligent controllers with Modbus RTU interface. The Modbus TCP protocol is used for this application due to the distance. System Requirements: • Modbus serial to Modbus TCP translation • Multiple slaves/masters support • Automatic Modbus TCP response time detection
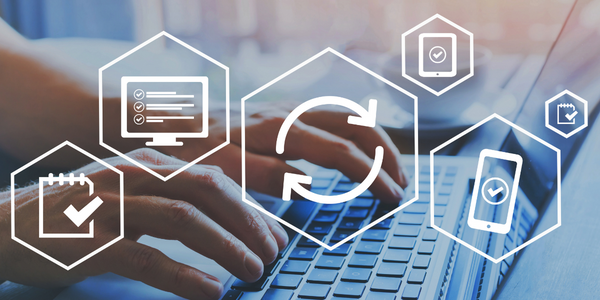
Case Study
Ascend Performance Materials Case Study
Ascend operations must access multiple software systems to manage day-to-day operations in an effective and secure manner. These systems generate large sets of data which contain critical information pertaining to management systems, planning and cost information in business systems and energy consumption. As a result, Ascend management was challenged with creating relevant reports reflecting performance measures in overall context of their operational process. The company’s previous process entailed collecting and analyzing data manually which was not effective, since the information collected was generated after the fact, and was too complex for collaborative use across the organization.
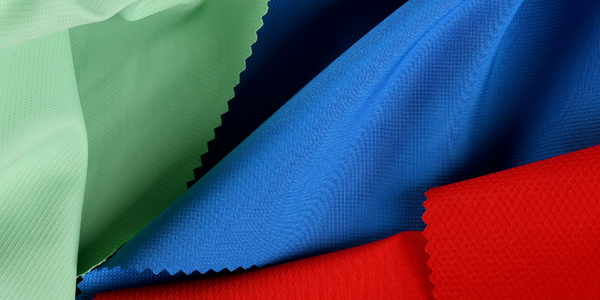
Case Study
Remake Enterprise-to-production System
The client was running a legacy material flow tracking system and wanted to replace the system with a more effective one as the system was increasingly expensive to maintain and support and also was not extendable. The client's IT landscape was filled with modern applications and it was difficult to interface the material flow tracking system with modern applications.