Omni Mold Growth Plan Focuses on Customer Satisfaction
公司规模
1,000+
地区
- Asia
国家
- Singapore
产品
- NX
- Teamcenter
- Unigraphics
技术栈
- 3D CAD/CAM
- Product Lifecycle Management (PLM)
- Web-native environment
实施规模
- Enterprise-wide Deployment
影响指标
- Cost Savings
- Customer Satisfaction
- Productivity Improvements
技术
- 分析与建模 - 预测分析
- 功能应用 - 产品生命周期管理系统 (PLM)
- 功能应用 - 远程监控系统
适用行业
- 汽车
- 电子产品
- 医疗保健和医院
适用功能
- 商业运营
- 产品研发
- 质量保证
用例
- 预测性维护
- 远程控制
服务
- 软件设计与工程服务
- 系统集成
- 培训
关于客户
Omni Mold is a premier ultra-precision mold manufacturer based in Singapore, established in the late 1980s. The company specializes in designing, engineering, and producing sophisticated and finely detailed steel molds for stringent specification industries such as electronics, automotive, telecommunications, and healthcare/medical equipment. Listed on the Singapore Stock Exchange in 1994, Omni Mold has grown to become a leader in its field, serving some of the world's top companies in these industries. The company prides itself on leveraging advanced technologies to produce high-quality molds and has a strong focus on customer satisfaction and innovation.
挑战
After expanding operations to meet ever-increasing customer demands, Omni Mold faced the challenge of working efficiently with a lean headcount. The company needed to compress design cycles and reduce production time to meet customer demands while solving workforce shortages caused by business expansion. Additionally, they aimed to curb the rate of human error and lower manufacturing costs. Omni Mold's management foresaw an upward trend in customer demand for complex three-dimensional (3D) products and shorter turnaround times. To address these challenges, they identified the use of cutting-edge technology as a key business driver and competitive differentiator.
解决方案
Omni Mold implemented Siemens PLM Software technology to maintain fast delivery of ultra-precision molds during a time of business expansion. In 1992, the company selected Unigraphics (now called NX) software for its CAM capabilities and standardized on the CAD/CAM system in 1996 to further improve customer service. Recently, Omni Mold implemented Siemens digital lifecycle management solution, Teamcenter, to widen its competitive edge. Teamcenter provides sophisticated tools for data management and access in a web-native environment, allowing for greater re-use of intellectual capital. The software makes diverse types of product information accessible from a single, intuitive browser interface and provides secure file management and revision control. Management believes that Siemens technology will bring numerous productivity benefits beyond those already achieved with NX, including a reduction in turnaround time and workforce resource savings.
运营影响
数量效益
Case Study missing?
Start adding your own!
Register with your work email and create a new case study profile for your business.
相关案例.

Case Study
Remote Temperature Monitoring of Perishable Goods Saves Money
RMONI was facing temperature monitoring challenges in a cold chain business. A cold chain must be established and maintained to ensure goods have been properly refrigerated during every step of the process, making temperature monitoring a critical business function. Manual registration practice can be very costly, labor intensive and prone to mistakes.
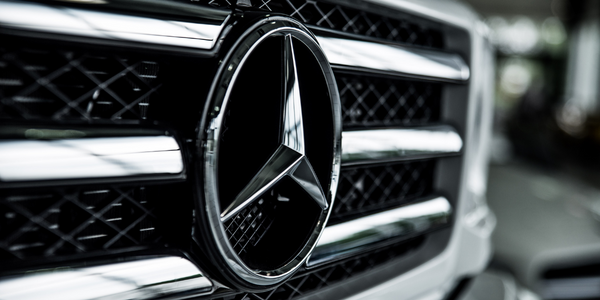
Case Study
Integral Plant Maintenance
Mercedes-Benz and his partner GAZ chose Siemens to be its maintenance partner at a new engine plant in Yaroslavl, Russia. The new plant offers a capacity to manufacture diesel engines for the Russian market, for locally produced Sprinter Classic. In addition to engines for the local market, the Yaroslavl plant will also produce spare parts. Mercedes-Benz Russia and his partner needed a service partner in order to ensure the operation of these lines in a maintenance partnership arrangement. The challenges included coordinating the entire maintenance management operation, in particular inspections, corrective and predictive maintenance activities, and the optimizing spare parts management. Siemens developed a customized maintenance solution that includes all electronic and mechanical maintenance activities (Integral Plant Maintenance).
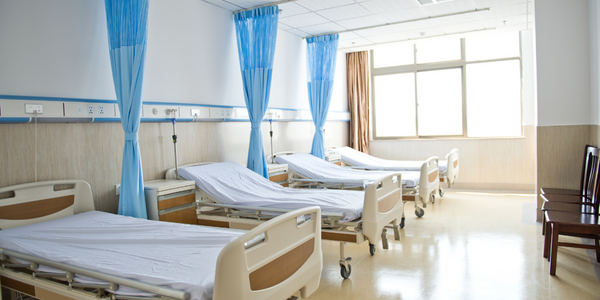
Case Study
Hospital Inventory Management
The hospital supply chain team is responsible for ensuring that the right medical supplies are readily available to clinicians when and where needed, and to do so in the most efficient manner possible. However, many of the systems and processes in use at the cancer center for supply chain management were not best suited to support these goals. Barcoding technology, a commonly used method for inventory management of medical supplies, is labor intensive, time consuming, does not provide real-time visibility into inventory levels and can be prone to error. Consequently, the lack of accurate and real-time visibility into inventory levels across multiple supply rooms in multiple hospital facilities creates additional inefficiency in the system causing over-ordering, hoarding, and wasted supplies. Other sources of waste and cost were also identified as candidates for improvement. Existing systems and processes did not provide adequate security for high-cost inventory within the hospital, which was another driver of cost. A lack of visibility into expiration dates for supplies resulted in supplies being wasted due to past expiry dates. Storage of supplies was also a key consideration given the location of the cancer center’s facilities in a dense urban setting, where space is always at a premium. In order to address the challenges outlined above, the hospital sought a solution that would provide real-time inventory information with high levels of accuracy, reduce the level of manual effort required and enable data driven decision making to ensure that the right supplies were readily available to clinicians in the right location at the right time.