OMEGA ELEVATOR, S.A. - Lifting Elevator Development to New Heights with SOLIDWORKS Solutions
公司规模
Large Corporate
地区
- Europe
国家
- Spain
产品
- SOLIDWORKS
- SOLIDWORKS Simulation
- SOLIDWORKS PDM Professional
- SOLIDWORKS Composer
技术栈
- 3D Design
- Simulation Analysis
- Product Data Management
- Technical Communication Software
实施规模
- Enterprise-wide Deployment
影响指标
- Cost Savings
- Customer Satisfaction
- Innovation Output
- Productivity Improvements
技术
- 分析与建模 - 预测分析
- 应用基础设施与中间件 - 数据交换与集成
- 功能应用 - 产品生命周期管理系统 (PLM)
- 平台即服务 (PaaS) - 应用开发平台
适用行业
- 建筑与基础设施
- 设备与机械
适用功能
- 产品研发
- 质量保证
用例
- 预测性维护
服务
- 软件设计与工程服务
- 系统集成
- 培训
关于客户
OMEGA ELEVATOR, S.A., is a leading European elevator company, designing, manufacturing, installing, maintaining, and servicing hydraulic and electric elevators, and other vertical transport systems. Headquartered in Vitoria, Spain, the company has produced elevators for transporting people, as well as small and large cargo loads, for more than 25 years, and has installations on several continents. With its modern production plant and knowledgeable, experienced employees, OMEGA brings extensive technical expertise to the development of its elevation equipment, including elevators, platforms, escalators, and access ramps. Each prototype OMEGA designs is verified and checked in its own testing and trial tower, and adapted to each particular case and specific local regulations.
挑战
Until 2012, OMEGA utilized 2D tools to support its entire development and manufacturing process, from design concept to production. However, to consistently maximize its capacity to produce 4,000 complete elevators annually, the elevator manufacturer decided to transition to 3D technology to accelerate and streamline elevator design, validation, and production, according to Managing Director Javier Azurmendi. The challenge was to accelerate and streamline elevator design, validation, and production by transitioning from a 2D to a 3D development platform.
解决方案
After evaluating 3D design packages, OMEGA standardized on SOLIDWORKS® solutions, implementing SOLIDWORKS design, SOLIDWORKS Simulation analysis, SOLIDWORKS PDM Professional product data management, and SOLIDWORKS Composer technical communication software. The company chose SOLIDWORKS solutions because of their ease of use, power, and versatility. In addition to using SOLIDWORKS design and SOLIDWORKS Simulation analysis software to develop and validate elevator designs, OMEGA implemented the SOLIDWORKS PDM Professional system to improve collaboration and automate workflows. OMEGA also utilizes SOLIDWORKS Composer technical communication software to reuse 3D design data to quickly create or update technical drawings and associated product documentation.
运营影响
数量效益
Case Study missing?
Start adding your own!
Register with your work email and create a new case study profile for your business.
相关案例.

Case Study
Smart Water Filtration Systems
Before working with Ayla Networks, Ozner was already using cloud connectivity to identify and solve water-filtration system malfunctions as well as to monitor filter cartridges for replacements.But, in June 2015, Ozner executives talked with Ayla about how the company might further improve its water systems with IoT technology. They liked what they heard from Ayla, but the executives needed to be sure that Ayla’s Agile IoT Platform provided the security and reliability Ozner required.

Case Study
IoT enabled Fleet Management with MindSphere
In view of growing competition, Gämmerler had a strong need to remain competitive via process optimization, reliability and gentle handling of printed products, even at highest press speeds. In addition, a digitalization initiative also included developing a key differentiation via data-driven services offers.
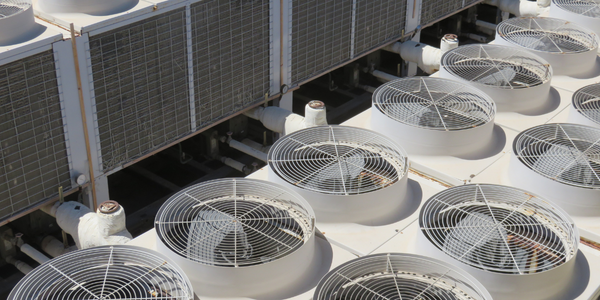
Case Study
Predictive Maintenance for Industrial Chillers
For global leaders in the industrial chiller manufacturing, reliability of the entire production process is of the utmost importance. Chillers are refrigeration systems that produce ice water to provide cooling for a process or industrial application. One of those leaders sought a way to respond to asset performance issues, even before they occur. The intelligence to guarantee maximum reliability of cooling devices is embedded (pre-alarming). A pre-alarming phase means that the cooling device still works, but symptoms may appear, telling manufacturers that a failure is likely to occur in the near future. Chillers who are not internet connected at that moment, provide little insight in this pre-alarming phase.

Case Study
Premium Appliance Producer Innovates with Internet of Everything
Sub-Zero faced the largest product launch in the company’s history:It wanted to launch 60 new products as scheduled while simultaneously opening a new “greenfield” production facility, yet still adhering to stringent quality requirements and manage issues from new supply-chain partners. A the same time, it wanted to increase staff productivity time and collaboration while reducing travel and costs.

Case Study
Integration of PLC with IoT for Bosch Rexroth
The application arises from the need to monitor and anticipate the problems of one or more machines managed by a PLC. These problems, often resulting from the accumulation over time of small discrepancies, require, when they occur, ex post technical operations maintenance.
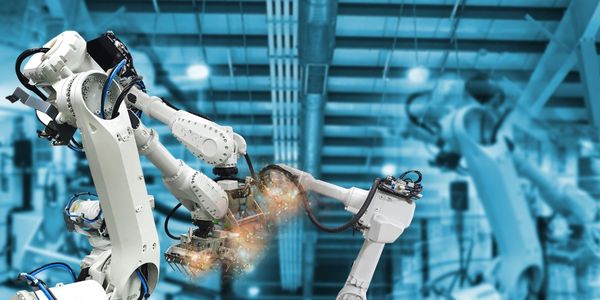
Case Study
Robot Saves Money and Time for US Custom Molding Company
Injection Technology (Itech) is a custom molder for a variety of clients that require precision plastic parts for such products as electric meter covers, dental appliance cases and spools. With 95 employees operating 23 molding machines in a 30,000 square foot plant, Itech wanted to reduce man hours and increase efficiency.