Multi-National Electronics Manufacturer Improves Quality Across Supply Chain
公司规模
Large Corporate
地区
- America
国家
- United States
产品
- GainSeeker
- Hertzler Systems
技术栈
- Integrated Platform
- Centralized Database
实施规模
- Enterprise-wide Deployment
影响指标
- Productivity Improvements
- Customer Satisfaction
- Digital Expertise
技术
- 分析与建模 - 预测分析
- 应用基础设施与中间件 - 数据交换与集成
- 功能应用 - 企业资源规划系统 (ERP)
适用行业
- 电子产品
- 设备与机械
适用功能
- 质量保证
- 商业运营
用例
- 质量预测分析
- 过程控制与优化
- 远程资产管理
服务
- 系统集成
- 软件设计与工程服务
关于客户
The customer is a multi-national electronics company specializing in the production of industrial energy management equipment. This company operates ten plants across North America and has been facing significant challenges in maintaining consistent product quality across its various facilities. Each plant had its own system for tracking defect data, leading to a lack of standardization and visibility. The corporate quality manager, responsible for overseeing quality across all plants, struggled with compiling and analyzing data from disparate sources. This lack of a unified system made it difficult to identify root causes of defects and implement effective solutions, resulting in mounting customer complaints and a sense of powerlessness to ensure product quality.
挑战
Disparate Systems Impact Manufacturing Quality Due to Lack of Visibility Across Silos and a Reliance on Manual Approaches. A corporate quality manager has responsibility for ten plants in North America. Whenever he received a complaint from a customer he would cringe – he felt like he was personally letting his customer and his company down. And he felt powerless to change the situation. Each facility had their own way of tracking defect data, and as the company acquired new plants the problem got worse. At the end of the month, the corporate quality manager received ten reports of the plants’ issues and resolutions, each in its own format. Every month he spent hours and hours compiling data and looking for patterns. It was next to impossible to figure out the root cause of the problem, let alone try to resolve it. “It was difficult for me to understand which plants were doing well… and which plants were not doing well.” Direct Impact on Quality. Disparate systems caused confusion. Customer complaints continued to mount. The corporate quality manager “could not guarantee customers were getting quality products.” The company needed to find a way to improve their quality across the board.
解决方案
Actionable Data Creates Opportunity for Continuous Improvement. The corporate quality manager entrusted Hertzler Systems to provide an integrated platform that combines quality and defect information across multiple plants. The resulting solution provided three advantages: Standardized data collection, Increased timeliness of analytics, Increased visibility at all levels. The Corporate Quality Manager Could Focus on the Analytics. As the company began to use GainSeeker they found that: The plants all collected data in the same system, Defects were accurately captured and logged into a centralized database, The platform provided confidence that the data was accurate. In addition, the standard platform could be adapted to various value streams, collecting defect information with defects appropriate for that product. Shift From Reactive to Proactive Quality Management. It was no longer necessary to wait for the reports to come from the plant. He was empowered to access standardized, integrated quality information in real-time, getting a better sense of what is happening now instead of last month. This enabled the plants to react more quickly, minimizing risks and increasing their autonomy.
运营影响
数量效益
Case Study missing?
Start adding your own!
Register with your work email and create a new case study profile for your business.
相关案例.

Case Study
Smart Water Filtration Systems
Before working with Ayla Networks, Ozner was already using cloud connectivity to identify and solve water-filtration system malfunctions as well as to monitor filter cartridges for replacements.But, in June 2015, Ozner executives talked with Ayla about how the company might further improve its water systems with IoT technology. They liked what they heard from Ayla, but the executives needed to be sure that Ayla’s Agile IoT Platform provided the security and reliability Ozner required.

Case Study
IoT enabled Fleet Management with MindSphere
In view of growing competition, Gämmerler had a strong need to remain competitive via process optimization, reliability and gentle handling of printed products, even at highest press speeds. In addition, a digitalization initiative also included developing a key differentiation via data-driven services offers.

Case Study
Remote Temperature Monitoring of Perishable Goods Saves Money
RMONI was facing temperature monitoring challenges in a cold chain business. A cold chain must be established and maintained to ensure goods have been properly refrigerated during every step of the process, making temperature monitoring a critical business function. Manual registration practice can be very costly, labor intensive and prone to mistakes.
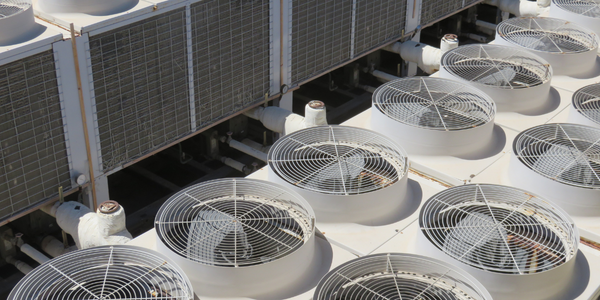
Case Study
Predictive Maintenance for Industrial Chillers
For global leaders in the industrial chiller manufacturing, reliability of the entire production process is of the utmost importance. Chillers are refrigeration systems that produce ice water to provide cooling for a process or industrial application. One of those leaders sought a way to respond to asset performance issues, even before they occur. The intelligence to guarantee maximum reliability of cooling devices is embedded (pre-alarming). A pre-alarming phase means that the cooling device still works, but symptoms may appear, telling manufacturers that a failure is likely to occur in the near future. Chillers who are not internet connected at that moment, provide little insight in this pre-alarming phase.

Case Study
Premium Appliance Producer Innovates with Internet of Everything
Sub-Zero faced the largest product launch in the company’s history:It wanted to launch 60 new products as scheduled while simultaneously opening a new “greenfield” production facility, yet still adhering to stringent quality requirements and manage issues from new supply-chain partners. A the same time, it wanted to increase staff productivity time and collaboration while reducing travel and costs.