公司规模
200-1,000
地区
- America
国家
- United States
产品
- NetSuite
- ShipHawk
技术栈
- ERP
- Shipping Software
实施规模
- Enterprise-wide Deployment
影响指标
- Cost Savings
- Productivity Improvements
技术
- 功能应用 - 企业资源规划系统 (ERP)
- 功能应用 - 仓库管理系统 (WMS)
适用行业
- 零售
适用功能
- 物流运输
- 仓库和库存管理
用例
- 库存管理
- 仓库自动化
服务
- 系统集成
关于客户
Mann Lake is a leading manufacturer and supplier in the beekeeping industry. Founded in 1983 in Hackensack, Minnesota, the company serves both commercial businesses and small-scale hobbyists with the goal of keeping bees flourishing. Mann Lake has also expanded to offer supplies and products for poultry and goat farming. The company currently operates from seven locations in Minnesota, California, Pennsylvania, Texas, Florida, Kentucky, and Oregon. With approximately 12,000 SKUs, Mann Lake's product range varies from one-pound boxes to 60-pound boxes with different dimensions. Some of their shipments qualify as HAZMAT and require special handling, instructions, and labeling.
挑战
Mann Lake, a leader in the beekeeping industry, faced a challenge after switching to NetSuite in 2020. The company needed a shipping solution that could integrate with its new ERP and automate its processes. Mann Lake has approximately 12,000 SKUs, with products ranging from one-pound boxes to 60-pound boxes with varying dimensions. Some shipments also qualified as HAZMAT and required special handling, instructions, and labeling. The company's previous shipping software was unable to automate these processes or integrate with NetSuite and all of its carriers. This led to a bottleneck in the order processing line. Additionally, Mann Lake was manually rate shopping between UPS, USPS, and FedEx, which was time-consuming and increased the likelihood of errors.
解决方案
Mann Lake implemented ShipHawk, a shipping solution that streamlined the fulfillment process and reduced order processing times by 50%. ShipHawk's packing algorithm calculates final packed weights and dimensions for each shipment and delivers packing and shipping rate intelligence in real time. Every order is packed in the optimal carton, automatically considering weight, dimensions, value, fragility, or special handling requirements, including hazardous materials. This solution eliminated the need for employees to spend unnecessary time trying to figure out the best box or cheapest carrier. Mann Lake has implemented ShipHawk’s shipping solution in all seven of its distribution centers.
运营影响
数量效益
Case Study missing?
Start adding your own!
Register with your work email and create a new case study profile for your business.
相关案例.
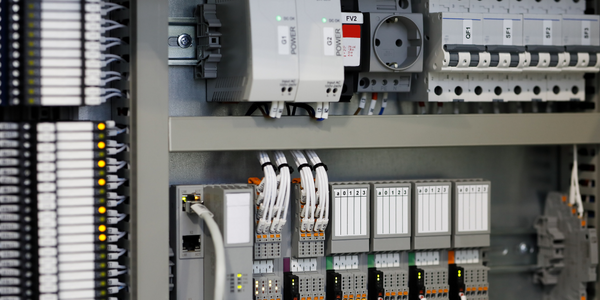
Case Study
Improving Production Line Efficiency with Ethernet Micro RTU Controller
Moxa was asked to provide a connectivity solution for one of the world's leading cosmetics companies. This multinational corporation, with retail presence in 130 countries, 23 global braches, and over 66,000 employees, sought to improve the efficiency of their production process by migrating from manual monitoring to an automatic productivity monitoring system. The production line was being monitored by ABB Real-TPI, a factory information system that offers data collection and analysis to improve plant efficiency. Due to software limitations, the customer needed an OPC server and a corresponding I/O solution to collect data from additional sensor devices for the Real-TPI system. The goal is to enable the factory information system to more thoroughly collect data from every corner of the production line. This will improve its ability to measure Overall Equipment Effectiveness (OEE) and translate into increased production efficiencies. System Requirements • Instant status updates while still consuming minimal bandwidth to relieve strain on limited factory networks • Interoperable with ABB Real-TPI • Small form factor appropriate for deployment where space is scarce • Remote software management and configuration to simplify operations
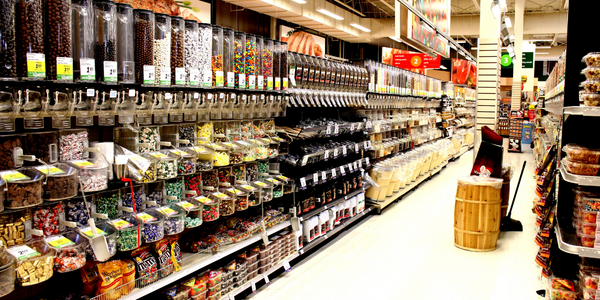
Case Study
How Sirqul’s IoT Platform is Crafting Carrefour’s New In-Store Experiences
Carrefour Taiwan’s goal is to be completely digital by end of 2018. Out-dated manual methods for analysis and assumptions limited Carrefour’s ability to change the customer experience and were void of real-time decision-making capabilities. Rather than relying solely on sales data, assumptions, and disparate systems, Carrefour Taiwan’s CEO led an initiative to find a connected IoT solution that could give the team the ability to make real-time changes and more informed decisions. Prior to implementing, Carrefour struggled to address their conversion rates and did not have the proper insights into the customer decision-making process nor how to make an immediate impact without losing customer confidence.
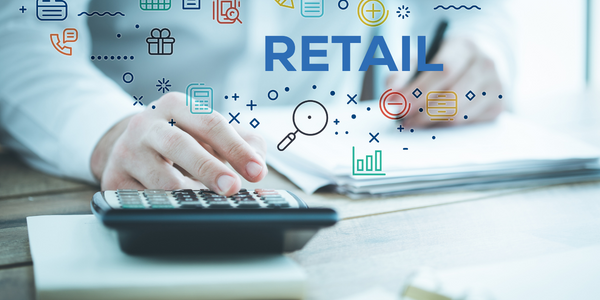
Case Study
Digital Retail Security Solutions
Sennco wanted to help its retail customers increase sales and profits by developing an innovative alarm system as opposed to conventional connected alarms that are permanently tethered to display products. These traditional security systems were cumbersome and intrusive to the customer shopping experience. Additionally, they provided no useful data or analytics.
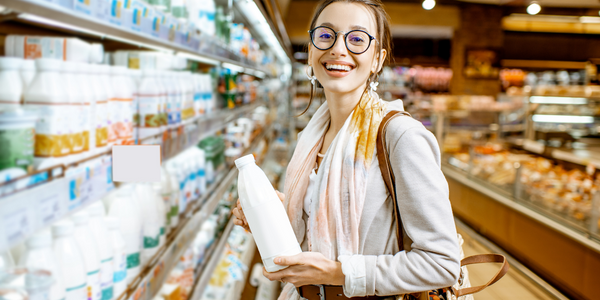
Case Study
Ensures Cold Milk in Your Supermarket
As of 2014, AK-Centralen has over 1,500 Danish supermarkets equipped, and utilizes 16 operators, and is open 24 hours a day, 365 days a year. AK-Centralen needed the ability to monitor the cooling alarms from around the country, 24 hours a day, 365 days a year. Each and every time the door to a milk cooler or a freezer does not close properly, an alarm goes off on a computer screen in a control building in southwestern Odense. This type of alarm will go off approximately 140,000 times per year, equating to roughly 400 alarms in a 24-hour period. Should an alarm go off, then there is only a limited amount of time to act before dairy products or frozen pizza must be disposed of, and this type of waste can quickly start to cost a supermarket a great deal of money.
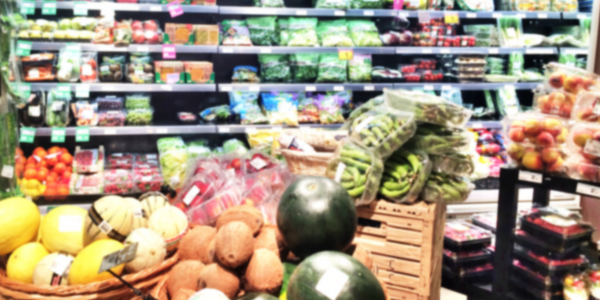
Case Study
Supermarket Energy Savings
The client had previously deployed a one-meter-per-store monitoring program. Given the manner in which energy consumption changes with external temperature, hour of the day, day of week and month of year, a single meter solution lacked the ability to detect the difference between a true problem and a changing store environment. Most importantly, a single meter solution could never identify root cause of energy consumption changes. This approach never reduced the number of truck-rolls or man-hours required to find and resolve issues.