技术
- 传感器 - 触觉传感器
- 传感器 - 扭矩传感器
适用行业
- 航天
- 造纸
适用功能
- 产品研发
- 质量保证
用例
- 数字孪生
- 虚拟现实
服务
- 测试与认证
关于客户
Zodiac Seats France(ZSFR - 现在的 Safran Seats)是一家高档乘客座椅供应商。赛峰座椅凭借世界知名的商务舱专业知识,设计、认证和组装创新、可定制和高附加值的产品。该部门利用强大的国际影响力,为来自所有市场的客户提供专业知识。他们的产品聘请了多个设计师团队,提供最先进的设计,融合了高科技设备,体现了为座椅市场的三个基本挑战寻找解决方案的决心:持续改进乘客座椅舒适度和人体工程学,提供差异化为其航空公司客户提供可定制的产品,并持续进行研究以优化可用的机舱空间。
挑战
Zodiac Seats France(ZSFR - 现在的 Safran Seats)是一家高档乘客座椅供应商,旨在提高飞机座椅的舒适度。我们面临的挑战是开发一种新型飞机座椅,以显着提高乘客的舒适度。飞机座椅的开发涉及人体工程学、机舱布局和生态设计等几个关键因素。 ZSFR 还希望考虑环境问题,并将生态设计和轻量化置于其产品开发计划的首要位置。较轻的座椅有助于减少飞机的燃油消耗,并且座椅主要使用可回收材料生产。该公司主要关心的是优化飞机乘客的舒适度。飞机座椅市场竞争激烈,必须尽快将新的高品质座椅推向市场。为了评估座椅的人体工程学质量,工程师需要一种工具来模拟所有生物力学不适源,例如就座乘客的大腿内侧软组织受压等因素。
解决方案
为了提高飞机乘客的质量和舒适度,Zodiac Seats 使用数值模拟和 Altair HyperWorksTM 套件来设计、评估和优化座椅。这使得 ZSFR 的设计人员能够评估其座椅结构在静态和动态应力下的行为以及热成型和冲压座椅组件的可行性。设计人员依靠 Altair HyperWorks 套件来模拟生物力学因素。软组织压缩是所研究的因素,可以通过应用两个参数来估计:外部接触压力和直接组织应变。为了处理这个问题,模拟工程师创建了两种模型,他们可以用它们来估计每种不适因素。通过采用 Altair 解决方案并结合模拟输出与多种不适因素之间的关系,该工具能够量化人体工程学质量。借助这些结果和见解,工程师能够优化座椅设计和材料,从而减少坐在这些座椅上的乘客的潜在不适。
运营影响
数量效益
Case Study missing?
Start adding your own!
Register with your work email and create a new case study profile for your business.
相关案例.
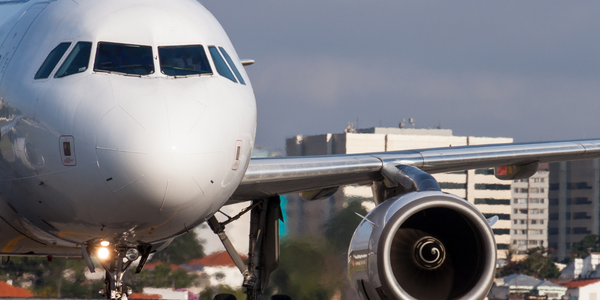
Case Study
Airbus Soars with Wearable Technology
Building an Airbus aircraft involves complex manufacturing processes consisting of thousands of moving parts. Speed and accuracy are critical to business and competitive advantage. Improvements in both would have high impact on Airbus’ bottom line. Airbus wanted to help operators reduce the complexity of assembling cabin seats and decrease the time required to complete this task.
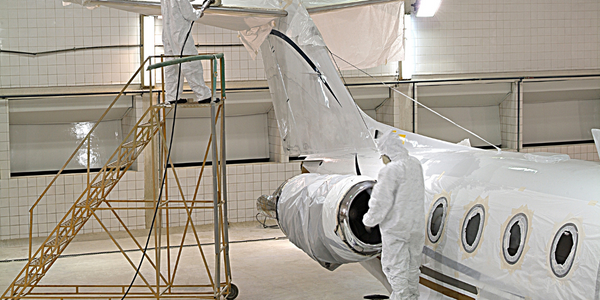
Case Study
Aircraft Predictive Maintenance and Workflow Optimization
First, aircraft manufacturer have trouble monitoring the health of aircraft systems with health prognostics and deliver predictive maintenance insights. Second, aircraft manufacturer wants a solution that can provide an in-context advisory and align job assignments to match technician experience and expertise.
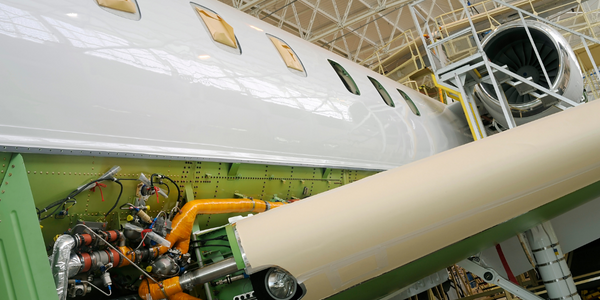
Case Study
Aerospace & Defense Case Study Airbus
For the development of its new wide-body aircraft, Airbus needed to ensure quality and consistency across all internal and external stakeholders. Airbus had many challenges including a very aggressive development schedule and the need to ramp up production quickly to satisfy their delivery commitments. The lack of communication extended design time and introduced errors that drove up costs.
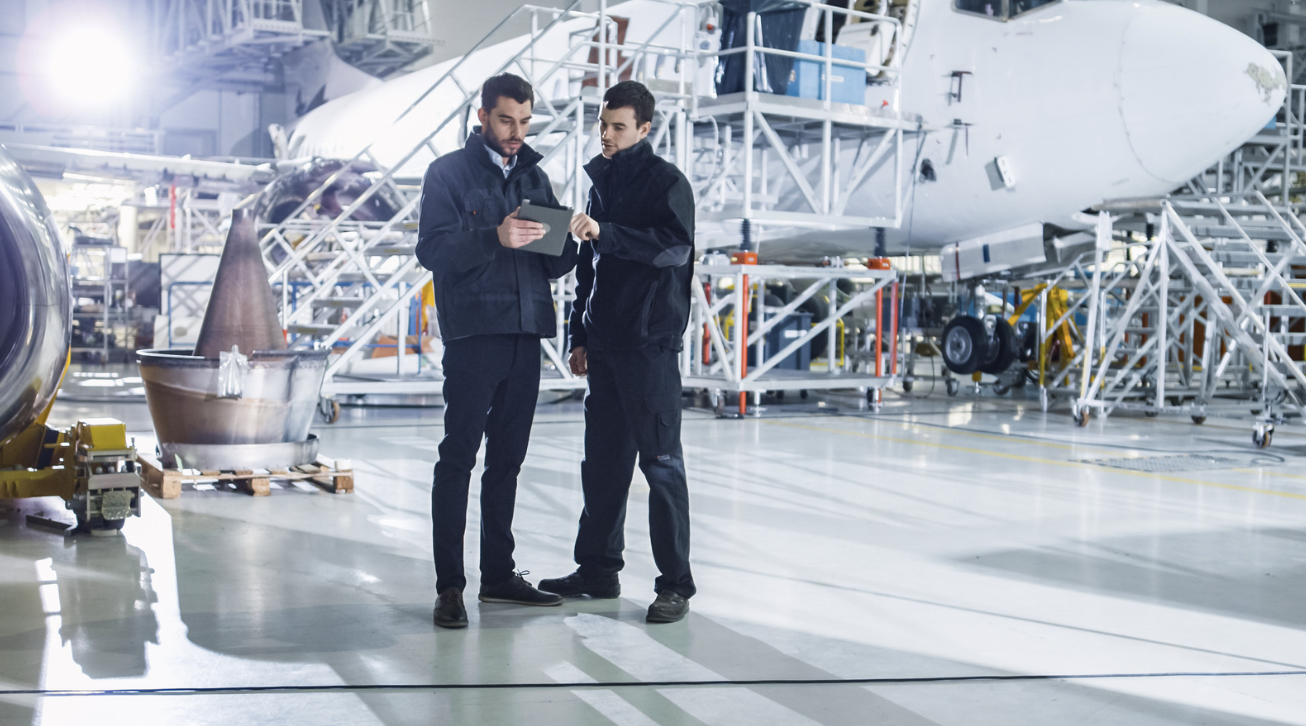
Case Study
Developing Smart Tools for the Airbus Factory
Manufacturing and assembly of aircraft, which involves tens of thousands of steps that must be followed by the operators, and a single mistake in the process could cost hundreds of thousands of dollars to fix, makes the room for error very small.

Case Study
Wireless Improves Efficiency in Compressed Air Systems
Hollingsworth and Vose wanted to improve the efficiency of their compressed air system, lower the electricity expense component of manufacturing cost in their commodity industry, and conserve energy leading to lowered greenhouse gas emissions. Compressed air systems degrade over time and become leaky and inefficient. Hollingsworth and Vose wanted to increase the frequency of system inspections without paying the high cost of manual labor.