公司规模
Mid-size Company
地区
- America
国家
- United States
产品
- Vocollect VoiceLink Enterprise Connector
- Vocollect SR-20 Wired Headsets
- Vocollect SRX Wireless Headsets
- Vocollect T5 Mobile Devices
- Vocollect SRX2 Wireless Headsets
技术栈
- Voice Technology
- RF Network
- Speech Recognition
实施规模
- Enterprise-wide Deployment
影响指标
- Cost Savings
- Customer Satisfaction
- Employee Satisfaction
- Productivity Improvements
技术
- 分析与建模 - 预测分析
- 功能应用 - 远程监控系统
- 功能应用 - 仓库管理系统 (WMS)
适用行业
- 食品与饮料
- 零售
适用功能
- 物流运输
- 仓库和库存管理
用例
- 库存管理
- 预测性维护
- 资产跟踪
- 仓库自动化
服务
- 软件设计与工程服务
- 系统集成
- 培训
关于客户
Jordano’s, Inc. is a family- and employee-owned food service and beverage distribution company based in the United States. Serving approximately 1,700 customers in central and southern California, Jordano’s has a rich 98-year history of commitment to quality and customer service. Originally founded as a grocery chain, the company transitioned to distribution in the 1970s and now boasts annual sales exceeding $142 million. With over 205 employees, Jordano’s operates primarily through its 100,000-square-foot distribution center in Santa Barbara, California, processing upwards of 14,000 SKUs six days a week across three shifts.
挑战
Jordano’s, Inc. faced the challenge of maintaining high order accuracy and customer satisfaction while complying with growing governmental regulations for food safety and traceability. The company’s existing double paper label processes were outdated and needed modernization to handle the increasing complexity of order fulfillment. Director of Operations Dennis Merchant recognized the need to improve accuracy levels in their 100,000-square-foot distribution center in Santa Barbara, California. The company sought a solution that could enhance operational performance and ensure perfect orders to maintain a competitive edge.
解决方案
Jordano’s, Inc. partnered with BFC and Honeywell to implement Vocollect voice solutions to modernize their order fulfillment processes. The deployment began cautiously, starting in the freezer section, then moving to the cooler, and finally to dry goods. The Vocollect voice technology, including the Vocollect VoiceLink Enterprise Connector, SR-20 Wired Headsets, SRX Wireless Headsets, and T5 Mobile Devices, was chosen for its proven results in the grocery and food distribution sectors. The implementation also involved reevaluating the RF network to address any dead spots, ensuring smooth operation. Recently, Jordano’s tested Honeywell’s freezer-certified Vocollect SRX2 wireless headsets, which provided excellent speech recognition quality, lighter weight, and easier maneuverability in the freezer section. The ability to share headsets across shifts reduced the number of batteries needed, resulting in significant cost savings. Employees appreciated the improved process and enjoyed working with the new technology.
运营影响
数量效益
Case Study missing?
Start adding your own!
Register with your work email and create a new case study profile for your business.
相关案例.

Case Study
The Kellogg Company
Kellogg keeps a close eye on its trade spend, analyzing large volumes of data and running complex simulations to predict which promotional activities will be the most effective. Kellogg needed to decrease the trade spend but its traditional relational database on premises could not keep up with the pace of demand.

Case Study
HEINEKEN Uses the Cloud to Reach 10.5 Million Consumers
For 2012 campaign, the Bond promotion, it planned to launch the campaign at the same time everywhere on the planet. That created unprecedented challenges for HEINEKEN—nowhere more so than in its technology operation. The primary digital content for the campaign was a 100-megabyte movie that had to play flawlessly for millions of viewers worldwide. After all, Bond never fails. No one was going to tolerate a technology failure that might bruise his brand.Previously, HEINEKEN had supported digital media at its outsourced datacenter. But that datacenter lacked the computing resources HEINEKEN needed, and building them—especially to support peak traffic that would total millions of simultaneous hits—would have been both time-consuming and expensive. Nor would it have provided the geographic reach that HEINEKEN needed to minimize latency worldwide.
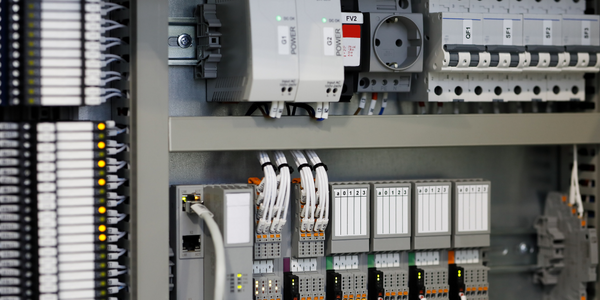
Case Study
Improving Production Line Efficiency with Ethernet Micro RTU Controller
Moxa was asked to provide a connectivity solution for one of the world's leading cosmetics companies. This multinational corporation, with retail presence in 130 countries, 23 global braches, and over 66,000 employees, sought to improve the efficiency of their production process by migrating from manual monitoring to an automatic productivity monitoring system. The production line was being monitored by ABB Real-TPI, a factory information system that offers data collection and analysis to improve plant efficiency. Due to software limitations, the customer needed an OPC server and a corresponding I/O solution to collect data from additional sensor devices for the Real-TPI system. The goal is to enable the factory information system to more thoroughly collect data from every corner of the production line. This will improve its ability to measure Overall Equipment Effectiveness (OEE) and translate into increased production efficiencies. System Requirements • Instant status updates while still consuming minimal bandwidth to relieve strain on limited factory networks • Interoperable with ABB Real-TPI • Small form factor appropriate for deployment where space is scarce • Remote software management and configuration to simplify operations

Case Study
Energy Management System at Sugar Industry
The company wanted to use the information from the system to claim under the renewable energy certificate scheme. The benefit to the company under the renewable energy certificates is Rs 75 million a year. To enable the above, an end-to-end solution for load monitoring, consumption monitoring, online data monitoring, automatic meter data acquisition which can be exported to SAP and other applications is required.
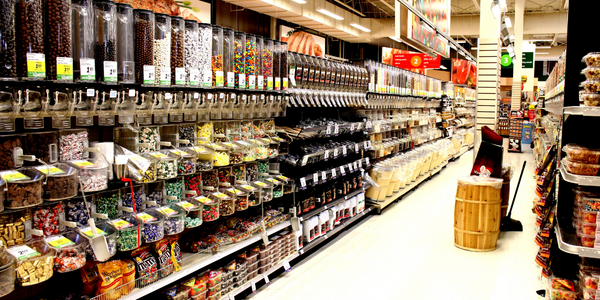
Case Study
How Sirqul’s IoT Platform is Crafting Carrefour’s New In-Store Experiences
Carrefour Taiwan’s goal is to be completely digital by end of 2018. Out-dated manual methods for analysis and assumptions limited Carrefour’s ability to change the customer experience and were void of real-time decision-making capabilities. Rather than relying solely on sales data, assumptions, and disparate systems, Carrefour Taiwan’s CEO led an initiative to find a connected IoT solution that could give the team the ability to make real-time changes and more informed decisions. Prior to implementing, Carrefour struggled to address their conversion rates and did not have the proper insights into the customer decision-making process nor how to make an immediate impact without losing customer confidence.