Hamburg Süd Heightens Customer Service by Minding the Data Gap
公司规模
1,000+
国家
- Germany
产品
- e2open Bookings
- e2open Logistics suite
技术栈
- SaaS
- Cloud-native platform
- Data visualization
实施规模
- Enterprise-wide Deployment
影响指标
- Cost Savings
- Customer Satisfaction
- Productivity Improvements
技术
- 分析与建模 - 预测分析
- 应用基础设施与中间件 - 数据可视化
- 功能应用 - 远程监控系统
适用功能
- 商业运营
- 物流运输
用例
- 车队管理
- 预测性维护
- 资产跟踪
服务
- 数据科学服务
- 软件设计与工程服务
- 系统集成
关于客户
Hamburg Süd is a container shipping company with a history spanning 150 years. Now part of Maersk, it operates as an independent entity with 250 offices in over 100 countries. The company offers custom-tailored logistics solutions to shippers, freight forwarders, and non-vessel-operating common carriers (NVOCCs). With approximately 700 vessels, 3.6 million units, and 400 ports served by the Maersk Group, Hamburg Süd provides access to the world’s largest vessel and container fleet. The company is known for its quality, reliability, and flexibility, and it is one of the many ocean carriers in e2open’s ocean carrier network.
挑战
Ocean carriers like Hamburg Süd need to provide timely in-transit status updates to their customers. These updates are often part of service-level agreements and are critical for minimizing delays, reducing costs, and maintaining smooth supply chain operations. However, the data required for these updates often comes from various parties, making it challenging to provide accurate and timely information. Previously, Hamburg Süd received monthly data-quality reports in PDF format, which only provided aggregated service level statistics and did not offer detailed insights into regional and local challenges. This limited the carrier's ability to improve operational efficiencies and service levels.
解决方案
Hamburg Süd collaborated with e2open to develop new analytics capabilities within the e2open Bookings platform. This included creating interactive visual dashboards that aggregate shipment event data, allowing Hamburg Süd to view its performance across all lanes and regions. The dashboards offer customizable views, enabling granular-level analysis of port activities and customer-specific needs. E2open's product management and development teams worked closely with Hamburg Süd to create dynamic, customized views for container shipments in-transit. These dashboards provide a comprehensive overview of shipment performance, reliability, and container status event reporting completeness. The new capabilities also include a measurement for submission timeliness, helping Hamburg Süd ensure timely updates to customers.
运营影响
数量效益
Case Study missing?
Start adding your own!
Register with your work email and create a new case study profile for your business.
相关案例.

Case Study
Remote Monitoring & Predictive Maintenance App for a Solar Energy System
The maintenance & tracking of various modules was an overhead for the customer due to the huge labor costs involved. Being an advanced solar solutions provider, they wanted to ensure early detection of issues and provide the best-in-class customer experience. Hence they wanted to automate the whole process.
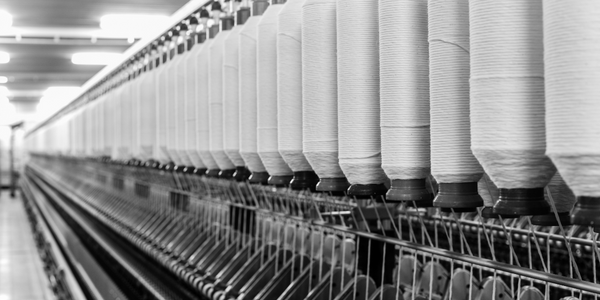
Case Study
IoT Applications and Upgrades in Textile Plant
At any given time, the textile company’s manufacturing facility has up to 2,000 textile carts in use. These carts are pushed from room to room, carrying materials or semi-finished products. Previously, a paper with a hand-written description was attached to each cart. This traditional method of processing made product tracking extremely difficult. Additionally, making sure that every cart of materials or semi-finished products went to its correct processing work station was also a problem. Therefore, the company desired an intelligent solution for tracking assets at their factories. They also wanted a solution that would help them collect process data so they could improve their manufacturing efficiency.
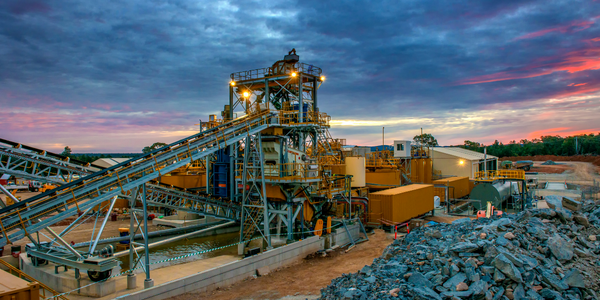
Case Study
Goldcorp: Internet of Things Enables the Mine of the Future
Goldcorp is committed to responsible mining practices and maintaining maximum safety for its workers. At the same time, the firm is constantly exploring ways to improve the efficiency of its operations, extend the life of its assets, and control costs. Goldcorp needed technology that can maximize production efficiency by tracking all mining operations, keep employees safe with remote operations and monitoring of hazardous work areas and control production costs through better asset and site management.
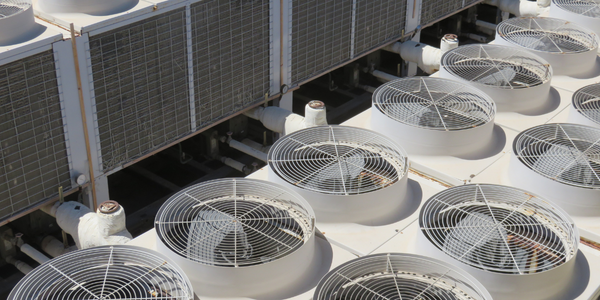
Case Study
Predictive Maintenance for Industrial Chillers
For global leaders in the industrial chiller manufacturing, reliability of the entire production process is of the utmost importance. Chillers are refrigeration systems that produce ice water to provide cooling for a process or industrial application. One of those leaders sought a way to respond to asset performance issues, even before they occur. The intelligence to guarantee maximum reliability of cooling devices is embedded (pre-alarming). A pre-alarming phase means that the cooling device still works, but symptoms may appear, telling manufacturers that a failure is likely to occur in the near future. Chillers who are not internet connected at that moment, provide little insight in this pre-alarming phase.
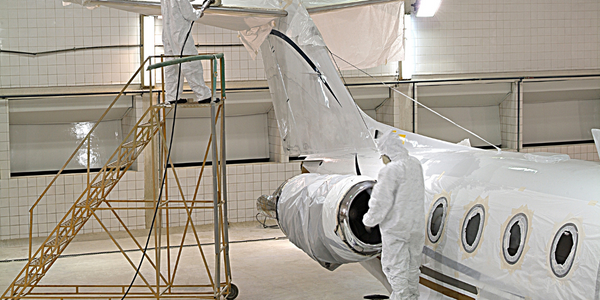
Case Study
Aircraft Predictive Maintenance and Workflow Optimization
First, aircraft manufacturer have trouble monitoring the health of aircraft systems with health prognostics and deliver predictive maintenance insights. Second, aircraft manufacturer wants a solution that can provide an in-context advisory and align job assignments to match technician experience and expertise.
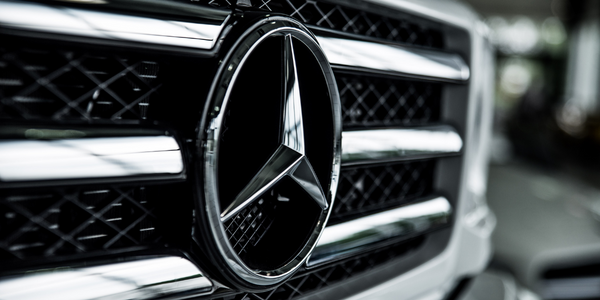
Case Study
Integral Plant Maintenance
Mercedes-Benz and his partner GAZ chose Siemens to be its maintenance partner at a new engine plant in Yaroslavl, Russia. The new plant offers a capacity to manufacture diesel engines for the Russian market, for locally produced Sprinter Classic. In addition to engines for the local market, the Yaroslavl plant will also produce spare parts. Mercedes-Benz Russia and his partner needed a service partner in order to ensure the operation of these lines in a maintenance partnership arrangement. The challenges included coordinating the entire maintenance management operation, in particular inspections, corrective and predictive maintenance activities, and the optimizing spare parts management. Siemens developed a customized maintenance solution that includes all electronic and mechanical maintenance activities (Integral Plant Maintenance).