H&O Distribution picks and packs profits with new supply chain solutions
公司规模
11-200
地区
- America
国家
- United States
产品
- Manhattan SCALE™
技术栈
- PC-based entries
- Unix-based system
实施规模
- Enterprise-wide Deployment
影响指标
- Cost Savings
- Customer Satisfaction
- Employee Satisfaction
- Productivity Improvements
技术
- 功能应用 - 企业资源规划系统 (ERP)
- 功能应用 - 仓库管理系统 (WMS)
适用功能
- 商业运营
- 仓库和库存管理
用例
- 库存管理
- 供应链可见性(SCV)
- 仓库自动化
服务
- 系统集成
- 培训
关于客户
H & O Distribution, along with its affiliate companies Osborne Trucking and Osborne Logistics, offers comprehensive warehousing, fulfillment, and shipping solutions to a diverse range of clients globally. Established in 1959, this family-owned business is located on 36 acres in Fairfield, Ohio, near Cincinnati. The company employs around 85 people, serves over 100 customers, and operates 525,000 square feet of warehouse space. The family-oriented nature of the business has been a key factor in its success, attracting both employees and customers. As a third-party public warehouse, H & O provides a variety of services, including repacking, crating, and general pallet storage, making it a one-stop shop for customers' logistical needs. Despite its success, the company faced challenges with outdated manual processes that impacted its efficiency and profitability.
挑战
H & O Distribution faced significant challenges with its manual processes for tracking inventory, distribution, and shipping. The company relied on a 'pen and paper' method, where forklift operators used clipboards to manage picking and receiving operations. This data was then handed over to clerical staff who entered it into an outdated Unix-based system. This manual process led to numerous data entry errors, extensive man-hours to maintain accuracy, and ultimately, revenue losses. Additionally, H & O lacked value-added services to offer its customers, which hindered its ability to attract new clients and maintain a competitive edge. The company needed to modernize its operations to improve efficiency, reduce errors, and provide better services to its customers.
解决方案
H & O Distribution selected Manhattan SCALE: Supply Chain Architected for Logistics Execution and Extended Enterprise Management to modernize its operations. The decision was based on Manhattan Associates' strong industry reputation and the built-in capabilities and configurability of their solutions. The implementation process was smooth, with Manhattan's professional services team delivering an easily configurable system that met all go-live dates without disrupting daily operations. The transition required minimal training, and the entire process was completed under budget. The new system replaced the outdated Unix-based system and manual processes, significantly improving efficiency and accuracy. Forklift operators now input inventory data on mounted computers, achieving nearly 100% accuracy and saving approximately $20,000 annually in shipping errors. The advanced features of Manhattan SCALE allowed H & O to streamline its business processes, enhance inventory tracking, and provide value-added services to its customers.
运营影响
数量效益
Case Study missing?
Start adding your own!
Register with your work email and create a new case study profile for your business.
相关案例.

Case Study
Remote Temperature Monitoring of Perishable Goods Saves Money
RMONI was facing temperature monitoring challenges in a cold chain business. A cold chain must be established and maintained to ensure goods have been properly refrigerated during every step of the process, making temperature monitoring a critical business function. Manual registration practice can be very costly, labor intensive and prone to mistakes.
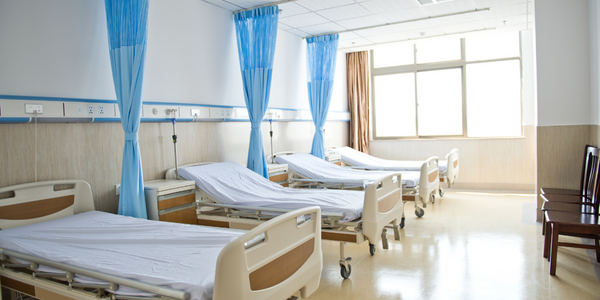
Case Study
Hospital Inventory Management
The hospital supply chain team is responsible for ensuring that the right medical supplies are readily available to clinicians when and where needed, and to do so in the most efficient manner possible. However, many of the systems and processes in use at the cancer center for supply chain management were not best suited to support these goals. Barcoding technology, a commonly used method for inventory management of medical supplies, is labor intensive, time consuming, does not provide real-time visibility into inventory levels and can be prone to error. Consequently, the lack of accurate and real-time visibility into inventory levels across multiple supply rooms in multiple hospital facilities creates additional inefficiency in the system causing over-ordering, hoarding, and wasted supplies. Other sources of waste and cost were also identified as candidates for improvement. Existing systems and processes did not provide adequate security for high-cost inventory within the hospital, which was another driver of cost. A lack of visibility into expiration dates for supplies resulted in supplies being wasted due to past expiry dates. Storage of supplies was also a key consideration given the location of the cancer center’s facilities in a dense urban setting, where space is always at a premium. In order to address the challenges outlined above, the hospital sought a solution that would provide real-time inventory information with high levels of accuracy, reduce the level of manual effort required and enable data driven decision making to ensure that the right supplies were readily available to clinicians in the right location at the right time.
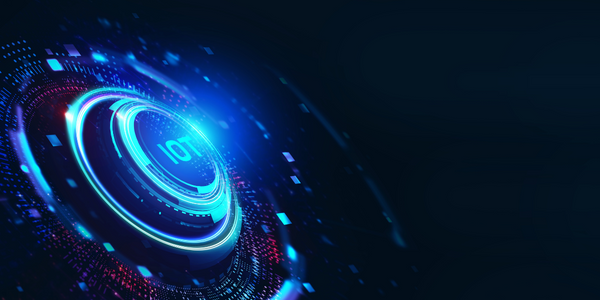
Case Study
IoT Solution for Cold Chain
Most of the customer's warehouses run on utility and generator power. Since these warehouses are in remote locations, power outages are a very common scenario. Diesel fuel, thereby, becomes a significant cost for these warehouses. Energy consumption was also very high due to the lack of a consistent temperature throughout the facility. This lack of a consistent temperature in all areas and no way to control it, resulted in the customer losing a significant amount of their temperature sensitive goods due to spoilage.