Global Crossdock Expansion Solution Creates a Competitive Advantage
公司规模
Large Corporate
地区
- Asia
- America
国家
- China
- United States
产品
- Crossdock Solution
- Virtual Stocking Location
技术栈
- Supply Chain Management Software
- Warehouse Management System
实施规模
- Enterprise-wide Deployment
影响指标
- Cost Savings
- Productivity Improvements
- Customer Satisfaction
技术
- 功能应用 - 仓库管理系统 (WMS)
适用行业
- 消费品
- 零售
适用功能
- 物流运输
- 仓库和库存管理
用例
- 供应链可见性(SCV)
- 库存管理
- 仓库自动化
服务
- 系统集成
- 软件设计与工程服务
关于客户
Energizer Holdings is a dynamic company that offers 30 global brands to consumers in 160 countries around the world. Beyond just batteries, Energizer Holdings offers several other commodities — from household products to infant and feminine care items, even skin, sun, and shaving goods — to make their customers’ and consumers’ lives better.
挑战
After the acquisition of several businesses, Energizer Holdings experienced swift growth across the globe. As the company expanded, it was common for individual products to have a unique ordering and transportation process when shipping from Asia to the United States. As new companies and their procedures were integrated, two primary processes evolved — one for household goods and another for personal care products. Historically, shipments of Energizer household products from China were sent to one warehouse in Memphis, TN. From there, orders were broken down and shipped via full truckload to distribution centers (DCs) throughout the United States. Personal care products were ordered from vendors in Southern China. Depending on the order size, single SKU loads were shipped in full 40’ containers, less than container loads (LCL), or 20’ containers. Once in the United States, products were transported to one of four DCs to be combined with other items for transportation to retailers around the country. The separate transportation arrangements of household and personal care items resulted in missed opportunities to optimize freight. There were frequent situations where multiple 20’ containers or LCL shipments were in transit at the same time. These types of circumstances resulted in additional costs, obscured total landed costs, diminished efficiency of container utilization, and unnecessarily long transit times. According to Josh Wright, senior manager of international warehousing and transportation at Energizer Holdings, “We needed a more holistic transportation strategy. Our company had expanded and with that expansion came opportunities to move goods more efficiently.” Energizer Holdings recognized the growth of the company as an opportunity to improve their global supply chain.
解决方案
Energizer Holdings developed a crossdock solution in Shenzhen, China, for one family of products. Through the crossdock, products from multiple vendors are consolidated at a warehouse in Shenzhen. The goods are then sent directly to a regional DC in the United States rather than a sorting warehouse. By eliminating the need for an additional warehouse, Energizer Holdings saw many benefits from the new process, including reduced domestic transportation needs and costs, faster speed to market, and greater control over order and shipment distribution. Thanks to the success of the crossdock, Energizer Holdings started plans to expand the process for the remaining products shipped from Asia to the United States. They anticipated this expansion would help consolidate activities and cut redundancies in order to drive financial savings. This led to a search for answers from an external company whose expertise could build a customized solution that would scale with future growth goals. Multiple companies submitted bids to oversee the project, including C.H. Robinson. Energizer Holdings already had a strong relationship with C.H. Robinson as a freight forwarder for their business, which ultimately influenced their choice for the crossdock expansion. According to Dwayne Baldwin, supply chain leader at Energizer Holdings, “C.H. Robinson delivered a competitive bid, but we also considered their quality customer service and flexibility in working out viable solutions in our decision process.” C.H. Robinson’s global forwarding team in Cleveland, OH, approached the ongoing challenges Energizer Holdings faced with a fresh perspective — one that could see the big picture. Through numerous cost scenarios and by working closely with the team from Energizer Holdings, a plan swiftly took shape. It became clear that Energizer Holdings required more than just an expansion of the crossdock. Thus, the crossdocking facility in Shenzhen, China, also became a virtual stocking location. As a virtual stocking location, the facility appears within Energizer Holdings’ ordering system as a warehouse that can fulfill orders. In addition to consolidating multiple SKUs into full container loads for shipment to the United States, the location also acts as a DC for orders in the Asia Pacific region — eliminating unnecessary international transportation costs.
运营影响
数量效益
Case Study missing?
Start adding your own!
Register with your work email and create a new case study profile for your business.
相关案例.
.png)
Case Study
Improving Vending Machine Profitability with the Internet of Things (IoT)
The vending industry is undergoing a sea change, taking advantage of new technologies to go beyond just delivering snacks to creating a new retail location. Intelligent vending machines can be found in many public locations as well as company facilities, selling different types of goods and services, including even computer accessories, gold bars, tickets, and office supplies. With increasing sophistication, they may also provide time- and location-based data pertaining to sales, inventory, and customer preferences. But at the end of the day, vending machine operators know greater profitability is driven by higher sales and lower operating costs.
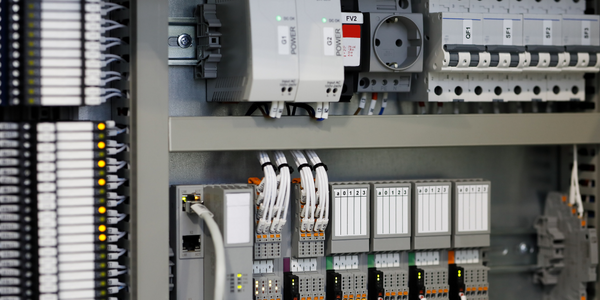
Case Study
Improving Production Line Efficiency with Ethernet Micro RTU Controller
Moxa was asked to provide a connectivity solution for one of the world's leading cosmetics companies. This multinational corporation, with retail presence in 130 countries, 23 global braches, and over 66,000 employees, sought to improve the efficiency of their production process by migrating from manual monitoring to an automatic productivity monitoring system. The production line was being monitored by ABB Real-TPI, a factory information system that offers data collection and analysis to improve plant efficiency. Due to software limitations, the customer needed an OPC server and a corresponding I/O solution to collect data from additional sensor devices for the Real-TPI system. The goal is to enable the factory information system to more thoroughly collect data from every corner of the production line. This will improve its ability to measure Overall Equipment Effectiveness (OEE) and translate into increased production efficiencies. System Requirements • Instant status updates while still consuming minimal bandwidth to relieve strain on limited factory networks • Interoperable with ABB Real-TPI • Small form factor appropriate for deployment where space is scarce • Remote software management and configuration to simplify operations
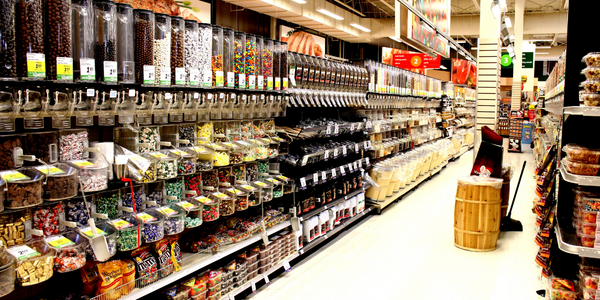
Case Study
How Sirqul’s IoT Platform is Crafting Carrefour’s New In-Store Experiences
Carrefour Taiwan’s goal is to be completely digital by end of 2018. Out-dated manual methods for analysis and assumptions limited Carrefour’s ability to change the customer experience and were void of real-time decision-making capabilities. Rather than relying solely on sales data, assumptions, and disparate systems, Carrefour Taiwan’s CEO led an initiative to find a connected IoT solution that could give the team the ability to make real-time changes and more informed decisions. Prior to implementing, Carrefour struggled to address their conversion rates and did not have the proper insights into the customer decision-making process nor how to make an immediate impact without losing customer confidence.
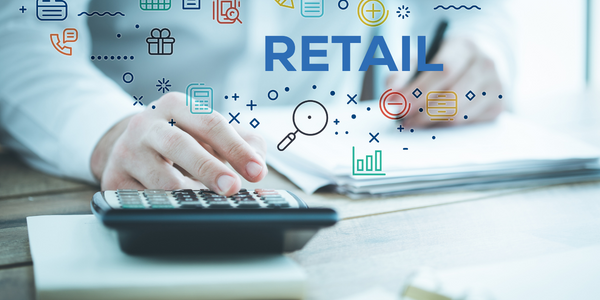
Case Study
Digital Retail Security Solutions
Sennco wanted to help its retail customers increase sales and profits by developing an innovative alarm system as opposed to conventional connected alarms that are permanently tethered to display products. These traditional security systems were cumbersome and intrusive to the customer shopping experience. Additionally, they provided no useful data or analytics.