GENCO Warehouse Experiment Delivers Peak Performance
公司规模
Large Corporate
地区
- America
国家
- United States
产品
- iWAREHOUSE
- Easy Metrics LMS
- Raymond Lift Trucks
技术栈
- Labor Management System (LMS)
- Warehouse Optimization System
实施规模
- Departmental Deployment
影响指标
- Cost Savings
- Productivity Improvements
- Customer Satisfaction
技术
- 功能应用 - 仓库管理系统 (WMS)
- 功能应用 - 车队管理系统 (FMS)
适用功能
- 仓库和库存管理
- 物流运输
用例
- 仓库自动化
- 车队管理
- 预测性维护
服务
- 系统集成
- 软件设计与工程服务
关于客户
Since its inception in 1898, GENCO has established itself as a leading third-party logistics (3PL) provider in the supply chain management industry. Today, GENCO is recognized as a Global Top 25 3PL. They have acquired a variety of customers and manage 38 million square feet of warehouse space across 130 locations. GENCO’s success can be attributed to its dedication to efficient execution, innovative technology, and continuous process improvements.
挑战
GENCO, a leading third-party logistics (3PL) provider, aimed to evaluate and improve the labor efficiency of its lift truck operators and warehouse management processes. The company faced challenges in visibility from both labor management and operational standpoints, which led to inefficiencies in budget and performance accountability. Equipment usage, time traveled, number of impacts, and utilization rates were not being accurately tracked, adding to the lack of accountability for lift truck operators.
解决方案
GENCO partnered with labor management system (LMS) provider Easy Metrics and lift truck provider The Raymond Corporation to develop a plan for merging their programs within its warehouse operations. The Easy Metrics LMS focuses on employee activity in relation to performance goals, while the iWAREHOUSE system from Raymond collects and reports key metrics related to lift trucks and operators. The combined systems provided a comprehensive view of operations from both equipment and labor management standpoints. The iWAREHOUSE system also ensured that only authorized personnel operated the lift trucks and that OSHA-mandated checklists were completed prior to operation.
运营影响
数量效益
Case Study missing?
Start adding your own!
Register with your work email and create a new case study profile for your business.
相关案例.

Case Study
Remote Monitoring & Predictive Maintenance App for a Solar Energy System
The maintenance & tracking of various modules was an overhead for the customer due to the huge labor costs involved. Being an advanced solar solutions provider, they wanted to ensure early detection of issues and provide the best-in-class customer experience. Hence they wanted to automate the whole process.
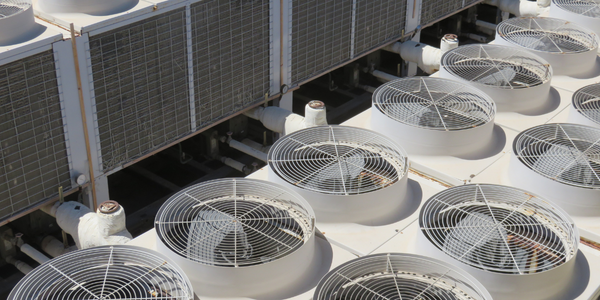
Case Study
Predictive Maintenance for Industrial Chillers
For global leaders in the industrial chiller manufacturing, reliability of the entire production process is of the utmost importance. Chillers are refrigeration systems that produce ice water to provide cooling for a process or industrial application. One of those leaders sought a way to respond to asset performance issues, even before they occur. The intelligence to guarantee maximum reliability of cooling devices is embedded (pre-alarming). A pre-alarming phase means that the cooling device still works, but symptoms may appear, telling manufacturers that a failure is likely to occur in the near future. Chillers who are not internet connected at that moment, provide little insight in this pre-alarming phase.
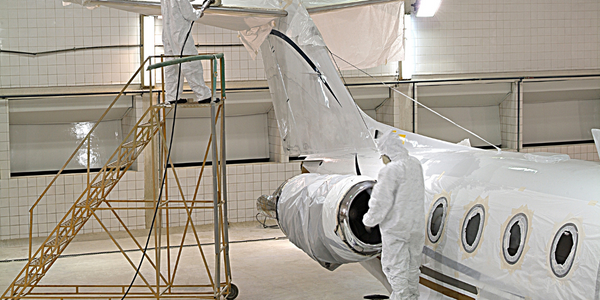
Case Study
Aircraft Predictive Maintenance and Workflow Optimization
First, aircraft manufacturer have trouble monitoring the health of aircraft systems with health prognostics and deliver predictive maintenance insights. Second, aircraft manufacturer wants a solution that can provide an in-context advisory and align job assignments to match technician experience and expertise.
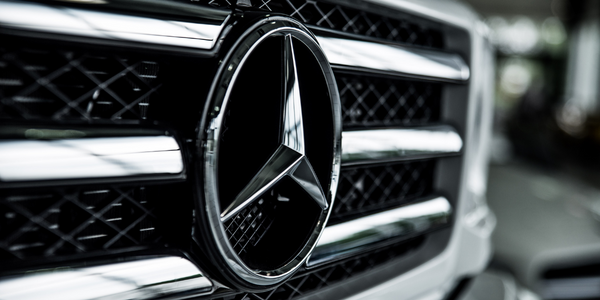
Case Study
Integral Plant Maintenance
Mercedes-Benz and his partner GAZ chose Siemens to be its maintenance partner at a new engine plant in Yaroslavl, Russia. The new plant offers a capacity to manufacture diesel engines for the Russian market, for locally produced Sprinter Classic. In addition to engines for the local market, the Yaroslavl plant will also produce spare parts. Mercedes-Benz Russia and his partner needed a service partner in order to ensure the operation of these lines in a maintenance partnership arrangement. The challenges included coordinating the entire maintenance management operation, in particular inspections, corrective and predictive maintenance activities, and the optimizing spare parts management. Siemens developed a customized maintenance solution that includes all electronic and mechanical maintenance activities (Integral Plant Maintenance).
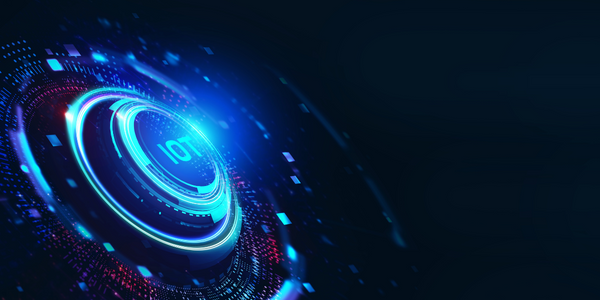
Case Study
IoT Solution for Cold Chain
Most of the customer's warehouses run on utility and generator power. Since these warehouses are in remote locations, power outages are a very common scenario. Diesel fuel, thereby, becomes a significant cost for these warehouses. Energy consumption was also very high due to the lack of a consistent temperature throughout the facility. This lack of a consistent temperature in all areas and no way to control it, resulted in the customer losing a significant amount of their temperature sensitive goods due to spoilage.