公司规模
Large Corporate
地区
- Europe
国家
- Norway
产品
- VersalisFurniture
技术栈
- Automation
- Lean Manufacturing
- Predictive Maintenance
实施规模
- Enterprise-wide Deployment
影响指标
- Cost Savings
- Productivity Improvements
- Customer Satisfaction
技术
- 分析与建模 - 预测分析
- 自动化与控制 - 自动化与过程控制系统
- 功能应用 - 制造执行系统 (MES)
适用功能
- 质量保证
用例
- 自动化制造系统
- 预测性维护
- 过程控制与优化
服务
- 系统集成
- 测试与认证
- 培训
关于客户
Ekornes is a renowned furniture manufacturer based in Norway, known for its high-quality 'Stressless' chairs. The company operates a production plant in Sykkylven, utilizing around 2200 hides per day in 56 colors to produce 2000 seating units, including 1200 'Stressless' chairs. The plant's high level of automation allows it to produce between 100 and 120 chairs every hour. Despite its long history since 1934, Ekornes faces challenges due to high wages and a shortage of skilled labor, driven by the oil industry's impact on Norway's economy. To maintain its competitiveness and keep production in Norway, Ekornes is focusing on creating synergies between skilled workers and advanced technology.
挑战
For Ekornes, the scarcity of skilled workers and high labor costs mean other ways have to be found to reduce costs and enable the company to remain competitive and keep manufacturing in Norway.
解决方案
Lectra proposed an integrated solution including VersalisFurniture, specifically designed to address the challenges of the upholstered leather furniture industry. The solution includes a customized approach delivered by a team of experienced consultants, trainers, and technical experts. Ekornes benefits from a service contract that allows Lectra’s experts to monitor each VersalisFurniture system in real-time, using onboard intelligence to anticipate possible breakdowns and minimize the need for on-site intervention. This ensures maximum uptime and efficiency, especially important for Ekornes' remote production facilities. The introduction of VersalisFurniture also provided an opportunity to review and optimize the entire production process, allowing Ekornes to mix models on the same hide and reduce hide wastage by 5-6%. The intuitive interface and automatic nesting features further enhance productivity and efficiency.
运营影响
数量效益
Case Study missing?
Start adding your own!
Register with your work email and create a new case study profile for your business.
相关案例.

Case Study
Remote Monitoring & Predictive Maintenance App for a Solar Energy System
The maintenance & tracking of various modules was an overhead for the customer due to the huge labor costs involved. Being an advanced solar solutions provider, they wanted to ensure early detection of issues and provide the best-in-class customer experience. Hence they wanted to automate the whole process.
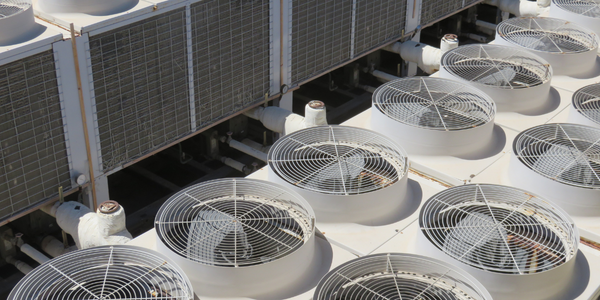
Case Study
Predictive Maintenance for Industrial Chillers
For global leaders in the industrial chiller manufacturing, reliability of the entire production process is of the utmost importance. Chillers are refrigeration systems that produce ice water to provide cooling for a process or industrial application. One of those leaders sought a way to respond to asset performance issues, even before they occur. The intelligence to guarantee maximum reliability of cooling devices is embedded (pre-alarming). A pre-alarming phase means that the cooling device still works, but symptoms may appear, telling manufacturers that a failure is likely to occur in the near future. Chillers who are not internet connected at that moment, provide little insight in this pre-alarming phase.

Case Study
System 800xA at Indian Cement Plants
Chettinad Cement recognized that further efficiencies could be achieved in its cement manufacturing process. It looked to investing in comprehensive operational and control technologies to manage and derive productivity and energy efficiency gains from the assets on Line 2, their second plant in India.

Case Study
Plastic Spoons Case study: Injection Moulding
In order to meet customer expectations by supplying a wide variety of packaging units, from 36 to 1000 spoons per package, a new production and packaging line needed to be built. DeSter wanted to achieve higher production capacity, lower cycle time and a high degree of operator friendliness with this new production line.
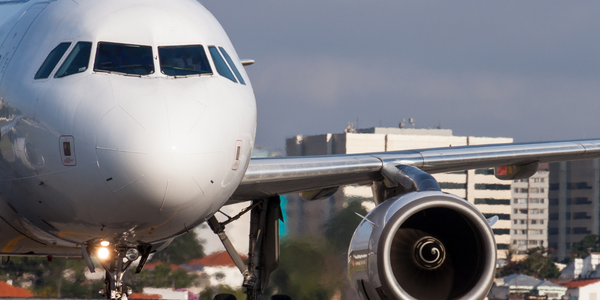
Case Study
Airbus Soars with Wearable Technology
Building an Airbus aircraft involves complex manufacturing processes consisting of thousands of moving parts. Speed and accuracy are critical to business and competitive advantage. Improvements in both would have high impact on Airbus’ bottom line. Airbus wanted to help operators reduce the complexity of assembling cabin seats and decrease the time required to complete this task.