公司规模
Large Corporate
地区
- Europe
国家
- France
产品
- EcoStruxure Plant
- Modicon M580 Ethernet programmable controller
技术栈
- IoT
- Ethernet
- Real-time data processing
实施规模
- Enterprise-wide Deployment
影响指标
- Productivity Improvements
- Environmental Impact Reduction
技术
- 功能应用 - 远程监控系统
适用行业
- 金属
适用功能
- 离散制造
- 维护
用例
- 机器状态监测
- 预测性维护
服务
- 系统集成
关于客户
ArcelorMittal is the world leader in steel manufacturing, and its Dunkirk plant is the largest steel factory in Western Europe. Every year, the Dunkirk steelworks delivers 7 million tons of steel for diverse industries, from automotive manufacturing to construction. With people’s safety depending on reliable steel, consistent product quality is paramount at any steel plant. Ensuring the continuity of the manufacturing process is another key issue as any interruption or equipment failure can be a costly event. Tackling equipment failures or performing routine maintenance usually means shutting down an entire section of a plant. Resuming normal production and bringing furnaces back to smelting temperatures can take up to two days. That’s why most steelworks run 24/7, 365 days a year.
挑战
ArcelorMittal, the world leader in steel manufacturing, operates the largest steel factory in Western Europe in Dunkirk. The plant delivers 7 million tons of steel annually for various industries. Ensuring consistent product quality is paramount, and any interruption or equipment failure can be costly. Regular maintenance is necessary to ensure safe working conditions and manufacturing continuity. However, performing maintenance usually means shutting down an entire section of a plant, which can take up to two days to resume normal production. ArcelorMittal needed to address this challenge and gain better control over its dust emissions to achieve greater operational flexibility for a recent equipment modernization project.
解决方案
Schneider Electric, a partner of ArcelorMittal for over 20 years, had the expertise and solutions to improve the dusting process for better steel quality, process reliability, and working conditions. The Modicon M580 offers a Change Configuration on the Fly (CCoF) feature, allowing maintenance and engineering teams to modify the automation control system without stopping the process. By implementing an IoT-enabled EcoStruxure Plant architecture, the Dunkirk steelworks has gained advanced connectivity that allows for precise dust level monitoring and better control of the entire process. The Modicon M580 has become “the brain” of the second phase dusting process, accountable for collecting and processing data from sensors.
运营影响
数量效益
Case Study missing?
Start adding your own!
Register with your work email and create a new case study profile for your business.
相关案例.
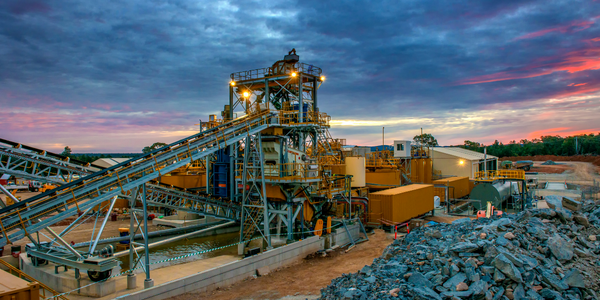
Case Study
Goldcorp: Internet of Things Enables the Mine of the Future
Goldcorp is committed to responsible mining practices and maintaining maximum safety for its workers. At the same time, the firm is constantly exploring ways to improve the efficiency of its operations, extend the life of its assets, and control costs. Goldcorp needed technology that can maximize production efficiency by tracking all mining operations, keep employees safe with remote operations and monitoring of hazardous work areas and control production costs through better asset and site management.
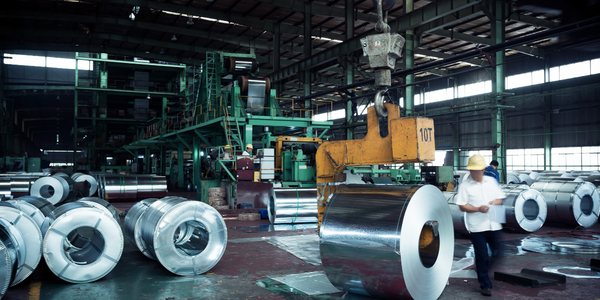
Case Study
KSP Steel Decentralized Control Room
While on-site in Pavlodar, Kazakhstan, the DAQRI team of Business Development and Solutions Architecture personnel worked closely with KSP Steel’s production leadership to understand the steel production process, operational challenges, and worker pain points.
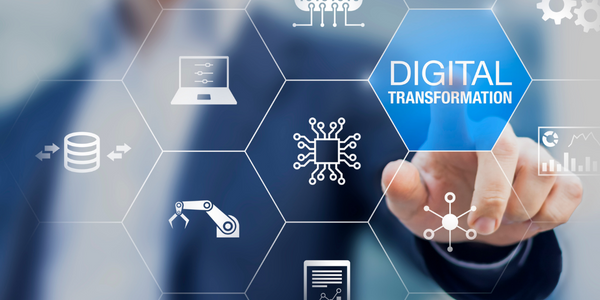
Case Study
Bluescope Steel on Path to Digitally Transform Operations and IT
Increasing competition and fluctuations in the construction market prompted BlueScope Steel to look toward digital transformation of its four businesses, including modern core applications and IT infrastructure. BlueScope needed to modernize its infrastructure and adopt new technologies to improve operations and supply chain efficiency while maintaining and updating an aging application portfolio.
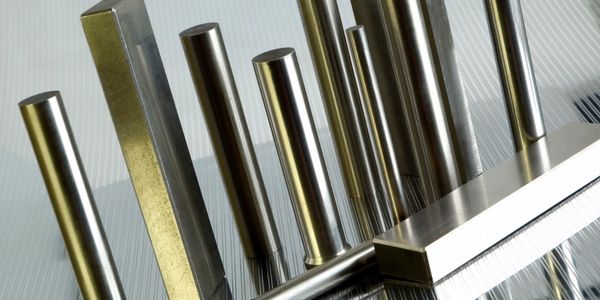
Case Study
RobotStudio Case Study: Benteler Automobiltechnik
Benteler has a small pipe business area for which they produce fuel lines and coolant lines made of aluminum for Porsche and other car manufacturers. One of the problems in production was that when Benteler added new products, production had too much downtime.
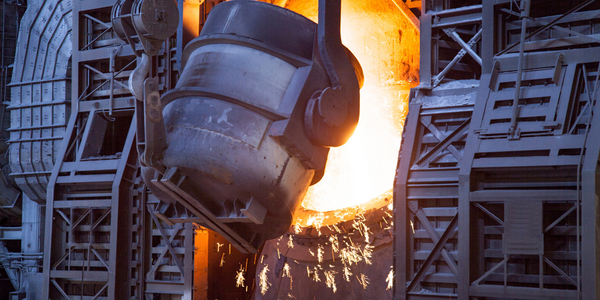
Case Study
Continuous Casting Machines in a Steel Factory
With a very broad range of applications, steel is an important material and has been developed into the most extensive alloy in the engineering world. Since delivering high quality is absolutely crucial for steel plants, ensuring maximum productivity and the best quality production are the keys to competitiveness in the steel industry. Additionally, working conditions in steel factories are not suitable for workers to stay in for long periods of time, so manufactures usually adopt various machines to complete the steel production processes. However, the precision of these machines is often overestimated and the lack of flexibility also makes supervisors unable to adjust operating procedures. A renowned steel factory in Asia planned to improve its Distributed Control System (DCS) of furnaces as well as addressing the problem of insufficient accuracy. However, most well-known international equipment suppliers can not provide a satisfactory solution and local maintenance because the project needed new technologies to more accurately control equipment operations. By implementing Advantech’s automated monitoring and control solution, steel factories can not only improve the manufacturing processes but can also allow users to add additional functions to the existing system so as to make sure the operation runs at high efficiency.
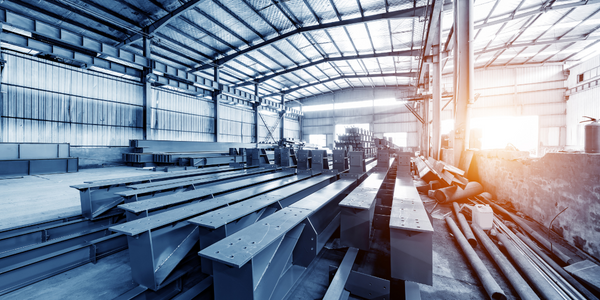
Case Study
Automated Predicitive Analytics For Steel/Metals Industry
Asset to be monitored: Wire Compactor that produces Steel RebarCustomer Faced The Following Challenges:Dependent upon machine uptime.Pressure cylinders within the compactor fail to control compression and speed causing problems in binding the coil.Equipment failure occurs in the final stage of production causing the entire line to stop, can you say bottleneck?Critical asset unequipped with sensors to produce data.