公司规模
Mid-size Company
地区
- America
国家
- United States
产品
- Sisense
- Sisense Elasticubes
技术栈
- Business Intelligence (BI)
- Data Aggregation
- Data Visualization
实施规模
- Enterprise-wide Deployment
影响指标
- Revenue Growth
- Customer Satisfaction
- Productivity Improvements
技术
- 分析与建模 - 大数据分析
- 应用基础设施与中间件 - 数据可视化
- 平台即服务 (PaaS) - 数据管理平台
适用行业
- 农业
- 建筑与基础设施
- 设备与机械
适用功能
- 商业运营
- 产品研发
服务
- 软件设计与工程服务
- 系统集成
关于客户
Equipment Data Associates (EDA) serves approximately 12 different industries by collecting, aggregating, and analyzing industry data for the purposes of extracting market insights. The company was founded in 1998 and today is a wholly owned subsidiary of Randall-Reilly. EDA serves industries that require financing heavy capital purchases like construction, machine tools, and agriculture. Its products service three major sectors in the industry: OEM (original equipment manufacturers) which are the companies building the equipment like John Deere or Caterpillar; the dealer network which includes companies who have exclusive rights within specific territories to sell the equipment; and “after-market” companies which are businesses that sell complementary services or products to the main industry (such as parts). Sonny Rivera, VP of Information Technology, has been working in the industry for nearly 25 years. When he started working at EDA about five years ago, data analysis was handled by one person who managed it all with an Excel spreadsheet. Throughout his time at EDA, Sonny transformed a 1-person technology team into a software product development team of about 15.
挑战
Sonny explains that before Sisense, company resources would be invested in reigning in data and wrestling with the complicated process of aggregating, processing and delivering it to the client. “We would build a bunch of pivot tables in Excel on numerous tabs, and then we would give people an import function that would import the raw data so that they could see the dynamic reports in Excel. But there were a number of problems, for example Excel would limit the amount of rows in a report, or the report was slow, or people just didn’t know how to use it.” Sonny also mentions that another significant problem was the task of distributing the data reports to thousands of different clients. To keep the reports current and updated, clients had to manually re-import the data, and eventually customization requests demanded even more time and resources, per client. “Overall, there just wasn’t control over what was happening. On top of that, if I had to update the report configuration, I had to send out thousands of new Excel files that had all the pivot tables defined in them. And ultimately every customer would need us to modify their pivot tables. It was just a nightmare.”
解决方案
EDA decided to build a web-based application that would allow users to access EDA’s products and define their own queries and filtering conditions. This solved the issue of updating and distributing the reports, but there was still something missing: insightful analysis. “Once the data was aggregated we asked ourselves, ‘What do we do with it?’ That was our problem. We needed a tool that would help us analyze the data. Our pain was going from being a data provider to an insight provider. Our clients wanted to know not only lists of data regarding the market, but also the trends and tendencies.” In addition to Sisense, Sonny investigated a number of major BI vendors, including Birst, QlikView, Tableau and Logi Analytics. The evaluation process included running the same test with each solution, side by side. A number of issues were explored, including the ability and speed of the tool to aggregate and process the data, the user interface, and the value and insights each managed to extract from the data. “We took our existing data and told ourselves that we need to build the tests based on that, running a full POC implementation using our own data. That was the litmus test. If we couldn’t outperform our current solution, then there wasn’t an advantage. We ran the same test on all the solutions so that we could see and compare how hard or easy it was to perform or how technical we needed to be and whether our consumers could potentially to it.” Each solution had its pros and cons, but none except Sisense had the “full package”. “Birst was too immature and costly; QlikView had memory and performance problems; Tableau’s user interface was great, but the analytics weren’t useful whatsoever. Tableau is pretty, but there’s no substance.” Sonny narrowed down the options to Logi XML and Sisense. While Logi XML worked well, the user interface and user experience were awkward, requiring a more technically savvy user to navigate through the system. That wouldn’t work within the company, or with EDA’s clients. After comparing all the tools, Sisense was the clear choice.
运营影响
数量效益
Case Study missing?
Start adding your own!
Register with your work email and create a new case study profile for your business.
相关案例.

Case Study
Smart Water Filtration Systems
Before working with Ayla Networks, Ozner was already using cloud connectivity to identify and solve water-filtration system malfunctions as well as to monitor filter cartridges for replacements.But, in June 2015, Ozner executives talked with Ayla about how the company might further improve its water systems with IoT technology. They liked what they heard from Ayla, but the executives needed to be sure that Ayla’s Agile IoT Platform provided the security and reliability Ozner required.

Case Study
IoT enabled Fleet Management with MindSphere
In view of growing competition, Gämmerler had a strong need to remain competitive via process optimization, reliability and gentle handling of printed products, even at highest press speeds. In addition, a digitalization initiative also included developing a key differentiation via data-driven services offers.
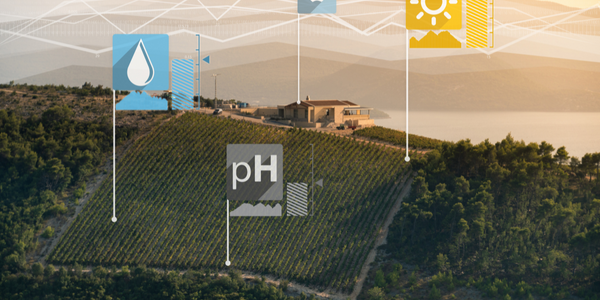
Case Study
Intelligent Farming with ThingWorx Analytics
Z Farms was facing three challenges: costly irrigation systems with water as a limited resource, narrow optimal ranges of soil moisture for growth with difficult maintenance and farm operators could not simply turn on irrigation systems like a faucet.
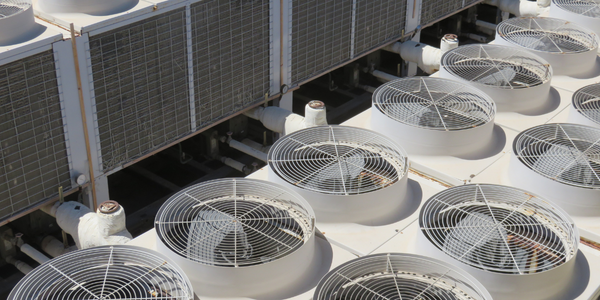
Case Study
Predictive Maintenance for Industrial Chillers
For global leaders in the industrial chiller manufacturing, reliability of the entire production process is of the utmost importance. Chillers are refrigeration systems that produce ice water to provide cooling for a process or industrial application. One of those leaders sought a way to respond to asset performance issues, even before they occur. The intelligence to guarantee maximum reliability of cooling devices is embedded (pre-alarming). A pre-alarming phase means that the cooling device still works, but symptoms may appear, telling manufacturers that a failure is likely to occur in the near future. Chillers who are not internet connected at that moment, provide little insight in this pre-alarming phase.

Case Study
Premium Appliance Producer Innovates with Internet of Everything
Sub-Zero faced the largest product launch in the company’s history:It wanted to launch 60 new products as scheduled while simultaneously opening a new “greenfield” production facility, yet still adhering to stringent quality requirements and manage issues from new supply-chain partners. A the same time, it wanted to increase staff productivity time and collaboration while reducing travel and costs.

Case Study
Integration of PLC with IoT for Bosch Rexroth
The application arises from the need to monitor and anticipate the problems of one or more machines managed by a PLC. These problems, often resulting from the accumulation over time of small discrepancies, require, when they occur, ex post technical operations maintenance.