公司规模
Mid-size Company
地区
- Asia
国家
- Malaysia
产品
- FORCAM FORCE
- Data Collection Units (DCU)
- Product Data Management (PDM)
技术栈
- Data Mining
- Data Visualization
- Real-Time Data Collection
实施规模
- Enterprise-wide Deployment
影响指标
- Productivity Improvements
- Cost Savings
技术
- 分析与建模 - 实时分析
- 应用基础设施与中间件 - 数据交换与集成
适用行业
- 金属
适用功能
- 离散制造
- 质量保证
用例
- 预测性维护
- 工厂可见化与智能化
服务
- 数据科学服务
- 系统集成
关于客户
C.S.YAP Group of Companies were established in 1976. Since then, C.S.YAP investment in machinery has exceeded 20 million Ringgit Malaysia. Over the years, C.S.YAP has become a market leader of metal parts to different kinds of industries in Malaysia. With over 30 years of proven track records, the experience and knowhow of management and staff, coupled with a well-equipped plant. The company prides itself with a special quality process and certification alongside shop floor management technology from FORCAM to help create high quality durable goods that are manufactured with highest attention to detail and craftsmanship. The goal is to eliminate problems with mass produced products and responsibly manage resources and waste. C.S.YAP’s goal is to become a world class solution provider from concept to completion of metal products through continuous investment in latest technologies and best metal fabrication services. Revenue target is US $40 million by 2020.
挑战
C.S.YAP Group of Companies, a market leader of metal parts to different industries in Malaysia, faced significant challenges in their manufacturing process. The process was complex and could be impacted by many factors such as supplies, equipment, factory overhead, the need for special parts, and the people who work at all points in the process. The more variables there were, the greater the possibility of disruption to the smooth operations of the factory. Management styles and workforce could also have an impact on this process. For instance, human insight into a manufacturing process leading to more labor-efficient and cost-effective methods of production could affect the manufacturing process in a positive way. Not only did the operator need to understand the basic machining operations, correct tool usage, and correct speed of operation but also detect tool wear and replacement patterns. Skilled machinists usually made these decisions based on experience with no written instructions other than a blueprint of the designed part. Often this involved setting up the machine tool, running a few pieces through to test the arrangement, and then adjusting the setup until an acceptable part was produced. This could be a time-consuming and a tedious process.
解决方案
C.S.YAP implemented a two-phase project with FORCAM's technology. In the first phase, they focused on Product Data Management & Digital Numeric Control (PDM-DNC). They used FORCAM FORCE to collect, analyze, and make decisions based on data. Data was stored in a central data warehouse and could be entered, accessed, and extracted remotely. Data was also preprocessed, transformed, modeled, analyzed, interpreted, and evaluated using a combination of techniques. This phase enabled C.S.YAP to spread product data into the entire Product Lifecycle Management (PLM) launch-process, in order to produce complex products. This significantly enhanced the effectiveness of the launch process and lowered the risk of human error during order data transfer. In the second phase, C.S.YAP moved forward to include real-time machine data collection, web visualization, and alerting. This implementation helped the workforce to utilize data generated through FORCAM FORCE to further scrutinize and increase shop floor efficiency.
运营影响
数量效益
Case Study missing?
Start adding your own!
Register with your work email and create a new case study profile for your business.
相关案例.
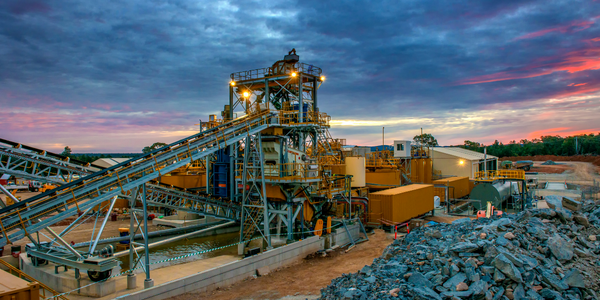
Case Study
Goldcorp: Internet of Things Enables the Mine of the Future
Goldcorp is committed to responsible mining practices and maintaining maximum safety for its workers. At the same time, the firm is constantly exploring ways to improve the efficiency of its operations, extend the life of its assets, and control costs. Goldcorp needed technology that can maximize production efficiency by tracking all mining operations, keep employees safe with remote operations and monitoring of hazardous work areas and control production costs through better asset and site management.
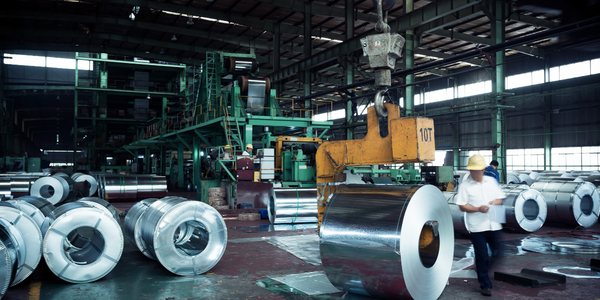
Case Study
KSP Steel Decentralized Control Room
While on-site in Pavlodar, Kazakhstan, the DAQRI team of Business Development and Solutions Architecture personnel worked closely with KSP Steel’s production leadership to understand the steel production process, operational challenges, and worker pain points.
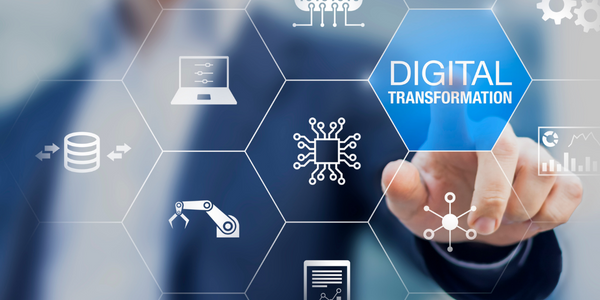
Case Study
Bluescope Steel on Path to Digitally Transform Operations and IT
Increasing competition and fluctuations in the construction market prompted BlueScope Steel to look toward digital transformation of its four businesses, including modern core applications and IT infrastructure. BlueScope needed to modernize its infrastructure and adopt new technologies to improve operations and supply chain efficiency while maintaining and updating an aging application portfolio.
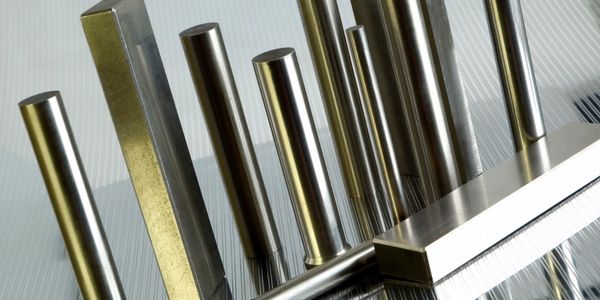
Case Study
RobotStudio Case Study: Benteler Automobiltechnik
Benteler has a small pipe business area for which they produce fuel lines and coolant lines made of aluminum for Porsche and other car manufacturers. One of the problems in production was that when Benteler added new products, production had too much downtime.
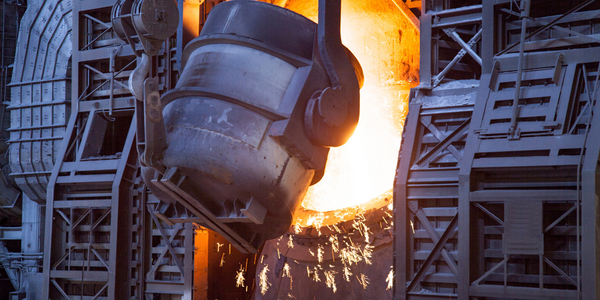
Case Study
Continuous Casting Machines in a Steel Factory
With a very broad range of applications, steel is an important material and has been developed into the most extensive alloy in the engineering world. Since delivering high quality is absolutely crucial for steel plants, ensuring maximum productivity and the best quality production are the keys to competitiveness in the steel industry. Additionally, working conditions in steel factories are not suitable for workers to stay in for long periods of time, so manufactures usually adopt various machines to complete the steel production processes. However, the precision of these machines is often overestimated and the lack of flexibility also makes supervisors unable to adjust operating procedures. A renowned steel factory in Asia planned to improve its Distributed Control System (DCS) of furnaces as well as addressing the problem of insufficient accuracy. However, most well-known international equipment suppliers can not provide a satisfactory solution and local maintenance because the project needed new technologies to more accurately control equipment operations. By implementing Advantech’s automated monitoring and control solution, steel factories can not only improve the manufacturing processes but can also allow users to add additional functions to the existing system so as to make sure the operation runs at high efficiency.
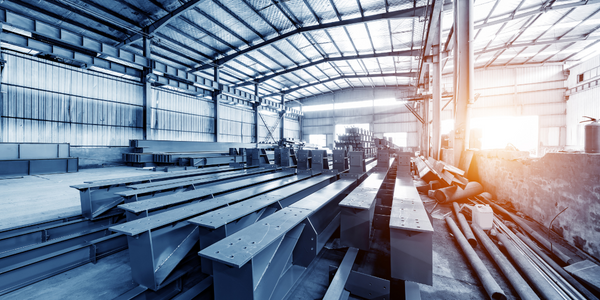
Case Study
Automated Predicitive Analytics For Steel/Metals Industry
Asset to be monitored: Wire Compactor that produces Steel RebarCustomer Faced The Following Challenges:Dependent upon machine uptime.Pressure cylinders within the compactor fail to control compression and speed causing problems in binding the coil.Equipment failure occurs in the final stage of production causing the entire line to stop, can you say bottleneck?Critical asset unequipped with sensors to produce data.