公司规模
Large Corporate
地区
- Europe
国家
- Germany
产品
- FORCAM FORCE
技术栈
- SAP ERP
实施规模
- Enterprise-wide Deployment
影响指标
- Productivity Improvements
技术
- 平台即服务 (PaaS) - 数据管理平台
适用行业
- 汽车
适用功能
- 离散制造
用例
- 自动化制造系统
- 预测性维护
服务
- 系统集成
关于客户
BorgWarner Inc. is a U.S. Automotive Supplier and market leader in the field of drive components and system solutions. The company supplies well-known manufacturers globally in America, Asia, and Europe. BorgWarner’s 19,250 employees generated total revenue of $ 7.1 billion in 2012 at more than 60 locations in 19 countries. A subsidiary based out of Markdorf in Germany, is the largest branch of the BorgWarner “Thermal Systems” division with a total of 12 production facilities. Core business segments in Markdorf include engine radiator systems for commercial vehicles as well as off-highway machines (agricultural and construction). The location in Markdorf has 320 employees and has also been continuously expanded since 1999 towards becoming a sales and development center. Global sales for the thermal systems division has been accounted for from Markdorf since August 2008.
挑战
BorgWarner Cooling Systems, a subsidiary of U.S. Automotive Supplier BorgWarner, aimed to optimize production at their German plant. The plant, which houses a total of 40 machines, was in need of a system that could systematically collect and process machine and operating data, visualize current process states online, and precisely analyze weak areas. The goal was to increase overall production efficiency. The challenge was to develop and implement an individual, custom-fit production management system that could meet these needs.
解决方案
FORCAM, an independent IT and consulting company, partnered with the BorgWarner team in Markdorf to develop and implement an individual, custom-fit production management system for the 40 machines in the plant. The system, FORCAM FORCE, systematically collects and processes machine and operating data. Current process states are visualized online and all weak areas, including technical, logistical, and organizational failures, are analyzed with precision. The system also integrates seamlessly with SAP ERP orders and operations to assist the operator at the shop floor level and increase productivity.
运营影响
数量效益
Case Study missing?
Start adding your own!
Register with your work email and create a new case study profile for your business.
相关案例.
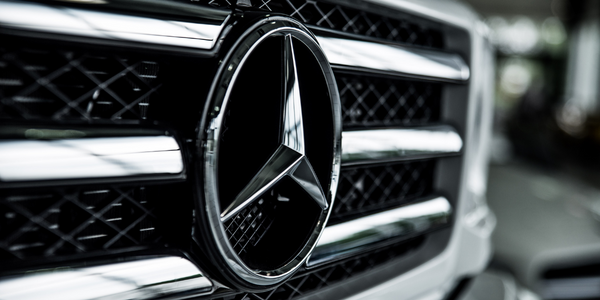
Case Study
Integral Plant Maintenance
Mercedes-Benz and his partner GAZ chose Siemens to be its maintenance partner at a new engine plant in Yaroslavl, Russia. The new plant offers a capacity to manufacture diesel engines for the Russian market, for locally produced Sprinter Classic. In addition to engines for the local market, the Yaroslavl plant will also produce spare parts. Mercedes-Benz Russia and his partner needed a service partner in order to ensure the operation of these lines in a maintenance partnership arrangement. The challenges included coordinating the entire maintenance management operation, in particular inspections, corrective and predictive maintenance activities, and the optimizing spare parts management. Siemens developed a customized maintenance solution that includes all electronic and mechanical maintenance activities (Integral Plant Maintenance).
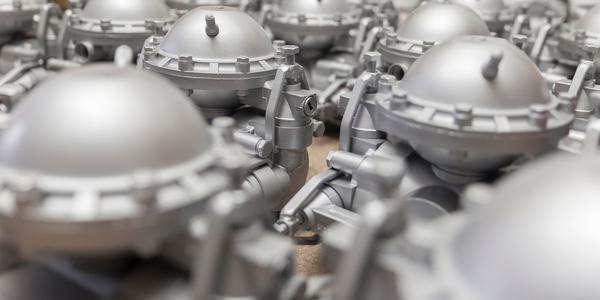
Case Study
Monitoring of Pressure Pumps in Automotive Industry
A large German/American producer of auto parts uses high-pressure pumps to deburr machined parts as a part of its production and quality check process. They decided to monitor these pumps to make sure they work properly and that they can see any indications leading to a potential failure before it affects their process.