公司规模
200-1,000
地区
- America
国家
- United States
产品
- GENESIS64
- BridgeWorX
- ReportWorX
- WebHMI
技术栈
- Microsoft SQL Server
- Microsoft Office
- Microsoft Access
实施规模
- Enterprise-wide Deployment
影响指标
- Cost Savings
- Productivity Improvements
技术
- 分析与建模 - 实时分析
- 应用基础设施与中间件 - 数据交换与集成
适用行业
- 海洋与航运
适用功能
- 离散制造
- 质量保证
用例
- 自动化制造系统
- 质量预测分析
服务
- 软件设计与工程服务
- 系统集成
关于客户
VEC Technology’s Greenville, PA. location provides custom composite manufacturing. Its parent company, J&D Acquisitions, also owns Larson Boats, a Little Falls, MN manufacturer of recreation boat hulls that utilizes the VEC process, “a patented, state-of-the-art, computer controlled manufacturing process that guarantees that every part is made to the most exacting standards of fit and finish, resulting in parts with unparalleled beauty and unprecedented quality.” VEC Technology considers itself a one stop shop for OEMs, providing part concepts, design, engineering, tooling and manufacturing, with seven molding stations at its Pennsylvania facility. The company states that manufacturing cells utilizing its Patented Floating Mold technology receive a “low-cost, high-quality, extremely accurate, closed-mold solution” and that VEC Technology has achieved “great success in the marine, construction, containers, transportation, farming equipment and recreational vehicle markets.” Larson Boats, itself a customer of VEC Technology, can process boat hulls in the 17 to 24 ft range at its Minnesota location, which includes eight molding stations and an automation mix plant.
挑战
VEC Technology required an HMI/SCADA solution coupled with data bridging/reporting/archiving that can be used over the Web, can integrate with the OPC communications protocol and can directly interface with the company’s product databases. They required the solution to control and monitor the company’s patented closed molding operations. They wanted a system that could manage various parameters based on several criteria, including the specific product being produced, ambient conditions and material properties. Also necessary was the ability to provide long term storage of multiple key parameters for product warranty information. The company sought a product with future-proof technology. They also looked for a solution that presented a simple user interface for making edits, as well as an easily maintained Web-based client/server architecture. VEC Technology aimed for a “single vendor” approach, intending to reduce both the number of automation interfaces as well as extra support staff to maintain various systems.
解决方案
VEC Technology selected ICONICS GENESIS64™ 64- bit HMI/SCADA software, in addition to BridgeWorX™ (real-time workflow for data bridging), ReportWorX™ (enterprise reporting, charting and analysis), OPC Server (supporting both OPC-UA and OPC-DA connectivity), and WebHMI (Web-based, real-time visualization). The engineers at VEC Technology allowed themselves a 10-month development cycle for the first installation, ensuring that their in-house personnel would become more familiar with the selected HMI/SCADA solution. The software would need to interface with multiple systems and hardware including eight Modicon PLCs between the two locations, five Delta RMC controllers, temperature/pressure/proximity gauges, scales and valves. The selected HMI/SCADA software would need to handle approximately 1,200 tags per molding station. VEC Technology maintains four servers and 16 client stations for this particular project. It uses several Microsoft applications including Microsoft Office, Access (to modify process input parameters) and SQL Server (for longterm historical data storage).
运营影响
数量效益
Case Study missing?
Start adding your own!
Register with your work email and create a new case study profile for your business.
相关案例.
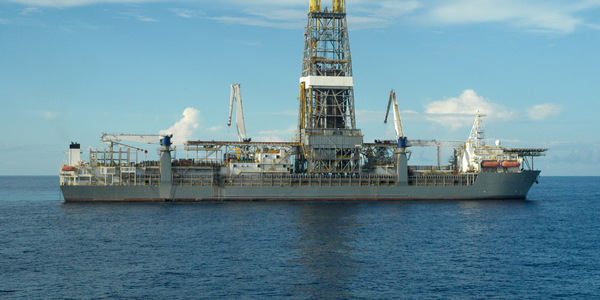
Case Study
Drill ship power challenge: hybrid solution solves distribution issues
Aspin Kemp & Associates (AKA), a manufacturer of electrical power and control systems headquartered in Montague, PEI, encountered one with its hybrid power initiative, the first hybrid drill floor destined for installation on ultra-deepwater drill ships operated by Transocean, Swiss offshore drilling contractors. Since on-site modification was impossible and scrap recycling of any modifications was unacceptable, the enclosures had to arrive ready-to-install.
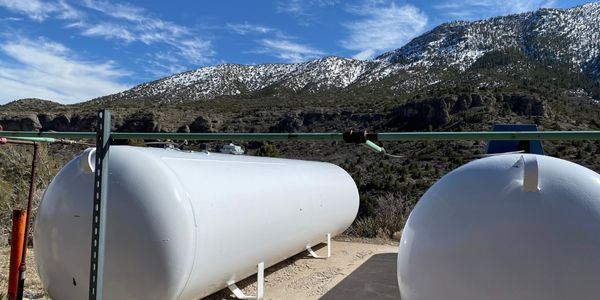
Case Study
Ensures Tanker Safety and Emissions Compliance
Storage tanks are irregular in shape and a certain amount of mathematical modelling is required to get an accurate representation of volume and, more importantly, the weight of material in each tank. In addition, countries have different emission regulations, so the ships position needed to be accurately known in order to geotag emission data.
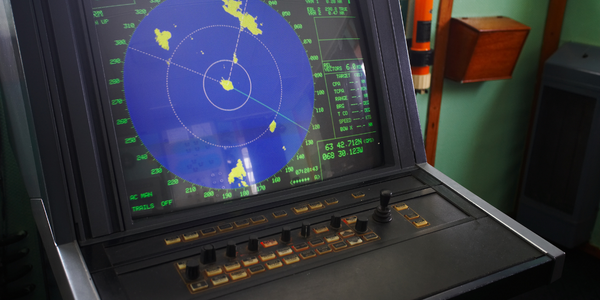
Case Study
Real-time Networked Sonar System for Ships
A multinational, knowledge-based corporation that delivers marine electronics solutions is utilizing industrial Ethernet technology to help ensure that operations at sea are dependable and optimal. Based in Europe, the company has nearly 4000 employees working in 20 countries around the world, and produces high-tech systems for offshore oil and gas operations, merchant marine systems, and various applications for the defense and aerospace industries. The company produces products and systems used by merchant vessels and offshore installations for positioning, navigation, automation, as well as for surveying and monitoring the seabed, and for fishing vessels and fi sheries research. As one of the major suppliers of high quality marine electronics in the world, their products include chart plotters for yachts, triple redundant dynamic positioning systems for oil drilling rigs, and sonar and instrument systems for scientifi c research vessels. Products used for marine applications must be rugged enough to endure the corrosive effects of salt water, and be able to withstand excessive amounts of vibration and shock. For this reason, the company only uses DNV and GL certified products and components to ensure that their systems can meet the high standards required by the maritime industry.
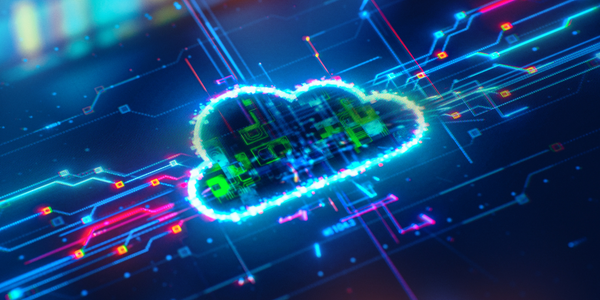
Case Study
Fleet Management Connectivity Solution for Marzam
Marzam, in order to ensure the best service, invested 3 million dollars in the construction of 2 fuel oil tanks with 40k gallons and 10k gallons capacity each, located in Manta, Ecuador. The customer needs to keep fleet operations going with fuel available at all times in order to guarantee quality of service. KEY ELEMENTS FOR THE CUSTOMER: Real-time level monitoring: Tank infrastructure remote level monitoring. Configure alerts and notifications when reaching critical values to avoid the need for emergency refills and optimize supply schedules. Real-time consumption monitoring: The customer needed an easy way to monitor in real-time accurate values of consumption.
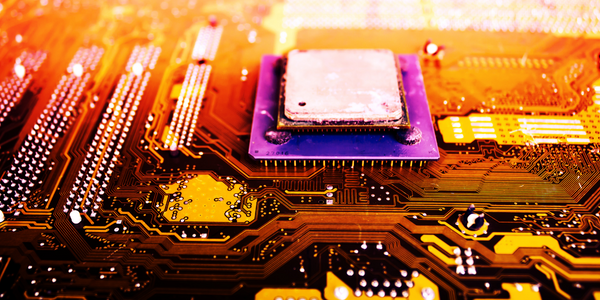
Case Study
Mitsubishi Electric's Edge Computing Solution Powered by Wind River VxWorks
Mitsubishi Electric Corporation, a global leader in factory automation (FA) applications, identified edge computing as a critical component of the Industrial Internet of Things (IIoT). The company aimed to enhance device and data security, reduce data traffic to the cloud, and enable faster response to network or device issues. In 2018, Mitsubishi Electric launched its first line of industrial hardware products designed for edge computing, the MELIPC Series. The primary development goals for MELIPC were to support the type of edge computing promoted by Mitsubishi Electric and to introduce advanced vision technology for device control. The flagship computer of the MELIPC line, the MI5000, was designed to combine real-time equipment control with high-speed data collection, processing, diagnosis, and feedback in a single machine. However, the development team needed a real-time control platform that could seamlessly integrate real-time control with proven analytic and diagnostic applications.
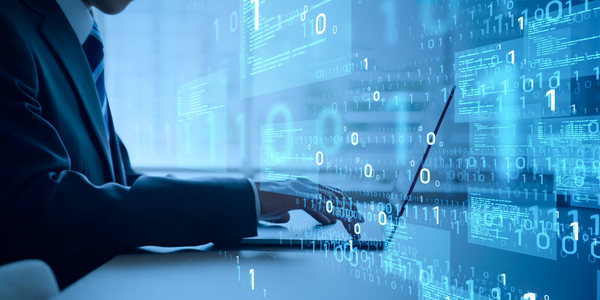
Case Study
Migrating to Software-Only Licenses for More Responsive License Management
The world’s premier shipping companies work with the software solutions of ABB Marine & Ports to get their vessels safely and efficiently to their destinations. A loyal customer of Wibu-Systems for over a decade, ABB has been relying on CodeMeter dongles to store the license keys for their ABB AbilityTM Marine Advisory System - OCTOPUS.The current version of the system is using Wibu-Systems’ robust metal-case CmStick ME, a perfect choice for the rugged conditions at sea. As satellite communications has made fast Internet connections at sea a common reality for maritime operators, the company is looking to move from physical to software solutions to streamline its logistics processes.