Creating an innovative drug delivery manufacturing system with SolidWorks software
公司规模
Large Corporate
地区
- America
国家
- United States
产品
- SolidWorks 3D CAD
- SolidWorks Simulation
- GibbsCAM
- SolidWorks eDrawings
- 3D ContentCentral
技术栈
- 3D CAD
- Finite Element Analysis
- Automated Machining
- Online Component Repository
实施规模
- Enterprise-wide Deployment
影响指标
- Productivity Improvements
- Customer Satisfaction
技术
- 功能应用 - 产品生命周期管理系统 (PLM)
- 分析与建模 - 预测分析
- 应用基础设施与中间件 - 数据可视化
适用行业
- 航天
- 消费品
适用功能
- 产品研发
- 质量保证
用例
- 预测性维护
- 过程控制与优化
- 远程协作
- 数字孪生
服务
- 软件设计与工程服务
- 系统集成
- 培训
关于客户
Remmele Engineering, Inc. is a leading provider of advanced manufacturing systems for various industries, including military equipment, aerospace, consumer products, and medical products. The company has a history of utilizing AutoCAD® 2D design tools but recognized the need to upgrade to a more advanced 3D CAD system to meet the demands of modern manufacturing. Remmele's engineers conducted a thorough evaluation of fifteen 3D CAD systems and ultimately selected SolidWorks® software for its ease of use, technical functionality, and strong local support.
挑战
Remmele Engineering, Inc. faced increasing complexity and diversity in automated systems, which highlighted the limitations of their existing 2D CAD tools. The company needed a more advanced design platform to handle new product-to-market ventures, innovative production processes, and pioneering manufacturing techniques. The goal was to improve communication, quality, and speed in the concept proposal, development, and production processes.
解决方案
Remmele Engineering selected SolidWorks 3D CAD software due to its ease of use, large assembly and configuration capabilities, robust design communication/animation tools, and ability to import/export AutoCAD data. The software's industry leadership position and strong local support were also key factors. SolidWorks enabled Remmele to handle complex projects, such as the development of an advanced manufacturing system for Aradigm Corporation's AERx® pulmonary drug delivery system. The 3D approach facilitated better communication with customers, improved quality control, and allowed for precise, high-volume production in a controlled environment.
运营影响
数量效益
Case Study missing?
Start adding your own!
Register with your work email and create a new case study profile for your business.
相关案例.
.png)
Case Study
Improving Vending Machine Profitability with the Internet of Things (IoT)
The vending industry is undergoing a sea change, taking advantage of new technologies to go beyond just delivering snacks to creating a new retail location. Intelligent vending machines can be found in many public locations as well as company facilities, selling different types of goods and services, including even computer accessories, gold bars, tickets, and office supplies. With increasing sophistication, they may also provide time- and location-based data pertaining to sales, inventory, and customer preferences. But at the end of the day, vending machine operators know greater profitability is driven by higher sales and lower operating costs.
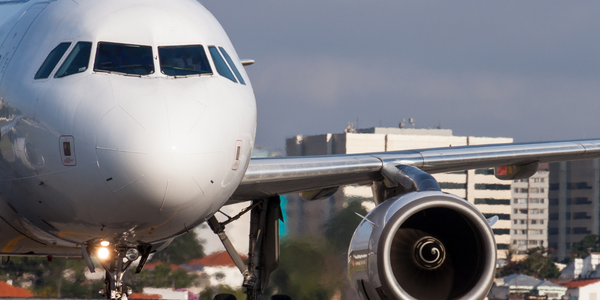
Case Study
Airbus Soars with Wearable Technology
Building an Airbus aircraft involves complex manufacturing processes consisting of thousands of moving parts. Speed and accuracy are critical to business and competitive advantage. Improvements in both would have high impact on Airbus’ bottom line. Airbus wanted to help operators reduce the complexity of assembling cabin seats and decrease the time required to complete this task.
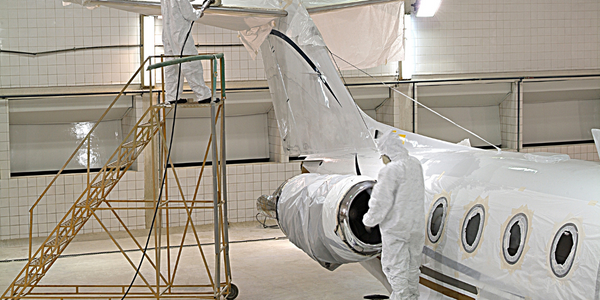
Case Study
Aircraft Predictive Maintenance and Workflow Optimization
First, aircraft manufacturer have trouble monitoring the health of aircraft systems with health prognostics and deliver predictive maintenance insights. Second, aircraft manufacturer wants a solution that can provide an in-context advisory and align job assignments to match technician experience and expertise.
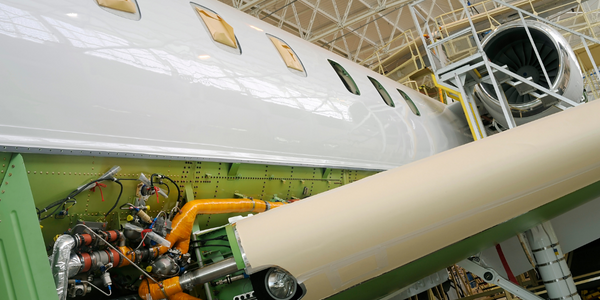
Case Study
Aerospace & Defense Case Study Airbus
For the development of its new wide-body aircraft, Airbus needed to ensure quality and consistency across all internal and external stakeholders. Airbus had many challenges including a very aggressive development schedule and the need to ramp up production quickly to satisfy their delivery commitments. The lack of communication extended design time and introduced errors that drove up costs.