Creating a data-driven, fix-to-root-cause culture
公司规模
1,000+
地区
- America
国家
- United States
产品
- GainSeeker Suite
技术栈
- Real-time data acquisition
- Analytics SPC software
实施规模
- Enterprise-wide Deployment
影响指标
- Cost Savings
- Customer Satisfaction
- Productivity Improvements
技术
- 分析与建模 - 预测分析
- 应用基础设施与中间件 - 数据交换与集成
- 功能应用 - 制造执行系统 (MES)
适用行业
- 消费品
- 电子产品
适用功能
- 流程制造
- 质量保证
用例
- 机器状态监测
- 预测性维护
- 过程控制与优化
服务
- 软件设计与工程服务
- 系统集成
关于客户
Hertzler Systems has been a leader in Statistical Process Control, SPC Software and Six Sigma for over twenty-five years. They provide the leading real-time data acquisition and analytics SPC software, the GainSeeker Suite. Hertzler Systems serves a diverse customer base, including BAE Systems, Crown Audio, McCormick & Company, Inc., Hormel Foods Corporation, Snyders of Hanover, Titleist & Footjoy, IDEX Corporation, and TaylorMade-Adidas Golf Worldwide. Their software and services enable clients to connect, collect, analyze, and visualize data, building a data infrastructure for making data-driven decisions. These capabilities help clients improve throughput and yield, improve cycle times, reduce costs and errors, and increase profitability.
挑战
Although the company had made major improvements to production throughput and first pass yield, they had reached a plateau and wanted to push through to the next level. To achieve this they needed better knowledge management, especially of repair data, in real time. Critical production repair data was being collected in a variety of ways in a host of different data systems. No standard processes were in place that prescribed or enforced what to do with data. Time to capture data was too high, and the data that was captured was not used effectively because it was not timely or accessible. The leadership team wanted to establish a company-wide, user-friendly database that would further their company's evolution into a data-driven, fix-to-root-cause culture. They knew they would have to refine and improve defect categorization, and define processes to enforce the use of data to investigate, resolve to root cause, and monitor quality.
解决方案
Hertzler Systems worked in concert with the customer's engineers to build a comprehensive, integrated data collection system that captures repair data from any one of eleven processes in real time. Once captured, all data resides in GainSeeker Suite in a single, central data repository. There it is accessible to all staff for tracking defect levels (DPMO) over time and for automated drill-down Pareto analysis. This system allowed the company to make repair data more accessible, visible, and timely. By doing so, they were able to reach previously unimagined yield levels. The solution also included refining and improving defect categorization and defining processes to enforce the use of data to investigate, resolve to root cause, and monitor quality.
运营影响
数量效益
Case Study missing?
Start adding your own!
Register with your work email and create a new case study profile for your business.
相关案例.
.png)
Case Study
Improving Vending Machine Profitability with the Internet of Things (IoT)
The vending industry is undergoing a sea change, taking advantage of new technologies to go beyond just delivering snacks to creating a new retail location. Intelligent vending machines can be found in many public locations as well as company facilities, selling different types of goods and services, including even computer accessories, gold bars, tickets, and office supplies. With increasing sophistication, they may also provide time- and location-based data pertaining to sales, inventory, and customer preferences. But at the end of the day, vending machine operators know greater profitability is driven by higher sales and lower operating costs.

Case Study
Remote Temperature Monitoring of Perishable Goods Saves Money
RMONI was facing temperature monitoring challenges in a cold chain business. A cold chain must be established and maintained to ensure goods have been properly refrigerated during every step of the process, making temperature monitoring a critical business function. Manual registration practice can be very costly, labor intensive and prone to mistakes.
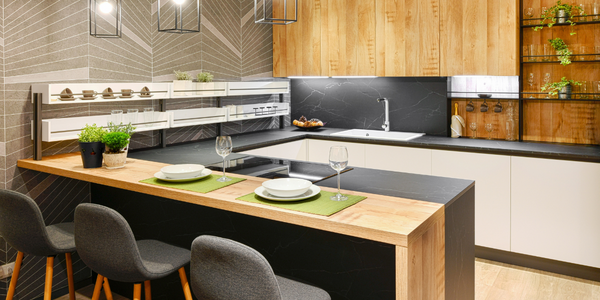
Case Study
Series Production with Lot-size-1 Flexibility
Nobilia manufactures customized fitted kitchens with a lot size of 1. They require maximum transparency of tracking design data and individual processing steps so that they can locate a particular piece of kitchen furniture in the sequence of processes.