Bringing Circular Manufacturing To Electronics
公司规模
Mid-size Company
地区
- America
国家
- Brazil
产品
- Sinctronics’ reverse logistics infrastructure
- Sinctronics’ Green IT Innovation Center
- Sinctronics’ Zero Waste Initiative
技术栈
- Reverse logistics technology
- Recycling facilities technology
- Reverse supply chain technology
实施规模
- Enterprise-wide Deployment
影响指标
- Environmental Impact Reduction
- Waste Reduction
- Innovation Output
技术
- 功能应用 - 库存管理系统
适用行业
- 电子产品
适用功能
- 物流运输
- 仓库和库存管理
用例
- 资产跟踪
- 库存管理
- 供应链可见性(SCV)
服务
- 系统集成
- 培训
关于客户
Sinctronics, a Brazilian company founded by Flex, is pioneering circular manufacturing processes that are making the information technology industry greener and more sustainable. The company describes itself as the first “integrated ecosystem” for sustainability in the electronics market. To succeed in circular manufacturing, it needed to build out four separate functions: reverse logistics, recycling facilities, R&D through its Green IT Innovation Center, and reverse supply chains. The company has had to invent virtually every process related to circular manufacturing. Sinctronics’ logistics infrastructure now covers all of Brazil, with dedicated vehicles in high-volume areas.
挑战
The modern world has a big electronics habit and it’s getting bigger all the time. Electronic devices keep us connected and on the go, but when they break or become obsolete—which is often very quickly—they frequently end up in the trash. Electronic waste, or e-waste, is a problem not only because of the volume of material that is being discarded, but also because some components can cause serious pollution. During 2014 alone, nearly 42 million tons of e-waste was created around the world. E-waste recycling is growing, however. In the United States, about 29 percent of e-waste was recycled in 2012, up from 19.6 percent in 20101. Better still, the world is recognizing that past recycling practices, such as sending devices to developing countries for disassembly and disposal (where they are often harmful to local environments) can be replaced with something better. That improvement is circular manufacturing, in which materials are collected to be refurbished or re-manufactured. Flex and Sinctronics realized that a market such as the region around São Paulo, Brazil, where manufacturing and re-manufacturing sites are close together, could help them showcase the true potential of a circular economy.
解决方案
Sinctronics began with reverse logistics, because that is the most expensive part of the entire process, accounting for about 60 percent of total cost. The company has had to invent virtually every process related to circular manufacturing. The company’s investment in innovation is driven by the belief that the new circular economy will ultimately be more efficient than the old linear model. The plastic parts produced by Sinctronics through its re-manufacturing process represent a savings of up to 82 percent on energy over normal plastics production, and an 82 percent reduction in greenhouse gas emissions. Thanks to the processes that Sinctronics has pioneered, 97 percent of recovered material is going back into the supply chain, with Sinctronics selling customers both finished products and reused raw materials that they can redevelop on their own. Sinctronics’ Zero Waste Initiative also means that less material is going to landfills. Sinctronics is improving circular manufacturing in other ways, too. One of the most radical changes has been its creation of a reverse logistics infrastructure. Reverse logistics was not common in Brazil, so logistics companies charged more for it than the regular process. Sinctronics developed partners for doing reverse logistics in an optimized way, tracking all the equipment and service levels involved.
运营影响
数量效益
Case Study missing?
Start adding your own!
Register with your work email and create a new case study profile for your business.
相关案例.

Case Study
Remote Temperature Monitoring of Perishable Goods Saves Money
RMONI was facing temperature monitoring challenges in a cold chain business. A cold chain must be established and maintained to ensure goods have been properly refrigerated during every step of the process, making temperature monitoring a critical business function. Manual registration practice can be very costly, labor intensive and prone to mistakes.
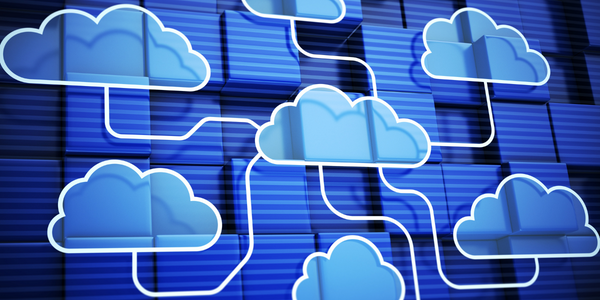
Case Study
Cloud Solution for Energy Management Platform-Schneider Electric
Schneider Electric required a cloud solution for its energy management platform to manage high computational operations, which were essential for catering to client requirements. As the business involves storage and analysis of huge amounts of data, the company also needed a convenient and scalable storage solution to facilitate operations efficiently.
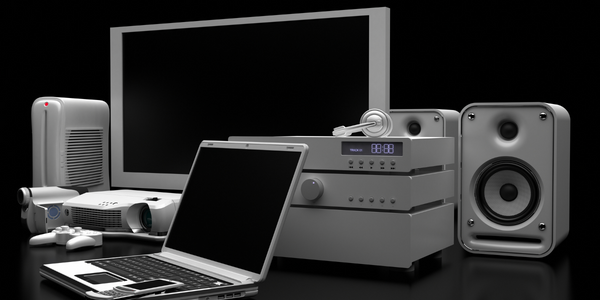
Case Study
Leveraging the IoT to Gain a Competitive Edge in International Competition
Many large manufacturers in and outside Japan are competing for larger market share in the same space, expecting a growing demand for projectors in the areas of entertainment, which requires glamor and strong visual performance as well as digital signage that can attract people’s attention. “It is becoming more and more difficult to differentiate ourselves with stand-alone hardware products,” says Kazuyuki Kitagawa, Director of Service & Support at Panasonic AVC Networks. “In order for Panasonic to grow market share and overall business, it is essential for us to develop solutions that deliver significant added value.” Panasonic believes projection failure and quality deterioration should never happen. This is what and has driven them to make their projectors IoT-enabled. More specifically, Panasonic has developed a system that collects data from projectors, visualizes detailed operational statuses, and predicts issues and address them before failure occurs. Their projectors are embedded with a variety of sensors that measure power supply, voltage, video input/ output signals, intake/exhaust air temperatures, cooling fan operations, and light bulb operating time. These sensors have been used to make the projector more intelligent, automatically suspending operation when the temperature rises excessively, and automatically switching light bulbs. Although this was a great first step, Panasonic projectors were still not equipped with any capability to send the data over a network.