Braskem Reduces Energy Usage by 20% with Aspen DMC3
公司规模
1,000+
地区
- America
国家
- Brazil
- United States
产品
- Aspen DMC3
技术栈
- Adaptive Process Control
- Aspen DMC3 Builder
实施规模
- Enterprise-wide Deployment
影响指标
- Energy Saving
- Productivity Improvements
技术
- 分析与建模 - 过程分析
- 应用基础设施与中间件 - 数据交换与集成
适用行业
- 化学品
适用功能
- 流程制造
用例
- 能源管理系统
- 过程控制与优化
服务
- 系统集成
- 培训
关于客户
Braskem is the largest petrochemical company in Latin America, the leading producer of polypropylene in the United States, and the eighth-largest resin producer worldwide. The company is positioned between extraction and plastic resin manufacturing, responsible for transformation from naphtha, natural gas, ethanol and salt into basic petrochemicals for polymer plants. The main final products Braskem produces are polyethylene (PE), polypropylene (PP) and PVC. Among basic petrochemicals, Braskem also produces solvents, aromatics and fuels. Since its founding in 2002, Braskem has been a major player in the international petrochemical market.
挑战
Braskem, a major player in the international petrochemical market, was facing challenges with variability in product quality, high energy usage, and excess reflux in their operations. The company had around 210 AspenTech advanced process control (APC) controllers installed among four Brazilian cracker sites. However, up until 2015, advanced process control was only installed on furnaces. The lack of an optimization algorithm on distillation columns resulted in lost potential benefits and unnecessary excess spending. There were frequent composition peaks and an excess of reflux, meaning excess utility spent on refrigeration compressors that use high pressure steam. Braskem decided to implement an optimization strategy using Aspen DMC3 to improve product quality and reduce project costs.
解决方案
Braskem implemented Aspen DMC3 on cold end units of ethylene site to reduce variations in quality and energy usage. The Adaptive Process Control technology in Aspen DMC3 allows simultaneous optimization and data collection with no interruptions to the process. Plant test data is used to build and update models which predict process response to manipulated variable moves and measured disturbances. That information is used to calculate the best moves to apply to the manipulated variables to stabilize production and push the process to the optimal point. Models are continuously adapted to represent unavoidable changing plant conditions. Braskem was able to implement Aspen DMC3 on their own with existing internal resources. In total, there were three engineers working on this project, all with less than five years’ experience.
运营影响
数量效益
Case Study missing?
Start adding your own!
Register with your work email and create a new case study profile for your business.
相关案例.
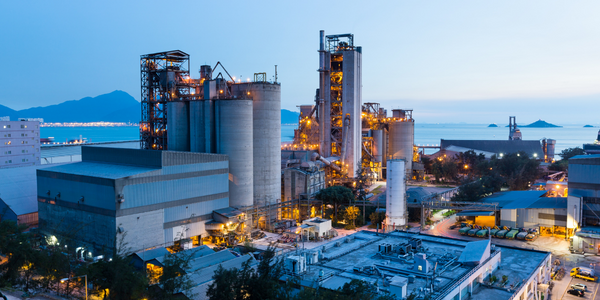
Case Study
Honeywell - Tata Chemicals Improves Data Accessibility with OneWireless
Tata was facing data accessibility challenges in the cement plant control room tapping signals from remote process control areas and other distant locations, including the gas scrubber. Tata needed a wireless solution to extend its control network securely to remote locations that would also provide seamless communication with existing control applications.

Case Study
Advanced Elastomer Systems Upgrades Production
In order to maintain its share of the international market for thermoplastic elastomers AES recently expanded its Florida plant by adding a new production line. While the existing lines were operating satisfactorily using a PROVOX distributed control system with traditional analog I/O, AES wanted advanced technology on the new line for greater economy, efficiency, and reliability. AES officials were anxious to get this line into production to meet incoming orders, but two hurricanes slowed construction.
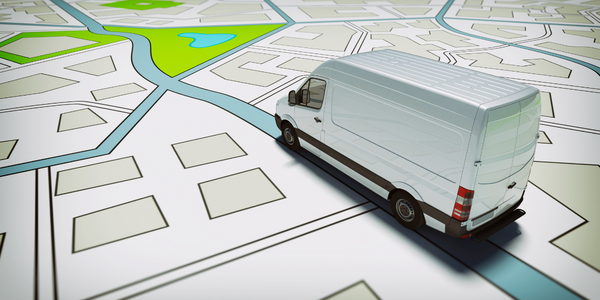
Case Study
Wireless GPS Tracking & Security Monitoring
Enhancing the security of hazardous freight and ensuring compliance with Homeland Security’s Transportation Security Administration mandate that all trains carrying chemicals capable of creating a toxic inhalation condition are equipped with on-board safety monitoring systems.
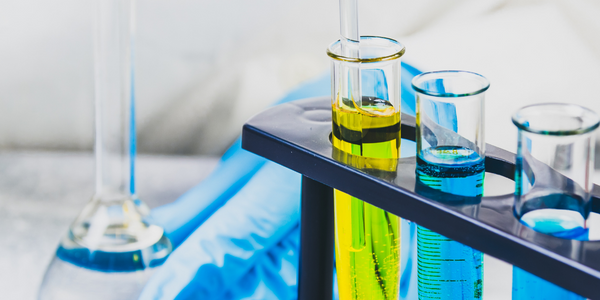
Case Study
Field Device Asset Management For Chemical Company in China
Chinese chemical subsidiary of multinational corporation serves customers throughout the world. Sales offices and research and technology centers are strategically located to provide rapid response to customer requests. Just two workers were assigned to maintain thousands of intelligent instruments in three production units, so they could do little more than react to device issues as they appeared. This costly maintenance method inevitably led to unexpected downtime when a critical instrument failed. Plant management recognized the need to change from reactive to predictive maintenance for all assets, including instruments and control valves, but help was needed in implementing such a technology-based initiative.
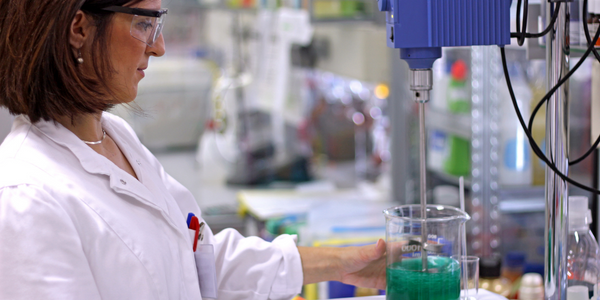
Case Study
Industrial Workforce Mobility for Improved Safety & Operations
Huntsman Corporation, a global manufacturer and marketer of differentiated chemicals, undertook an aggressive program to eliminate injuries, product defects, and environmental releases at their Port Neches facility. Termed “Project Zero”, this program required a completely mobile solution to empower operations and maintenance personnel to capture defects, track work progress and make process and safety related decisions in real-time.