Boeing 787: Global Supply Chain Management Takes Flight
公司规模
Large Corporate
国家
- United States
产品
- Exostar Supply Chain Management Solution
- e2open software
- Boeing 787 Dreamliner
技术栈
- Software-as-a-Service (SaaS)
- Enterprise Systems
实施规模
- Enterprise-wide Deployment
影响指标
- Cost Savings
- Productivity Improvements
- Customer Satisfaction
- Waste Reduction
技术
- 功能应用 - 企业资源规划系统 (ERP)
- 分析与建模 - 预测分析
- 网络与连接 - 网络管理和分析软件
适用行业
- 航天
- 运输
适用功能
- 物流运输
- 采购
- 质量保证
用例
- 供应链可见性(SCV)
- 预测性维护
- 库存管理
- 车队管理
服务
- 系统集成
- 软件设计与工程服务
- 云规划/设计/实施服务
关于客户
Boeing is a leading aerospace company and the largest manufacturer of commercial jetliners and military aircraft combined. The company also designs and manufactures rotorcraft, electronic and defense systems, missiles, satellites, launch vehicles, and advanced information and communication systems. Boeing has a long history of innovation and is known for its commitment to quality and safety. The company operates in more than 65 countries and employs over 140,000 people worldwide. Boeing's customers include airlines, government and defense organizations, and space exploration companies. The company is headquartered in Chicago, Illinois, and has major operations in the United States and around the world. Boeing's mission is to connect, protect, explore, and inspire the world through aerospace innovation.
挑战
The Boeing 787 Dreamliner represents a fundamental shift in manufacturing philosophy and approach for The Boeing Company. With 135 structural and systems partner locations around the world involved in the manufacturing and fabrication of the airplane, coordinating the end-to-end supply chain across these partners is paramount to the program’s success. One of the biggest challenges in this production model is ensuring that all partners have access and visibility to the latest demand information from Boeing and that Boeing has visibility to the supplier’s ability to meet the delivery schedule. It is crucial that all of the major subassemblies arrive in Washington at the same time for final assembly. If a subassembly is late or missing, there is very little time or space for Boeing to store the other large components. If a partner cannot meet an expected delivery date then Boeing must adjust the schedule and potentially delay the arrival of the other assemblies. Another critical success factor is to ensure continuity of supply of component parts being consumed by the Tier 1, volume partners. Due to the critical nature and dollar value of some of these component parts, Boeing retained contractual relationships directly with the Tier 2, providing partners. One of the benefits to the Tier 2 suppliers is shorter payment cycles. The challenge was implementing a pull-based replenishment model between the Tier 1 and Tier 2 partners that could be supported by the commercial relationship and payment process between Boeing and the Tier 2 partners. Above all else, Boeing and their partners needed a way to quickly identify potential problems across the supply chain and immediately assess their impacts on other partners or aspects of the manufacturing process. As an example, if a component part replenishment shipment was late, will it cause a potential stock out at a Tier 1 provider? If it will, then which delivery schedule will be impacted and against which finished airplane? What are the other subassembly production schedules that must be adjusted as a result? Having global visibility to process exceptions across the supply chain is critical to delivery performance.
解决方案
Boeing turned to Exostar for a solution to help manage processes executed across multiple tiers of their supply network. The Exostar Supply Chain Management Solution, powered by e2open software, is used to manage the complete order life cycle and returns process across the multiple partner tiers, while also tracking planning schedules, consumption, and managing replenishment for the Boeing Partner Managed Inventory program with Tier 2 partners. The Exostar solution is designed to allow Boeing and its partners to collaborate on planning schedules, issue purchase orders, track purchase order changes, exchange shipping information, manage returns, track shipments, and manage inventory consumption across the multiple tiers involved in the manufacturing process. The system also monitors events and process exceptions that occur between partners and evaluates the impacts of these events against the master schedule using synchronized time-sequenced information. The solution includes reporting capabilities that allow Boeing and its partners to track overall performance of the supply chain. Exostar’s software-as-a-service (SaaS) delivery model and existing network of connectivity into the A&D supply chain enabled Boeing to go live with the solution in less than 90 days from project kick off. Boeing was able to leverage its investment in Enterprise Systems to quickly connect to Exostar in order to enable its supply chain processes across the extended supply chain. Exostar’s solution was configured to meet Boeing’s current process requirements, and can evolve as process requirements or partners change over time. Leveraging the Exostar Supply Chain Management Solution to manage Boeing’s 787 program, was a logical decision for Boeing who has standardized on Exostar for managing their external information flow with supply partners. Exostar is a well-established technology and service provider to the A&D community, currently managing demand and supply processes between 20,000+ companies in the industry. The Exostar Supply Chain Management Solution is powered by e2open software. E2open software currently powers some of the world’s largest supply chain hubs in various industries including electronics, telecommunications, and heavy equipment.
运营影响
数量效益
Case Study missing?
Start adding your own!
Register with your work email and create a new case study profile for your business.
相关案例.
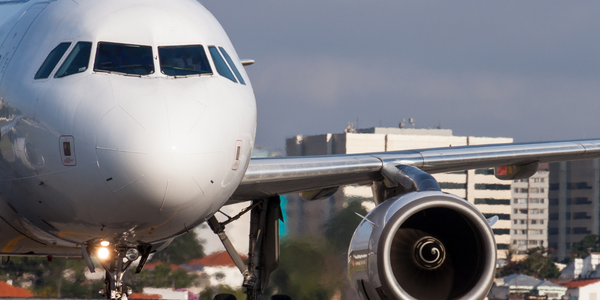
Case Study
Airbus Soars with Wearable Technology
Building an Airbus aircraft involves complex manufacturing processes consisting of thousands of moving parts. Speed and accuracy are critical to business and competitive advantage. Improvements in both would have high impact on Airbus’ bottom line. Airbus wanted to help operators reduce the complexity of assembling cabin seats and decrease the time required to complete this task.
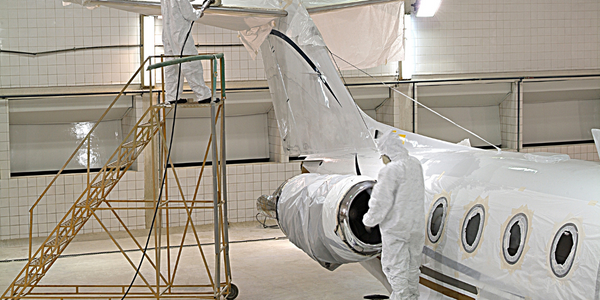
Case Study
Aircraft Predictive Maintenance and Workflow Optimization
First, aircraft manufacturer have trouble monitoring the health of aircraft systems with health prognostics and deliver predictive maintenance insights. Second, aircraft manufacturer wants a solution that can provide an in-context advisory and align job assignments to match technician experience and expertise.
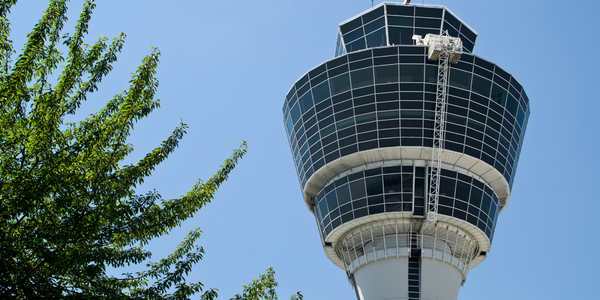
Case Study
Airport SCADA Systems Improve Service Levels
Modern airports are one of the busiest environments on Earth and rely on process automation equipment to ensure service operators achieve their KPIs. Increasingly airport SCADA systems are being used to control all aspects of the operation and associated facilities. This is because unplanned system downtime can cost dearly, both in terms of reduced revenues and the associated loss of customer satisfaction due to inevitable travel inconvenience and disruption.
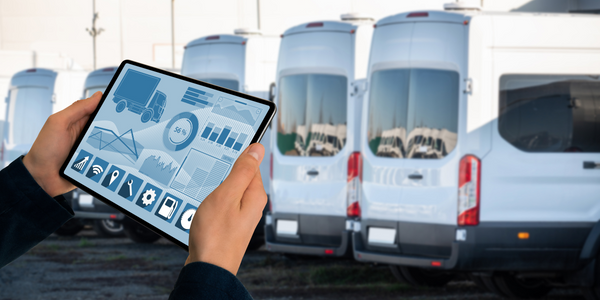
Case Study
IoT-based Fleet Intelligence Innovation
Speed to market is precious for DRVR, a rapidly growing start-up company. With a business model dependent on reliable mobile data, managers were spending their lives trying to negotiate data roaming deals with mobile network operators in different countries. And, even then, service quality was a constant concern.
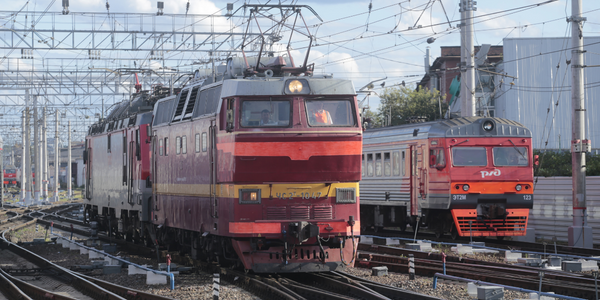
Case Study
Digitize Railway with Deutsche Bahn
To reduce maintenance costs and delay-causing failures for Deutsche Bahn. They need manual measurements by a position measurement system based on custom-made MEMS sensor clusters, which allow autonomous and continuous monitoring with wireless data transmission and long battery. They were looking for data pre-processing solution in the sensor and machine learning algorithms in the cloud so as to detect critical wear.
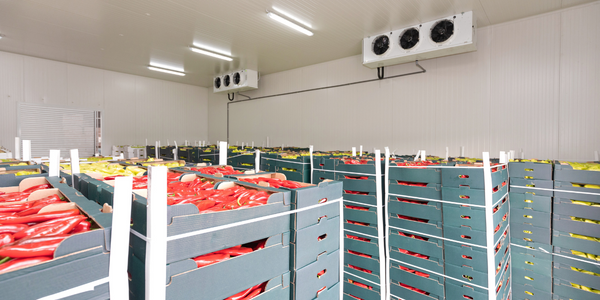
Case Study
Cold Chain Transportation and Refrigerated Fleet Management System
1) Create a digital connected transportation solution to retrofit cold chain trailers with real-time tracking and controls. 2) Prevent multi-million dollar losses due to theft or spoilage. 3) Deliver a digital chain-of-custody solution for door to door load monitoring and security. 4) Provide a trusted multi-fleet solution in a single application with granular data and access controls.